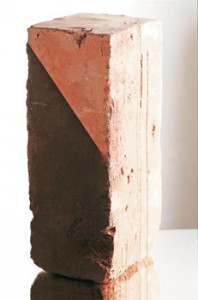
Brick made from a mixture of sand, cement and sludge from the paper industryMIGUEL BOYAYAN
The sludge resulting from the treatment of water effluents in paper manufacturing, comprised of materials such as kaolin – a kind of clay widely used by the porcelain industry – and pulp, was recycled in an innovative manner. This sludge was used in the production of cement compounds for civil construction, such as sealing blocks, interlocked flooring, and slabs for lining. Sand, cement and the residues from effluent treatment stations go through the adequate processing and form a mortar to which is added gravel to form the compounds. “The innovation is the composition of the material”, says professor Adriana Nolasco, from the Forestry Sciences Department of the University of São Paulo/USP’s Escola Superior de Agricultura Luiz de Queiroz/Esalq School of Agriculture in the city of Piracicaba, São Paulo State. Professor Nolasco is the coordinator of this research project. “A variety of products can be manufactured, based on the same technology.”
The proportion of sludge in the combination varies according to the application. The compression resistance tests showed that sealing blocks, dividing panels and compacted bricks – components that require higher physical-mechanical performance – can contain 5% to 10% of the residue, while lining slabs and thermo acoustic isolation panels can contain 20% to 30% of the residue material. Two companies with distinct manufacturing processes were chosen to participate in the research project. Papirus Indústria de Papel, from the city of Limeira, manufactures recycled cardboard from chips; the Piracicaba plant owned by Votorantim Papel e Celulose manufactures paper for printing and special paper from raw materials. The objective was to evaluate the performance of the compounds made from residues from various sources. The result showed insignificant variation in the performance of the materials that were obtained, which indicates that the same residues obtained under different conditions have the same application potential.
The study, conducted by Samantha Nazaré de Paiva, who is studying for her master’s degree under professor Adriana, resulted in the filing of a patent request for the material and the production process by the Agência USP de Inovaçã, Patent Requesting Agency. The study was also ranked first in the social and environmental solutions category at the Olimpíada USP de Inovação competition held last December. “Recycling the sludge makes it possible to manufacture new construction materials at a lower cost”, says the researcher. “It is also an environment-friendly solution, as the residue is suitably disposed of”.
Large volumes
Brazil is the world’s sixth largest cellulose manufacturer and the world’s eleventh largest paper producer. This ranking illustrates the huge volumes of these materials that are produced in Brazil. There are approximately 220 pulp and paper companies located in 17 states. Data from the 2007/2008 statistical report prepared by the Associação Brasileira de Celulose e Papel/Bracelpa, the Brazilian Pulp and Paper Association, states that 12 million tons of pulp and 9 million tons of paper were produced in 2007. The sludge from the effluents corresponds to approximately 1% of this production volume. These residues are discarded into industrial landfills, at an average cost of R$ 65,00 per ton, plus transportation costs. However, small companies still resort to landfills and city government garbage dumps, in violation of the law. A prior study conducted by Adriana shows that, to make production feasible, 100 kilometers is the longest distance that can separate construction material factories and paper manufacturers. “As these materials are going to compete with traditional construction materials, the logistic costs of the sludge for the factories have to be taken into consideration”, she says. The ideal situation would be to have regional production, in the vicinity of the paper manufacturers. “The companies could set up partnerships with the local governments or with third sector organizations to make it feasible for small businesses to produce these materials”.
By recycling the sludge from treatment stations, companies reduce transportation and disposal costs related to these residues. The companies that manufacture construction materials also benefit from this new technology. “They are able to produce high-quality material and reduce the costs of inputs”. The product is manufactured by using conventional technology, and the forms and sizes of the components are the same as those of the products on the market. The findings of this research study are the result of two decades dedicated to the recycling of residues. In 1989, during the presentation of her master’s thesis at USP’s São Carlos School of Engineering, Adriana produced a compound material from cement and the sludge from the paper industry. “It was a very light material for thermal-acoustic isolation, that could be used to substitute pre-fabricated Styrofoam panels”, says the researcher. The project did not move forward at the time, because Adriana was unable to find a commercial partner interested in manufacturing the material. But she did not give up. She continued concentrating on this line of research, which resulted in the development of ceramic blocks and bricks, comprised of this sludge and clay. In this project, conducted from 1993 to 1996, Adriana partnered with Votorantim de Piracicaba – the company was in charge of contacting potteries and ceramic manufacturers in Piracicaba. The results were different this time and the ceramic blocks made of residues went into commercial production immediately after the conclusion of the research study. Several companies started producing this product in 1996, having obtained the manufacturing permit from the Companhia de Tecnologia de Saneamento Ambiental/Cetesb, the State Environmental Authority. The ceramic industry also benefited, because as the residue is quite humid, the consumption of water for the production of ceramic blocks drops significantly. “The cellulose keeps the bricks from retracting before they are baked”, says Adriana. Many bricks crack when the clay retracts too much and material is lost. The cellulose disappears during the baking process, but the kaolin – a high quality clay – goes into action. “The ceramic material gains quality in finishing and impact-resistance”.
Republish