Ceará, one of the driest and most water-stressed states in Brazil, is preparing to build what will become the largest desalination plant in the country. Once completed, the project, which began with basic design in 2016, will provide increased water security to the state capital, Fortaleza, and surrounding municipalities in a metropolitan area with a population of 4 million people. The project owner, CAGECE, the state water utility, expects to issue the call for bids for construction within the first half of the year. The technical, operational, environmental, and economic studies that are being used to inform the call for bids were prepared by a consortium led by South Korean GS Group.
Construction of the facility, which should start operation in 2022, will be through a public-private partnership (PPP) arrangement, the particulars of which will be outlined in the call for bids, explains CAGECE’s sustainability director, Ronner Gondim. Mucuripe beach, near the port of Fortaleza, is being considered to host the project. The plant will be designed to produce 1 cubic meter (m3) (or 1,000 liters) of water per second—the Metropolitan Area of Fortaleza consumes 8 m3 per second. “Water supply capacity will increase by 12%, enough for 720,000 people,” says Gondim. The cost of the project is estimated to be approximately R$480 million.
“The successful bidder will be responsible for construction and will acquire the right to operate the plant for 30 years,” he explains. The Government of Ceará will stipulate a maximum rate per liter of desalinated water and will award the contract to the bidder offering the lowest rate. CAGECE currently charges an average of R$3 per cubic meter of treated water. The global average cost of desalinated water starts at US$2 (approximately R$8) per cubic meter, depending on the process.
The new plant will likely use the reverse osmosis process for desalination, although this decision will be left to the successful bidder. Reverse osmosis is currently the cheapest known method of desalination. In this process, a high-pressure pump forces water across polymer membranes with minute pores, which retain the salts. The energy expenditure of this process is as high as 4 kilowatt-hours (kWh) per m3 of purified water. The technology is used in 84% of desalination operations globally. Israel, a pioneer in desalination by reverse osmosis, processes 600 million m3 of sea water into drinking water each year, providing water supply to 6.5 million people, or about 75% of the Israeli population.
There are currently 15,900 desalination plants in operation worldwide, with a capacity to purify about 95 million m3 of water per day, according to a study published in December 2018 in Science of the Total Environment. The majority of plants are in the Middle East, North Africa, the US, China, and Australia. In Europe, Spain has the largest desalination capacity. The plant in Barcelona, on the Mediterranean coast, with a capacity to process 2.3 m3 of water per second, is one of the largest on the continent.
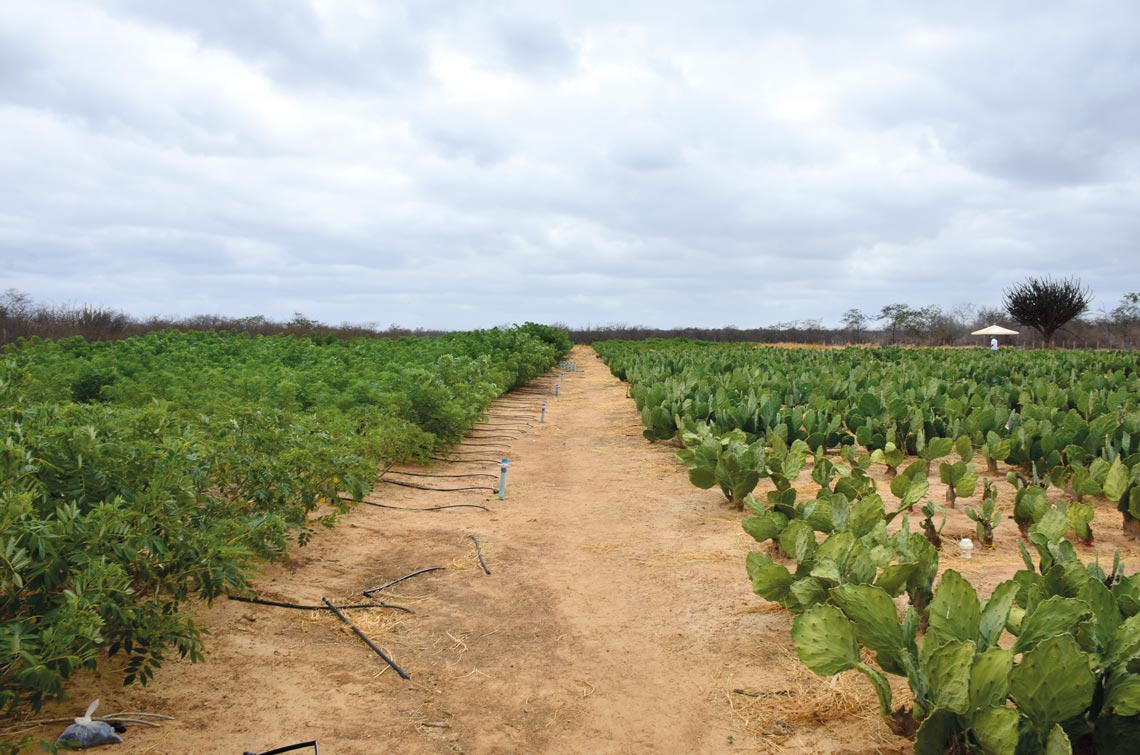
An irrigation system in northeastern Brazil using effluent from the desalination processMarcelino Lourenço Ribeiro Neto / Embrapa Semiárido
Cost is the primary constraint
