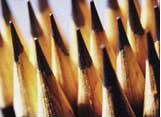
eduardo cesarPencil with the new graphite: resistant, without losing softness and the intensity of the writing on the papereduardo cesar
The German multinational Faber-Castell, with the use of advanced technologies for characterization and technology developed in partnership with the Interdisciplinary Electrochemical and Ceramics Laboratory (Liec) of the Federal University of São Carlos (UFSCar), has obtained a more resistant lead, without altering its deposition, which is the intensity of the mark of the lead on the paper, and of the smoothness of the product. The improvements implemented as a result of two years of research have made it possible for then pencils and leads for propelling pencils, to reach the level of international quality, without altering the price for the consumer, reports Vladimir Barroso, the company’s manager for Research&Development (R&D).
The company is the national leader in the production of lead pencils, with about 2.5 million grosses (units of measure equivalent to 12 dozens) a year, besides being the group’s only manufacturer in the whole world of lead for propelling pencils. According to Barroso, the improvement in the resistance and the maintenance of other qualities of the products are going to guarantee their leadership in the domestic market, and will help Faber-Castell to expand its share in new markets. “Developing a product that meets the requirements of the international market was fundamental for preserving this share”, says Professor Edson Leite, the coordinator of research at Liec, a laboratory that is a part of the Multidisciplinary Ceramic Materials Development Center (CMDMC), one of the ten Research, Innovation and Diffusion Centers (Cepid) financed by FAPESP.
Patent for the catalyst
The main challenge for the team of researchers consisted of filling in the pores and the fissures left in the graphite leads during the stage of firing or sintering, when the organic compounds present there are decomposed and transformed into gas. To do so, they used an organometallic nanocompound, or organic molecules bound to metals, which had been developed and patented by Liec to be used as a catalyst (accelerator of chemical reactions), particularly in the conversion of methanol and ethanol into hydrogen. “Our task was to adapt this nanocompound to the graphite and to the company’s production process”, says Leite.
Besides being compatible with the thermal expansion coefficient (the increase in the volume of materials during heating) and with the crystallographic structure (the internal structural arrangement), the use of the nanocompound made possible a good performance by the end product and a cost that was acceptable for the market. “Before the partnership with Liec, we thought of using a compound obtained by Japanese researchers that was costing US$ 2,000 the kilo and, having little stability, needed special care in transportation, storage and handling. The development of the new compound at Liec led to a product with a cost 600 times lower than the Japanese material, without showing any difficulty in stocking and handling, besides having the advantage of not containing toxic solvents in its composition”, Barroso says.
The additional expense arising from the introduction of one more component in the formulation of the graphite was offset, according to the company’s R&D manager, by the increase in the product’s resistance. This alteration brought about a reduction in losses during the industrial processing of the pencils and of the leads. “With more resistant graphite, we achieved a 2% reduction in the level of rejects and a consequent increase in productivity”, Barroso commemorates. It was, however, still necessary to carry out improvements in the raw materials (graphite, clay and resins) and in several stages of the production process (mixing, extrusion, pyrolysis and sintering) to allow its adaptation to the graphite.
The details of this process and the composition of the organometallic and its modifications are treated as an industrial secret by the researchers. They merely reveal that improvements were established in the purity of the raw materials and in the homogenization of the materials. “We developed test methodologies for assessing the impact of each stage of the process and of the raw materials on the finished product”, says Leite.
For the company, the technologies developed in partnership with Liec cost about R$ 1 million, forked out in two years. Of this total, R$ 160,000 was passed on to the laboratory for the maintenance of equipment and payment of technicians. Another result of this partnership came in the form of praises from the German researchers at Faber’s headquarters. “They were very surprised at the technologies introduced into the process”, Barroso says. He points out that the Brazilian R&D department is the only one maintained by the multinational outside its headquarters. Eight researchers, from the university and the company, worked directly in the process of improving the new graphite. “This partnership with Liec made it possible to contract two doctors, who before that used to belong to the team of the laboratory, and the qualification of all the members of the company’s staff who were in any way involved in the project”, Barroso says.
The Project
Nanocompound for graphite; Modality Research, Innovation and Diffusion Centers (Cepid); Coordinator Elson Longo – Multidisciplinary Ceramic Materials Development Center; Investment R$ 1,200,000.00 annually for the whole Cepid (FAPESP) and R$ 1,000,000.00 specifically for the project (Faber-Castell)