
leo ramosLuma: slight modifications to take it to the Antarctic Oceanleo ramos
They do not talk and bear no resemblance whatsoever to the human body, though they have a backbone, two arms and two legs that allow them to go where no human being has ever set foot, or finds it very difficult to get to, such as the seabed and the swamps of the Amazon Region. Thanks to their capacity to replace humans, five machines, created by Brazilian researchers to work in water, basically, can be referred to as robots. One of them was created to inspect pipelines in the Amazon Forest. This robot will travel to the Amazon Region in November and will move around rivers and lakes on special wheels. Another one is used to inspect reservoirs and the marine environment and is scheduled to be taken this month to the South Pole to assist a survey being conducted on the fauna, algae and micro organisms in the Bay of Almirantado, the site of Brazil’s Antarctic research center. Two other robots will be guided by remote control based on software and sensor systems to inspect marine ducts, explore the seabed terrain and help in oil prospecting. The fifth machine is going through the last stages of preparation before being sent to inspect riverbeds and check the foundations of bridges. These five machines are the latest samples of this kind of technology, which is growing worldwide. Only a few Norwegian, Canadian and Japanese firms make robots, but a number of universities and research centers around the world are working on the development of robotic aquatic artifacts.
The Brazilian robot to be taken to Antarctica was initially devised to inspect underwater tunnels in hydroelectric power plants; these tunnels draw the water from the dams to the turbines. The robot was designed and built at the Postgraduate Engineering Center (Coppe) of UFRJ – Rio de Janeiro Federal University for Ampla, an electric power distributor, formerly called Companhia Elétrica do Estado do Rio de Janeiro/Cerj, to inspect the distributor’s hydroelectric power plants. Equipped with photo cameras, the robot has already been used to inspect dams. It was concluded in 2006, three years after the initial development. “This aroused the interest of my colleagues from the UFRJ Marine Biology Institute, after I suggested that they use the robot to explore the Antarctic Sea during the International Polar Year, from March 2007 to March 2009. We asked Ampla for a license and started to adapt Luma (the robot’s name) for the South Pole environment,” says professor Liu Hsu, the project coordinator. According to Hsu and researcher Ramon Romankevicius Costa, the robot was called Luma because the team consists only of men: apparently the name refers to Luma de Oliveira, queen of the percussion section of several Rio de Janeiro’s samba schools. This makes sense, but the researchers avoid the question.
The researchers’ biggest challenge now is to adapt Luma to dive 500 meteres down into the Antarctic Sea, because the robot was designed to operate 50 meters down at most. “To do this, we changed the structure, which had been made of aluminum, and used a polymer called acetal, which is very thick and resistant to deformation,” says Costa. Another adaptation is a very creative system of floaters made from PET bottles, the plastic bottles used for soft drinks and mineral water. These floaters are highly resistant and are used to offset the engine that pushes the robot to the seafloor. “If there is any kind of engine failure, Luma can rise up to the surface and drift,” says. “The floaters are pressurized up to 80 pounds, which is three times as much as the pressure in car tires.” In Antarctica there is much more pressure on the seabed, which the PET bottles cannot withstand. In October, the researchers were testing aluminum bottles and very rigid synthetic foam to replace the plastic.
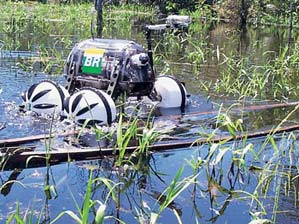
Cenpes/PetrobrasChico Mendes: tests in the Amazon region and detail of the mechanical arm at the lab in Rio de JaneiroCenpes/Petrobras
In the Antarctic Ocean, Luma will help to identify marine organisms. “We are going to collaborate with the Census on Antarctic Marine America that runs programs in the Antarctic (Brazil, Argentina, Chile, Uruguay, Peru and Ecuador). Brazil is leading four API projects to learn about biodiversity in the Antarctic Region, and in the long term, to find out whether those marine organisms are related to those that live on Brazil’s continental seacoast,” says professor Lúcia de Siqueira Campos, from the UFRJ Biology Institute and a member of the CAML scientific committee. “The robot will help us learn more about the seabed, through samples and records of marine organisms provided by cameras and sensors able to measure environmental characteristics like temperature and the amount of sunlight that reaches the seabed,” says Lúcia. In the cold waters of the Bay of Almirantado, a diver can only dive to a depth of 30 meters and can only remain in the water, with a suitable wet suit, for 15 to 20 minutes at most.
