
EDUARDO CESAR
Polímero biodegradável produzido por bactériasEDUARDO CESARO forte aquecimento do mercado consumidor e a pressão nos custos das matérias-primas originadas do petróleo têm levado as indústrias de plástico a buscar, em fontes renováveis, matérias-primas substitutas para seus produtos. Plásticos feitos a partir do etanol de cana-de-açúcar, que podem ser reutilizados num processo de reciclagem, além de polímeros biodegradáveis produzidos por bactérias alimentadas por sacarose e outras substâncias estão na linha de frente de pesquisas e investimentos anunciados por gigantes petroquímicas como Dow Química, Braskem e Oxiteno, fabricantes de resinas plásticas feitas a partir da nafta e de outras matérias-primas derivadas do petróleo. A Braskem, líder latino-americana em produção de resinas, investiu US$ 5 milhões em pesquisa e desenvolvimento para chegar a um polietileno certificado a partir de álcool da cana, chamado de “polímero verde”.
As pesquisas que resultaram no novo produto tiveram início em 2005, embora desde 1998 a empresa já avaliasse as propriedades de outros polímeros de matérias-primas renováveis existentes no mercado. Como naquela época não havia ainda um mercado efetivo interessado em um produto desse tipo, o assunto não prosperou. “Ao retomar as discussões, avaliamos as opções existentes e começamos a trabalhar com o polietileno verde a partir do álcool de cana”, relata Antônio Morschbacker, gerente de tecnologia de Polímeros Verdes do Pólo Petroquímico de Triunfo, no Rio Grande do Sul, responsável pelo desenvolvimento do projeto.
As informações disponíveis apontavam que a empresa poderia chegar a um produto competitivo. “Ao longo de 2005, depois de estimativas de custos, vimos que seria viável fabricá-lo e, em 2006, decidimos construir a planta piloto e paralelamente fizemos um estudo mais aprofundado do mercado mundial”, diz Morschbacker. “O processo, bastante eficiente, transforma 99% do carbono contido no álcool em etileno, matéria-prima do polietileno.” O principal subproduto é a água, que pode ser purificada e reaproveitada.

PHD INDUSTRIAL
Plásticos rígidos fabricados pela PHB a partir do açúcarPHD INDUSTRIALDesidratação do etanol
Na planta piloto, que começou a funcionar em junho de 2007, é feita a transformação do etanol – obtido por um processo bioquímico de fermentação do caldo, centrifugação e destilação – em etileno. A conversão ocorre por meio de um processo de desidratação, no qual são adicionados catalisadores – compostos que aceleram as reações químicas – ao etanol aquecido, que permitem a sua transformação em gás etileno. A partir daí, para chegar ao polietileno, o plástico de maior utilização no mundo, o processo de fabricação é igual ao empregado para as matérias-primas provenientes de fontes fósseis, ou seja, o etileno polimerizado resulta no polietileno. A polimerização é uma reação em que as moléculas menores (monômeros) se combinam quimicamente para formar moléculas longas e ramificadas.
Com o etileno produzido por essa tecnologia é possível fazer qualquer tipo de polietileno. Inicialmente a Braskem pretende produzir resinas de alta densidade e de baixa densidade, para aplicações rígidas e flexíveis em setores como o automotivo, empacotamento de alimentos, embalagem de cosméticos e artigos de higiene pessoal. Alguns clientes, do Brasil e do exterior, já estão recebendo amostras do polímero verde produzido em escala piloto. O início da produção em escala industrial, que deverá chegar a 200 mil toneladas anuais, está previsto para o final de 2009. Por enquanto a empresa ainda não definiu onde será instalada a fábrica destinada à produção do novo polímero, que deverá demandar investimentos de cerca de US$ 150 milhões.
O produto, que deverá custar entre 15% e 20% a mais do que os polímeros tradicionais, será destinado, principalmente, aos mercados asiático, europeu e norte-americano. Antes mesmo de ser lançado em escala comercial, o polietileno verde já faz sucesso. Na Feira Internacional do Plástico e da Borracha – K 2007, o maior evento da indústria petroquímica, realizada no final de outubro em Düsseldorf, na Alemanha, Morschbacker fez dez concorridas apresentações do produto em oito dias e atendeu um grande número de interessados no produto e no projeto.