Saudi Arabia and the United Arab Emirates have the largest desalinization capacity globally. The world’s biggest plant, in Ras Al-Khair, Saudi Arabia, produces 1 million m3 of water per day (11.5 m3 per second). The most commonly used method there is thermal desalination, in which saltwater is stored in heated tanks. When it evaporates, steam builds up in the upper part of the tank and then condenses into pure water without salts.
One of the drawbacks of thermal desalination is its high energy requirement, to the tune of 15 kWh/m3. Most of the thermal energy used in the process comes from fossil fuels, such as oil and gas, which are abundant in the region. Thermal desalination costs about three times as much as reverse osmosis, at about US$6 per m3 of treated water.
With high energy consumption remaining the biggest barrier to large-scale adoption of desalination, especially in developing nations, researchers in several countries are working to develop new, more efficient, and more cost-effective technologies for desalination. One of the new technologies that is currently being explored is capacitive deionization, an electrochemical process that retains the ions contained in the water as they pass between two electrically charged porous carbon electrodes. “Capacitive deionization is still a young technology, but has shown promise. For brackish water, it is even more cost-effective than reverse osmosis,” says chemical engineer Luís Augusto Martins Ruotolo of the Department of Chemical Engineering at the Federal University of São Carlos (UFSCar). Globally, the leading institutions advancing this method are Stanford University, the Lawrence Livermore National Laboratory, the Massachusetts Institute of Technology (MIT), and the European Center of Excellence for Sustainable Water Technology (WETSUS), in the Netherlands.
The biggest advantage of this system is that high pressures are not required to operate the equipment, unlike in reverse osmosis, says Ruotolo. “This reduces energy requirements and operating costs,” he explains. In Brazil, Ruotolo’s group developed a capacitive deionization process using activated carbon with nanometric pores.
Another emerging strategy that has gained interest is the use of graphene oxide membranes—atom-thick sheets of carbon—in reverse osmosis systems to filter salt out of seawater or brackish water, such as the water found in wells drilled in Brazil’s semiarid region. This technology is estimated to reduce energy consumption by up to 50%—pumping saltwater across graphene membranes creates less friction compared to traditional polymer membranes.
Scientists around the world are engaged in further researching this technology. In Brazil, researchers from the State University of Paraíba (UEPB), the Federal University of Rio Grande do Norte (UFRN), and the Federal University of Paraíba (UFPB) are developing nanostructured graphene membranes for use in desalinating brackish water. In addition to cost reduction, another benefit of this method is that graphene filters need cleaning less often than reverse osmosis membrane filters do. Graphene is also immune to the effects of chlorine, a chemical used in the cleaning process that reduces the structural integrity of polymer membranes, requiring them to be replaced more frequently.