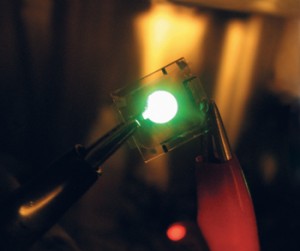
IMETROPrototype of flexible transparent display receives electric charge at the Inmetro laboratory IMETRO
In the near future, it will probably be unnecessary to accommodate a notebook inside a briefcase or knapsack when going on a trip – the notebook will be folded and put inside a pocket. This technological breakthrough will come true when flexible screens made from Foleds (the acronym for flexible organic light emitting device) enter the market in the near future. Several electronic equipment manufacturers – such as Sony, Philips, Fujitsu, and research groups around the world – are pursuing this objective. Among these is a group of Brazilian researchers from the Chemistry Institute of Paulista State University/ (IQ-Unesp), in the Araraquara campus, State of São Paulo, and from Inmetro, the National Industrial Quality, Standards and Metrology Institute in Rio de Janeiro. These researchers have recently developed a prototype of a Foled that uses a unique substrate based on biocellulose, a type of transparent paper that the researchers have named biopaper. The transparency of this biopaper is higher than 90% in the visible region of the electromagnetic spectrum, which means it lets through all the light that shines on it. The group of researchers, which is preparing to file a patent request for the novelty, introduced it to the scientific community in December 2008 in an article published in the journal Thin Solid Films.
In addition to palmtops, the flexible e-papers are also likely to be used for billboards, e-magazines, e-journals, restaurant menus and store posters, for example. Considered one of the most promising video and image technologies of the future, Foleds are an answer to the efforts to obtain an electronic device that combines the optic properties of paper, such as high reflectivity, flexibility, and contrast, with the dynamic capacity of the conventional digital displays that equip notebooks, mobile telephones and PDAs, the small palmtops used at retail facilities and restaurants. Glass is the most commonly used substrate in these devices, because glass is a transparent material with good mechanical resistance. It has, however, an obvious drawback: the difficulty of making displays for flexible or foldable equipment, as glass cracks easily. Polymers were the second material of choice, because they provide lighter, more flexible and portable systems, while keeping the requisite transparency and resistance. Several polymers, including PET (polyethylene terephthalate), cellulose acetate, polycarbonate and polyutherane have been used to produce flexible devices. The drawback is that, besides being synthetic or petroleum by-products, they require several additional treatments to generate the ideal material, and are often neither biocompatible nor biodegradable.
The advantages of the biocellulose substrate created by the Brazilians concern environmental factors, a simpler manufacturing process, and renewable raw material. Also referred to as bacterial cellulose/CB, biocellulose is made by the Gluconacetobacter xylinus bacteria, in the form of highly hydrated sheets that consist of water (99%) and cellulose (1%). Its production process generates no environmentally toxic residues, as is the case with the traditional cellulose production method. Because it is biodegradable and biocompatible, biocellulose can also be used in the manufacturing of medical devices. “Although it has the same chemical structure as plant cellulose, biocellulose has higher purity, crystallinity and exceptional mechanical resistance relative to plant cellulose,” explains chemist Younés Messaddeq, a professor at Lamf, the Photonic Materials Laboratory of IQ-Unesp.

EDUARDO CESARSubstrate of the flexible paper: production with no toxic wasteEDUARDO CESAR
When preparing the final version of the transparent paper, the researchers incorporated a hybrid system containing alumina and syloxane, a silicon-based polymer, into the microfiber structure of the biocellulose membranes. This addition increased the biopaper’s transparency from an index of roughly 40% in the visible region of the electromagnetic spectrum to more than 90%, says Hernane Barud, who is working on his PhD in chemistry at Lamf. The synthesis of the alumina-syloxane hybrid material was part of the doctoral thesis prepared of researcher José Maurício Almeida Caiut, who has a post-doctorate grant from FAPESP at IQ-Unesp.