The testing performed to adapt Luma to the Antarctic environment included deep-freeze compartments – especially for the electronic components, the navigation sensors and three photo and video cameras. “One of these will be able to take high resolution photos and videos,” says Costa. He emphasizes that the navigation technology and the control software were developed at Coppe. The robot – 90 centimeters long, 60 centimeters high and 70 centimeters wide – will be equipped with four propulsion devices, or electric motors, that will run two propellers – and will be connected to the boat by two cables. One of the cables will feed power into the engines while the other will transmit control and navigation data and images. Water robots connected to boats by cables are referred to as Remotely Operated Vehicles/ROV.
Another ROV, of a non-diving kind, is called Chico Mendes, in honor of the environmental activist from the State of Acre, who was murdered in 1988. It was developed by the CENPES research and development center run by Petrobras in Rio de Janeiro. “This robot will float on water or mud and will be able to walk over floating plants, on sand and on stones, which is why it was called a Hybrid Environmental Robot”, says researcher and project coordinator Ney Robinson Salvi dos Reis.
The project arose from the company’s need to approve the 420-kilometer long Coari-Manaus gas pipeline, most of which crosses a part of the Amazon Jungle crisscrossed by rivers. The robot is part of Petrobras’s project Piatam, an acronym for Potenciais Impactos e Riscos Ambientais da Indústria do Petróleo e Gás no Amazonas (Potential Impact and Environmental Risks in the Oil and Gas Industry in the Amazon Region). “The question we asked ourselves was how to reach the points of interest in this complex ecological region without causing major damage. We needed an artifact that would be able to walk on this terrain and show us what is available there,” says Reis. “But the robot’s main objective was to travel over the gas pipeline and check possible leaks.” The monitoring will begin when the gas pipeline is ready in 2008.
Potentially, the Chico Mendes robot will also be able to help on environmental and public health research; it can eventually be used to transport products to the local population. Chico Mendes moves on wheels and a suspension system that recognizes the terrain. A computer system in the vehicle itself processes the information from the navigation sensors and automatically configures the traction set. It is teleoperated from a distance by a radio system and runs on power supplied by nickel batteries and solar panels.
The conception and development of the Chico Mendes resulted in three patents – one for the vehicle’s design, the second for the vehicle’s suspension and the third for the wheel. “We reinvented the wheel”, laughs Reis. In his opinion, the project’s success lies in the team’s multi-disciplinary characteristics, as it is comprised of several postgraduate and doctoral students, as well as technicians from universities and other research centers such as UFRJ, the Federal University of Santa Catarina, the Catholic University of Rio de Janeiro and the Federal University of Amazonas. Reis says that the biggest challenges to adapt the vehicle to the Amazon environment are the humidity and the radio signal, which is hindered by the jungle. After having taken the second tele-guided prototype to the region of the Coari-Manaus gas pipeline this month, Reis now plans to upgrade the Chico Mendes and transform it into a man-driven vehicle. “The vehicle going to the Amazon for the second time, to conduct sensor and navigation control tests is the M (medium-sized) model; the G model (big-sized) is in the industrial design phase.”
Another water robot developed in Brazil at the Polytechnic School of the University of São Paulo (Poli-USP) will be unable to carry a crew because if it gets any bigger it will become a submarine. An independent robot was designed that does not need power or control cables to connect it to a boat. It is called an AUV, the acronym for autonomous underwater vehicle. The AUV goes on ocean missions to conduct research on geological activities on the seabed and to aid in oil prospecting, a growing activity worldwide.