O polietileno de etanol foi certificado pelo laboratório Beta Analytic, dos Estados Unidos, pela técnica do carbono-14, como um produto feito com 100% de matéria-prima renovável. A matéria-prima utilizada, no caso o etanol, é renovável, mas o produto final não é biodegradável. “O produto possui propriedades idênticas aos polietilenos produzidos a partir do petróleo. Como é um plástico bastante resistente e estável, ele pode ser reciclado e reutilizado várias vezes e, no final da vida útil, pode ser incinerado sem causar nenhum problema ambiental”, diz Morschbacker. A grande vantagem ambiental do polietileno do álcool é que, para cada quilo de polímero produzido, são absorvidos em torno de 2,5 quilos de gás carbônico, o dióxido de carbono, da atmosfera pela fotossíntese da cana.
Pólo alcoolquímico
A Dow Química também prepara-se para produzir polietileno a partir do etanol. Em julho, a empresa anunciou uma joint-venture com a brasileira Crystalsev, trading brasileira de açúcar e álcool controlada pelas usinas Vale do Rosário, de Morro Agudo, e Santa Elisa, de Sertãozinho, ambas no interior paulista, para criação de um pólo alcoolquímico integrado, que deverá iniciar suas operações em 2011 e terá capacidade para produzir 350 mil toneladas por ano de polietileno de baixa densidade, chamado comercialmente de Dowlex, destinado à fabricação de embalagens flexíveis, filmes industriais e artigos injetados. A princípio, o produto será vendido no mercado interno, que tem crescido de 6% a 7% ao ano. O material já é produzido pela Dow a partir da nafta de origem petrolífera em unidades industriais localizadas na Ásia e na Europa.
Para transformar o etanol em polietileno, a Dow também utiliza o processo de desidratação. Modernos catalisadores permitem obter um etileno tão puro quanto o produzido a partir do petróleo. A água liberada durante o processo de transformação do etanol em etileno será utilizada no sistema de produção de vapor para geração de energia elétrica. As estimativas são de que o empreendimento gere cerca de 3.200 empregos diretos, além de centenas de indiretos nos setores agrícola, industrial e de manufatura. A fábrica de polietileno vai consumir 700 milhões de litros de álcool por ano, o que corresponde a 8 milhões de toneladas de cana-de-açúcar.
As duas empresas participarão como sócias em todas as etapas, a começar pela formação de um canavial de 120 mil hectares até a fabricação e comercialização do plástico. A integração completa do ciclo fará com que o pólo seja auto-suficiente do ponto de vista energético e gere excedente de energia suficiente, proveniente do bagaço da cana, para atender a uma cidade de 500 mil habitantes. Por enquanto ainda não foi definido o local em que o pólo petroquímico será instalado, mas estão sendo analisadas localidades na região centro-sul do país. “O preço do polietileno produzido a partir do etanol será estabelecido levando-se em consideração as mesmas forças de oferta e demanda que afetam o preço do polietileno produzido a partir da nafta”, diz Diego Donoso, diretor de Plásticos da Dow para a América Latina. “O cliente final irá receber um produto com as mesmas características técnicas e de performance do polietileno convencional, mas irá ganhar no valor agregado da produção.”

MIGUEL BOYAYAN
Planta piloto da PHB …MIGUEL BOYAYANHidrólise ácida
A Oxiteno, do Grupo Ultra, tem projeto similar ao da Dow para construir uma biorrefinaria que produzirá açúcar e álcool a partir de bagaço, palha e pontas da cana-de-açúcar, por meio de uma tecnologia chamada de hidrólise ácida, ainda não dominada em escala comercial e cujo fundamento é a quebra das moléculas de celulose por meio da adição de ácido sulfúrico aos resíduos. A futura unidade vai fabricar também produtos alcoolquímicos a partir de tecnologias não-convencionais.
