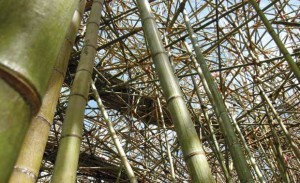
Bamboo is used in more than 5 thousand ways in oriental countries, ranging from edible bamboo shoots to construction of bridges and buildingsKRIS ARNOLD / WWW.FLICKR.COM/PHOTOS/WKA/4610770284/IN/SET-72157624068821508
Light, flexible and highly resistant, bamboo is becoming increasingly more popular as a material that can substitute other materials used in industrial applications, such as the wood used for manufacturing furniture. It can be used to substitute sand in cement mortar, or as a structural element in civil construction. In addition to being an excellent way to capture carbon dioxide (CO2) from the atmosphere, as it uses CO2 to form its woody tissue, bamboo is renewable material which continues flourishing annually after it is pruned; therefore, there is no need to plant new seedlings. Every bamboo-planted hectare absorbs nearly 10 tons of carbon gas per year. Of the approximately 1,300 species of bamboo that exist in the world, 19 species are considered priority, that is, they actually have various uses and have proven economic value.
In Brazil, 232 native species have been identified so far, of which approximately 80 are endemic – that is, they exist only in Brazil. Each species has distinct physical and chemical characteristics, such as diameter, wall thickness, and height, which results in special uses. “The plant moves from the edible shoot stage to a height of up to 30 meters in a few months – which is incredibly fast,” says professor Marco Antônio dos Reis Pereira, from the School of Mechanical Engineering at Paulista State University (Unesp) Bauru campus, in the State of São Paulo. Professor Pereira has dedicated himself to studying this giant grass plant since the 1990’s, when he was working on his master’s thesis.
Pereira’s master thesis focused on the use of bamboo in an irrigation system for small areas. At that time, he started planting this grass on the Unesp campus and now has a collection of 25 species, 11 of which have economic value. “Every year, I gather more than 400 bamboo culms to use in my research studies,” says Pereira, author of the book Bambu de corpo e alma, published in 2007. He wrote the book together with professor Antonio Ludovico Beraldo from the School of Agricultural Engineering at the State University of Campinas (Unicamp). The culm is the cylinder-shaped stem, a characteristic of grass plants, with visible nodes and internodes, as seen in bamboo and sugar cane. Unprocessed bamboo can be used for building sheds and for other applications; in addition, bamboo stems can be cut up into small strips, and glued on the sides, to be used in the manufacturing of plates for making furniture, decorative objects, plaques and flooring.
Bamboo anatomy
“Our studies are focused on the field of product design and on the physical and mechanical characteristics of the species, such as traction, compression, flexion, retraction, and swelling,” says Pereira, who also teaches design in the university’s post-graduate program. Pereira has partnered with professor Mário Tomazello Filho, from the University of São Paulo (USP)’s Luiz de Queiroz Higher School of Agriculture, in the city of Piracicaba, São Paulo State, to develop one of the 12 research projects funded since 2008 by the National Council of Scientific and Technological Research (CNPq), the focus of which is the study of bamboo and its different characteristics. Tomazello, who is coordinator of the project, does research work on bamboo anatomy.
“Brazil does not have any more hardwood for making furniture, because we have already depleted all the biomes where this kind of wood existed in large quantities,” says Pereira. Wood from reforestation, basically plantations of eucalyptus and pine trees, is now being used for this purpose. “Everything made from wood can also be made of bamboo, because the two plants are chemically similar.” However, wood and bamboo differ in terms of their anatomy- bamboo is hollow. “Although bamboo has been used for thousands of years, it is viewed as the material of the future, because it grows very fast and captures a considerable amount of CO2 from the atmosphere,” he points out. Eucalyptus trees take 20 to 30 years before they can be transformed into products and structures, while it takes only four years for the culm of the giant grass to reach the adult – or mature – stage with the adequate mechanical structure. A bamboo shrub takes eight to ten years to reach the adult stage – depending on the climate and soil conditions – when it is planted as a crop. In oriental countries such as China, India and Japan, the plant has more than 5 thousand listed uses, ranging from the edible shoot and the production of vinegar and baskets, to the construction of bridges, temples and five-story buildings. The structure of the dome of the 400-year old Indian monument Taj Mahal, for example, is made of bamboo. One of the specific characteristics of this plant is the fact that it has the same diameter when it is young as it does when it reaches the adult stage.