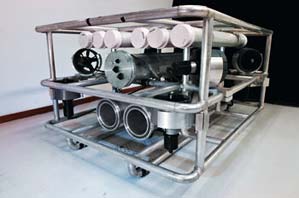
Juan Ávila/Poli-USPLaurs: configuration for going 2,000 meters deep, tested in USP poolJuan Ávila/Poli-USP
The Brazilian vehicle is called “Pirajuba,” i.e., “yellow fish” in the native Tupi language. It has been tested in the test tanks of the IPT Technological Research Center in São Paulo, where it underwent hydro-dynamic trials, which test how water resistance affects the vehicle’s shape and its behavior during maneuvers. Prof. Ettore Apolônio de Barros, of the Unmanned Vehicles Laboratory of Poli-USP’s Mechatronics Department is the project coordinator. He explains that robots of this kind navigate by themselves, as they are equipped with an on-board computer with instructions stored in the software. It is necessary to program the route, depth and other parameters, however, for the robot to sail to a specific place and back. The navigation system can be based on sonar signals, equipment which emits ultrasound waves. The sonar is used to calculate the distance between the transmitter and the receptor. The results of the hydro dynamic trials are also useful for saving energy, which is supplied by lithium batteries, similar to those in mobile telephone sets, or acid lead batteries, such those in automobiles. “We are studying the possibility of combining the lithium and the lead batteries.” The batteries move a propulsion device equipped with propellers.
Barros is working together with the Higher Technical Institute of Lisbon Technical University (Universidade Técnica de Lisboa) in Portugal, and with the Goa Oceanography Institute in India. “The Indians have the vehicle and I took the model on which we do hydro dynamic studies and used its geometry as a basis for another project and the construction of our AUV”, he says. “The experiments with the Portuguese AUV are normally conducted in the Azores; these vehicles study the local volcanoes, conduct terrain surveys on the seabed and collect plankton.” Barros says that these sea robots have a military tradition, having been developed in the former Soviet Union and in the US. They were widely used during the Gulf War in 1991. “The current AUVs derived from military use; in addition, computer-related costs have dropped. But it is hard to get the so-called high performance navigation inertial systems on the market. These systems are based on sensors with acceleration meters and gyroscopes (which inform the speed and vehicle inclination parameters) because this equipment can also be used for military purposes and is subject to the embargo that affects Brazil in this respect.” The solution is to combine sensors based on other more accessible technologies such as the sonar. A number of companies currently have prototypes or commercial AUVs in the US, Norway and Japan.
The AUVs are an alternative to the ROVs which are better known commercially because they have no limitations related to long cables, in addition to the operation being hampered by waves and sea currents close to the surface. However, the AUV’s lack of cables does not allow seabed images to be seen immediately by the boat crew, but the images can be recorded for subsequent viewing and analysis. The project coordinated by Barros has equipped the robot to navigate at a top speed of 2 meters per second (m/s). The values of the AUVs in operation range from 1 to 2,5 m/s. The hull is fiberglass, but it can also be made out of aluminum, steel or titanium, provided the material is light and resistant. The robot is 1.8 meters long and has a 0.24 meter diameter.
At another mechatronics lab at Poli, a group coordinated by professor Julio Cezar Adamowski is conducting integration and trials for another submarine robot prototype, designed for deep waters, called Laurs, the acronym for Laboratório de Ultra-som e Robótica Submarina, the University of São Paulo’s ultrasound and submarine robotics lab. The Laurs can also be considered a ROV because it has a thin cable for its remote control and video signals; or it can be considered an AUV, because it carries batteries. “As it has a cable used only for data transmission, the Laurs’ movements are simpler than those of a conventional ROV,” says Juan Pablo Julca Ávila, a doctoral student and team member.