Desde novembro de 2006 a empresa tem parceria com a FAPESP para desenvolvimento de projetos de pesquisa na área de tecnologia de produção de açúcares, álcool e derivados. Na primeira fase, em janeiro de 2007, foram escolhidos 23 projetos em parcerias com institutos de pesquisa e universidades, dos quais foram aprovados sete na segunda fase, em julho.
Enquanto as petroquímicas apostam nos plásticos a partir do etanol, a PHB Industrial, pertencente ao Grupo Pedra Agroindustrial, de Serrana, e ao Grupo Balbo, de Sertãozinho, ambos no interior paulista, tem fabricado desde dezembro de 2000, em uma planta piloto, um plástico biodegradável produzido por bactérias naturais, que está sendo vendido em pequenas quantidades, com o nome comercial de Biocycle, para Estados Unidos, Japão e países da Europa. A matéria-prima tem sido empregada principalmente na fabricação de plásticos rígidos produzidos pelo processo de injeção e também em espumas para substituição do isopor. O Biocycle também se aplica à produção de substitutos de poliuretanos, além de chapas bioplásticas e produtos termoformados.
A planta industrial para produção em grande escala, prevista para ficar pronta em 2010, será instalada na região de Ribeirão Preto. “A produção do plástico biodegradável deverá ficar entre 10 mil e 30 mil toneladas por ano”, diz o físico Sylvio Ortega Filho, diretor executivo do desenvolvimento do plástico biodegradável na PHB, que teve participação do Instituto de Pesquisas Tecnológicas (IPT), do Centro de Tecnologia Canavieira (CTC) e do Instituto de Ciências Biomédicas (ICB) da Universidade de São Paulo e financiamento do Programa Inovação Tecnológica em Pequenas Empresas (Pipe) da FAPESP (leia em Pesquisa FAPESP nº 80).
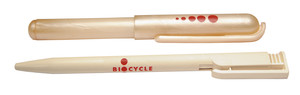
PHB INDUSTRIAL
…onde são fabricados produtos vendidos com o nome de BiocyclePHB INDUSTRIALPoliéster natural
A produção do polímero é feita pelo cultivo da bactéria Alcaligenes eutrophus, atualmente chamada de Cupriavidus necator, em um meio de cultura com a sacarose presente no açúcar. A sacarose é transformada em glicose para alimentar as bactérias. “A cadeia de carbono da glicose é transformada pela bactéria no polihidroxibutirato (PHB)”, explica a professora Elisabete José Vicente, do Instituto de Ciências Biomédicas (ICB) da USP, que participou dos estudos que resultaram no plástico biodegradável e atualmente orienta algumas linhas de pesquisa para a produção de polímeros a partir de bactérias. O PHB pertence ao grupo de polímeros denominados polihidroxialcanoatos (PHA), que são poliésteres acumulados por microorganismos na forma de grânulos intracelulares.
Suas propriedades termoplásticas permitem que, depois de extraídos do interior da célula produtora com o uso de solventes orgânicos, sejam purificados e processados, gerando um produto biodegradável, compostável e biocompatível. Esses polímeros podem ter aplicações diversas, como produção de filmes ou estruturas rígidas, além de usos médicos e veterinários, como confecção de suturas, suportes para cultura de tecidos, implantes, encapsulação de fármacos para liberação controlada e outras, utilizando-se da nanotecnologia.
“Até hoje já foram identificadas mais de 150 diferentes bactérias que acumulam naturalmente esse grânulo citoplasmático”, diz Elisabete. A bactéria C. necator se destaca porque consegue acumular grande quantidade de polímero, entre 80% e 90% do seu peso seco. Para crescer, ela precisa de frutose ou glicose. “O primeiro melhoramento genético da bactéria, realizado há muitos anos, obteve um mutante capaz de crescer em glicose, matéria-prima mais barata que a frutose”, diz Elisabete. No Brasil, as pesquisas iniciadas em 1992 pela pesquisadora em parceria com a professora Ana Clara Guerrini Schenberg, também do ICB, resultaram em uma nova bactéria mutante capaz de crescer em sacarose da cana e em outra bactéria recombinante com melhor rendimento de produção do co-polímero PHB-V, que é mais maleável.