Own light
The structure of biocellulose consists of a three-dimensional network of nanometric dimensions (measurements equivalent to one millimeter divided by one million) – the nanocelluloses. It has a wide range of applications, including medicine, as a temporary skin replacement in dressings, already on sale, produced by the firm Fibrocel, in the city of Londrina, State of Paraná. It can also be used in the food industry, to make dietary fibers, such as coconut cream, or to make flexible substrates for the deposition of Oleds (organic light emission devices). The advantage of Oleds relative to conventional displays (plasma, LCDs) is its capacity to produce its own light. Its structure is based on the placement of two organic layers between two conducting materials. When an electric current goes through it, the device emits brilliant light, in a process called electroluminescence.
The prototype prepared by Unesp and Inmetro is based on the manufacturing of Oleds over biopaper, a flexible substrate. The structure resembles that of a sandwich. It consists of nanometric films with specific properties and functions. The substrate, in turn, consists of biocellulose, a layer of conducting material, and a layer of silicon dioxide (SiO2), whose function is to eliminate the paper’s roughness, as this interferes with the electric conduction of the device. In this case, the conducting material is tin-doped indium oxide or ITO, which is used in the manufacturing of liquid crystal displays.
Unesp’s task was to create the biocellulose and the biopaper, while Lador, the Organic Devices Laboratory of t Inmetro’s science metrology division was in charge of manufacturing and characterizing the Foled. “One of our lab’s missions is to conduct metrological research of new technologies based on organic materials. In addition, our mission is to support national industry and other research and development centers focused on developing and characterizing materials,” says Cristiano Legnani, a researcher at Lador. “We have conducted research on glass substrate Oleds at Inmetro since 2006, as well as on polymer flexible substrates, such as polyutherane and polyetherimide.”
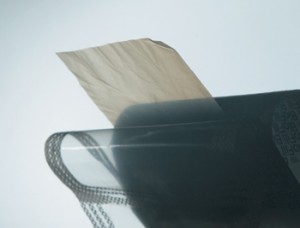
EDUARDO CESARDressing made from bacteria cellulose is already available on the marketEDUARDO CESAR
The race for success
Researcher Marco Cremona, a professor at the Physics Department of the Catholic University of Rio de Janeiro/PUC-Rio and head of Lador, visited the city of Araraquara in 2005. During his visit, he became acquainted with the biocellulose research of professors Messaddeq and Sidney José Lima Ribeiro. The interest in jointly developing a flexible device stemmed from this meeting. According to Messaddeq, using biocellulose for the manufacturing of Foleds is a pioneering event, although a Japanese group from Kyoto University’s Research Institute for Sustainable Humanosphere has already successfully developed a prototype that used a substrate made from plant cellulose. This group, however, has not produced a final product yet.
Researchers Marco Cremona, Cristiano Legnani and Welber Quirino also hope that the innovation they created will be used in photodynamic therapy for the treatment of skin cancer and other skin diseases. The use of a flexible substrate with biocompatible properties, such as biocellulose, is crucial for the development of this technology. The conventional therapy uses photosensitizing medication that is applied to the patient and concentrates on the tumor, on which a beam of light (laser or LED) is focused to destroy the damaged tissue. With the Foled, which would run on a battery smaller than that of a mobile phone, the medication would be embedded in the device and the device would then be placed on the skin. “As it emits its own light, the patient would be able to go home and carry out his normal daily activities, without having to stay at the clinic to get the conventional light treatment ,” Legnani explains.
According to Messaddeq, the initial results of the biocellulose Foled resembled those obtained with similar glass devices. However, it is still necessary to reduce the roughness of the surface of the biocellulose membranes and thus increase the electroluminescent efficiency of the e-paper. Once this is achieved, the technology can be passed on to industry. “The efficiency, which is the ratio between the quantity of light power provided by the device and the electric power used for this purpose, must be at least comparable to that of the devices currently on the market (such as LCD displays),” says Messaddeq. In his opinion, the most optimistic forecast is that the first Foled-based products will be on the market in 2015.
Scientific article
LEGANI, C. et al. Bacterial cellulose membranes as flexible substrates for organic light emitting devices. Thin Solid Films. v. 517, p. 1016-20, Dec. 2008.