The Laurs was initially conceived to retrieve transponders in deep waters, at a depth of some 2 thousand meters, and is used for the acoustic signaling that positions the vessels drilling for oil. This project began in 2000, as part of a program run by Cenpes/Petrobras and a research team from the Mechatronic Engineering Department of Poli-USP; the initial funding was provided by the Oil & Gas Sector/CTPetro fund. In addition to retrieving transponders, the Laurs can also be adapted for other jobs, such as collecting marine plants and animals. It is 1.2 m wide, 0.8 m high and 1.4 m long and it has already undergone trials in the Poli Naval Engineering and Oceanography Department testing tank and in the swimming pool of the USP Sports Center, to identify its hydro-dynamic parameters and test its control systems. New navigation sensors will be installed in the robot and more trials will be run before it goes to sea.
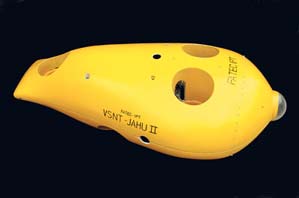
Antônio Amorim/Fate-JaúJaú II prototype and designAntônio Amorim/Fate-Jaú
Of all these advanced vehicles, the Jaú is the senior member of Brazil’s aquatic robots. A second version of the Jaú is being prepared by the College of Technology/Fatec in the city of Jaú. The Jaú I Veículo Submersível Não-Tripulado – VSNT (unmanned submersible vehicle) was developed from 1995 to 1998, under the coordination of professors Antônio Eduardo Amorim and Luís Alberto Sorani. The new version, Jaú-II, has already undergone its first hydro dynamic analysis trials at the IP testing tanks. The Jaús’ objective is to do underwater work connected with analyzing and inspecting structures such as bridges and dams and to check vessels’ hulls, underwater cables and the conditions of riverbeds. “The Jaú I was created with R$ 5 thousand donated by the Intermunicipal Consortium of the Valleys of the Tietê-Paraná Rivers; it is equipped with two tractor alternators converted into an electric motor. It has no on-board computer, but in 1998 it went 30 meters down at a lock on the Tietê River in the city of Barra Bonita and took pictures with a videocassette camera”, he recalls. The vehicle had a data cable and an image cable. “The Jaú II will have only one cable for image transmission via digital camera; the cable will also be used to transmit data and commands. It will have a computer and batteries on board to make it self-reliant,” says Amorim. The Jaú II relied on the collaboration of professor Hélio Morishita, from the Naval Engineering Department of Poli-USP, and professor Humberto Ferasoli Filho, from the Computer Sciences Department of Unesp state university in the city of Bauru.
The electronic systems being integrated include laser and sonar systems that will be attached to the cameras to determine the distance of obstacles during navigation. The vehicle will be equipped with six motors. “We employed a type of electric motor used in fishing, which makes the boat glide when the main motor is switched off whenever the boat approaches a school of fish. Our robot is made from the largest possible number of inexpensive and adaptable parts found on the Brazilian market.” The first test of the VSNT-Jaú II, scheduled for early 2008, will be held on a river in the central part of the state. The researchers believe that once the vehicle is ready, a company might be interested in acquiring the technology, or perhaps the students themselves will set up a company to provide services using the robot.
The Project
1. Development of technology for the inspection of adduction tunnels using an underwater robot; Coordinator Liu Hsu – Coppe-UFRJ; Investment R$ 380,000.00 (Ampla-Aneel)
2. Development of low-cost independent submarine vehicles. Part A: maneuverability and propulsion system (nº 05/55847-1); Modality
Regular Line of Research Grants; Coordinator Ettore Apolônio de Barros – USP; Investment R$ 78,750.00 (FAPESP)
3. Laurs underwater robot; Coordinator Julio Cezar Adamowski – USP; Investment R$ 300,000.00 (CTPetro-Finep) and R$ 150,000.00 (CTPetro-CNPq)
4. VSNT-Jaú II Submersible vehicle (nº 99/10493-5); Modality
Grant Program for Young Researchers; Coordinator Antônio Eduardo Assis Amorim – Fatec-Jaú; Investment R$ 55,560.00 (FAPESP)