Modificações genéticas
A bactéria fabrica naturalmente o polímero, mas os melhoramentos genéticos permitem que ocorra um aumento considerável da produção. No projeto desenvolvido entre a empresa PHB e as instituições parceiras foram desenvolvidas e patenteadas algumas bactérias geneticamente modificadas. “Estamos usando apenas a bactéria natural para produzir o biopolímero, porque a Europa proíbe organismos geneticamente modificados”, diz Ortega. A demanda para os polímeros de fontes renováveis concentra-se basicamente em três grandes aplicações no mercado mundial. A primeira é o mercado de embalagens. A segunda é a indústria automobilística, que está em busca de substitutos para os produtos utilizados nos carros por outros que não contribuam para o aquecimento global, exigência dos mercados europeus. E a terceira aplicação é na área médica (ver quadro na página 68).
A parceria com a PHB resultou não apenas em um produto que já está no mercado como também na continuidade das pesquisas na universidade. O grupo coordenado pela professora Elisabete, do ICB da USP, trabalha em duas frentes. Em uma delas, os pesquisadores procuram bactérias que consigam produzir polímeros a partir de outras fontes de carbono que não a sacarose, como os resíduos produzidos pela indústria. “Essa seria uma forma de baixar o custo da produção do biomaterial, que chega a três vezes o do plástico derivado do petróleo”, diz Elisabete. Paralelamente, o grupo estuda aplicações do biopolímero, depois de purificado, como substrato para o crescimento de células-tronco, linha de pesquisa conduzida em parceria com o professor Radovan Borojevic, diretor do programa avançado de Biologia Celular Aplicada à Medicina da Universidade Federal do Rio de Janeiro. Outra linha estuda o emprego do biopolímero para a imobilização de enzimas e fármacos, numa parceria com os professores Mário Politi, do Instituto de Química da USP e coordenador do Grupo de Pesquisas em Nanotecnologia do Conselho Nacional de Desenvolvimento Científico e Tecnológico (CNPq), e Carlos Alberto Brandt, integrante do mesmo centro de pesquisa.
Aplicações médicas
Fios de sutura para cirurgias, malhas para reforço na cirurgia de correção de hérnias, membranas para remendos de lesões venosas e artérias e tubos para enxertos arteriais são alguns dos produtos desenvolvidos pelo Grupo de Pesquisas Biopolímero de Cana-de-Açúcar, uma parceria entre a Universidade Federal de Pernambuco (UFPE) e a Universidade Federal Rural de Pernambuco (UFRPE). “Todos esses produtos foram aplicados em pesquisas experimentais com excelentes resultados”, diz o professor José Lamartine de Aguiar, coordenador do grupo. As pesquisas tiveram início em 1990, quando Francisco Dutra, engenheiro químico da UFRPE, identificou formações poliméricas no processo de fermentação para a produção de álcool. O biopolímero é obtido a partir de subprodutos da cana-de-açúcar, como o melaço. As características físicas e químicas do biopolímero após a sua purificação despertaram o interesse de pesquisadores de várias áreas. “Inicialmente o material foi aplicado em animais de experimentação, após os testes de citotoxicidade e biocompatibilidade”, diz Aguiar. A produção do biopolímero, patenteado pela UFPE, ficará a cargo de uma biofábrica que está em fase final de instalação na Estação Experimental de Cana-de-Açúcar de Carpina, campus avançado da UFRPE na região da mata pernambucana.
O Projeto
Obtenção e caracterização de polímeros ambientalmente degradáveis (PAD) a partir de fontes renováveis: cana-de-açúcar (nº 01/02909-9); Modalidade Programa de Inovação Tecnológica em Pequenas Empresas (Pipe); Coordenador Jefter Fernandes do Nascimento – PHB Industrial; Investimento R$ 338.686,30 (FAPESP)