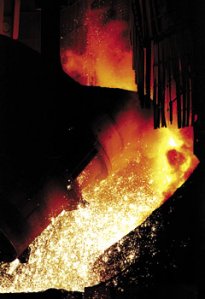
ALAOR FILHO/AEResidues with metallic content ready to be re-usedALAOR FILHO/AE
A new process adopted since February of this year on the industrial scale by the steelmaking company Companhia Siderúrgica Nacional (CSN), in the town of Volta Redonda, state of Rio de Janeiro, allows for the re-use of the iron contained in the sludge generated in high temperature furnace and steelworks during the processes of reduction and steel refining, resulting in economic and environmental gains for the company. Currently around 80,000 tons of sludge, of the 120,000 tons produced per year at the steelmaking plant are recovered. For this to occur, the material, which has in its composition 30% of iron oxide and 70% of carbon and clay, passes through a process for the separation of the metallic content. “The residues that carry the iron oxide are made into small pellets, thermally treated and re-introduced into the production process, transforming it into pig iron and afterwards into steel”, says professor Elson Longo, the director of the Multidisciplinary Center for Ceramic Materials Development, one of FAPESP’s Research, Innovation and Diffusion Centers, which have been joined by the São Paulo State University (Unesp) at the town of Araraquara and the Federal University of São Carlos (UFSCar), in a partnership with CSN in search of innovations and improvements in the production processes since 1989. The clay that is left over from the metal separation process is transformed into slag and has various applications.
“The process represents the recovery of almost 70% of the residues generated from the high temperature furnaces, reducing the environmental impact and generating a significant economy for the steelmaker”, advised Walter Luiz da Costa Reis, the general manager of CSN’s steel making processes, supervised during his doctorate thesis by professor Longo. Before, all of this material was discarded and sent to an environmentally controlled land fill. The researchers are now working on the development of a project for the recycling of the remaining 30% of the sludge, which corresponds to 40,000 tons and contains a large quantity of zinc, an expensive metal, but harmful to the steel reduction and refining processes. “We want to carry out an even better recovery of this remaining material in order to obtain the maximum possible return”, says Longo.
The research that resulted in the reuse of the sludge began some three years ago and was able to count upon the assistance of the researchers José Arana Varela, pro-rector of research at Unesp, Edson Leite, from UFSCar, and André Tarcizo de Oliveira Vieira, CSN’s coordinator of residue management. From the university laboratories the process was initially implanted on a pilot scale at the steel works. Today some 5,000 tons per month of sludge produced by the high temperature furnaces making pig iron, and 1,500 tons of residues produced making steel are recycled and re-used. “The management of this sludge constitutes one of the greatest challenges to the steel industry world wide”, says Longo.
Ceramic fiber
As well as the process of recycling and recovery of the metals contained in the sludge, which was patented, another recent fruit of the collaboration between CSN and the Ceramic Materials Center is the development of ceramic fibers from the slag resulting from the production of steel, with a high potential for substituting asbestos in the manufacture of roofing tiles. The new product could also be used in ceilings, panels, asphalt and even in the tires and dyes industries. The major advantage of the fiber obtained from slag is its low production cost. “As this raw material comes out of the blast furnaces in a liquid state, it’s not necessary to melt it for it to be transformed into a new product, which results in an economy of energy”, says Longo.
CSN has set up a partnership with the company Unifrax, a multinational of North American origin and a specialist in ceramic fibers, to initially produce the fibers at the company’s plant at Vinhedo, in the interior of the state of São Paulo, which has the capacity of an annual production of some 3,000 tons. The plans are to set up a new company, with majority participation from the steelmaker, to produce between 40,000 and 50,000 tons of fiber annually. The forecast is that the new factories begin their production at the beginning of 2008 and that the sales of ceramic fiber come in at around US$ 50 million to US$ 70 million per year. The investments required to attain the estimated productivity capacity are in the order of US$ 15 million. Since the start of the research for obtaining fibers, which began in 2003, the steelmaker has invested US$ 4 million. “The slag has low added value, since it was exclusively destined to the small stones industry, which used it, mixed with cement, in the building of highways”, explains Longo. With the transformation of the material, its added value has reached another level.
In the form of ceramic fibers, the slag presents the same physical properties as asbestos, but without any risk to the human organism, and for this reason it is quoted as substituting it in various applications. In Europe and Japan, asbestos can no longer be used because of the illnesses caused to workers who manipulated the product. In Brazil the variety known as chrysotile or white asbestos has controlled usage, allowed for by Brazilian legislation since 1995. The production of roofing tiles is the large asbestos market, which will be disputed by the ceramic fibers coming from slag. Another sector that is also promising is that of the manufacture of sheets for facades, currently imported.
The Projects
1. Recovery of sludge
2. Ceramic fibers starting from slag
Modality
Research, Innovation and Diffusion Centers (Cepid)
Coordinator
Elson Longo – Multidisciplinary Center for Ceramic Development (CMDMC)
Investment
Annual R$ 1,200,000.00 (FAPESP)