At the Federal University of Santa Catarina (UFSC), the research group headed by professor Carlos Alberto Szücs, from the Civil Engineering Department, is also working on a project with glued laminated bamboo, in partnership with Oré Brasil, a company located in the city of Campo Alegre, State of Santa Catarina, and with the Santa Catarina State Bamboo Association (BambuSC). Even before the research project began, the company from Santa Catarina had already been making bamboo furniture. However, they wanted to become familiar with the physical and mechanical behavior of the giant bamboo (Dendrocalamus giganteus) and the mossô bamboo (Phyllostachys pubescens) it uses to make tables and chairs. “We describe the bamboo from the point of view of its mechanical behavior, that is, we verify the resistance of the glued sheets to the different forces that the finished piece can be submitted to,” says Szücs.

Demoiselle table, made by Oré Brasil: lightweight, resistant structureStudio 25
The company uses thin sheets which go through a transformation process until they are ready to be used. After being sliced and flattened in the longitudinal sense, they are treated with pyroligneous acid – obtained from the smoke that comes from the burning of wood used to make charcoal – they are then dried in a special high-performance greenhouse. “The sheets are glued to each other to make the furniture,” says Szücs. This process creates slim, light pieces that are considerably different from the rustic furniture made from cut and tied bamboo sticks. Last November, three design objects designed by architect Paulo Foggiato, who is also a director of the company, were awarded the first prize under the furniture category at the 23rd Museu da Casa Brasileira Design Award event held in São Paulo. The awarded objects include the Demoiselle table, whose design was inspired by the structures of the first airplanes created by Santos-Dumont, one of the pioneers of the structural use of bamboo.
Technical standards
After the tests conducted at the UFSC, the furniture is tested at a lab of the National Service for Industrial Training (Senai); the test is conducted according to international standards, as Brazil does not yet have a technical standard for bamboo furniture. This issue was addressed at the 2nd Seminar of the National Network for Bamboo Research, held in August in the city of Rio Branco, State of Acre. The event brought together researchers involved in 12 projects being conducted at different institutions and universities; the projects are being funded by the CNPq funding agency. The program is coordinated by professor Jaime Almeida, from the Center for the Research and Application of Bamboo and Natural Fibers of the University of Brasília. “We want to establish a specific technical standard for bamboo, similar to the technical standard used for wood,” says Szücs, who has been working with reforested wood for the last 27 years.
At the event, Beraldo presented the results of his project, which focused on the use of bamboo residues in materials for civil construction. Bamboo processing generates small bamboo chips that can substitute gravel or sand in the production of mortars and alternative concrete. This renewable addition can be used to make lightweight concrete, which is a thermal insulator, and is appropriate for floorings, hollow blocks and corrugated roof tiles. “Like any plant, bamboo residues contain substances such as tannin and sugar, which interfere in the hydration reactions of cement,” says Beraldo, whose early interest in bamboo was aroused in the mid-1980’s, when he discovered the various possibilities related to the application of bamboo. To neutralize these substances which provide plants with color and scent, the bamboo is boiled in hot water or in a diluted lime solution. The next step is to dry the residues and they are ready to be used. The same material can be mixed in plaster, after the particles are treated.
“Bamboo has great potential to generate energy, as its combustion heat is similar to that of eucalyptus,” says Beraldo. Four years after it is planted, bamboo can be used to make charcoal, in comparison to the ten years it takes eucalyptus to get to this stage and the thirty years it takes native trees. “All the applications of this giant gramineae, however, are constrained by the small scale production, in view of the modest use in Brazil, a situation which has existed for centuries,” says Beraldo. “Support needs to be provided for the production of seedlings in a scientific way.” The production of seedlings in a systematized manner is one of the major obstacles to the large scale planting of bamboo.
Researchers from the Cellular and Molecular Biology Lab at the Center for Nuclear Energy in Agriculture (Cena), located on the USP campus in the city of Piracicaba, have made efforts to overcome this obstacle. “Although bamboo seedlings grow in the fields, it is quite complicated to multiply the seedlings of the species of interest, such as the giant bamboo,” says researcher Siu Mui Tsai, coordinator of one of the projects funded by the CNPq. After getting good results with the first and second generations of seedlings, the yields start to drop and the fifth generation of seedlings dies. “This happens because there is an enormous natural interaction of the plant with beneficial micro organisms called endophytic organisms, which are eliminated when the bamboo is cultivated in vitro,” she says. Researchers want to understand how this relationship works in order to move towards large scale production.
The projects
1. Projeto Bambu: manejo do bambu-gigante (Dendrocalamus giganteus) cultivado na Unesp/campus de Bauru e determinação das características físicas e de resistência mecânica do bambu laminado colado (nº 2003/04323-7); Modality Regular Research Awards; Coordinator Marco Antonio dos Reis Pereira – Unesp; Investment R$ 45.989,40 (FAPESP)
2. Tratamento químico de colmos de bambu pelo método Boucherie modificado (nº 2001/12700-0); Modality Regular Research Awards; Coordinator Antonio Ludovico Beraldo – Unicamp; Investment
R$ 12.065,00 (FAPESP)