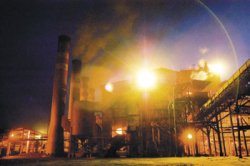
EDUARDO CESARBoilers at the Santa Elisa Mill: production of electricity with sugarcane bagasseEDUARDO CESAR
The old mills producing sugar and alcohol in the interior of São Paulo, with their extremely high brick chimneys, have given their place to modern companies tuned in to the new technologies that are resulting in greater productivity in the field and gains in the industrial process. Sertãozinho, a city with less than 100 thousand inhabitants located in the northeast of the state of São Paulo, 320 kilometers from the capital, translates well the transformations that have occurred over the last few decades in the sugar and alcohol sector. The city has seven mills producing sugar and alcohol and 500 companies scattered over four industrial districts, 90% of which focused on the sugar and alcohol sector, but also acting in the areas of pulp and paper, foodstuffs and others. The city is a leader in the generation of employment in the São Paulo industrial sector, according to figures from the Industry Center of São Paulo State (CIESP). In this year alone, up until the month of August, the positive variation was 20.4%, with the hiring of 6,300 workers.
The industrial vocation of the city, a neighbor to Ribeirão Preto, started in the 1970s, with the oil crisis and the government incentive for Proálcool. In the golden age of the program, Zanini, a company that makes industrial equipment, went so far as to have 7 thousand employees working 24 hours a day. With the end of the government program and consequent mergers of companies and dismissals of employees, many engineers and workers began to provide the sugar and alcohol sector and other sectors with maintenance services. Today, many of these embryonic businesses have transformed themselves into companies exporting high technology. And this is an upward trend in the municipality. “We exported US$ 74 million in 2003, US$ 120 million in 2004, and US$ 135 million in 2005”, says Marcelo Pelegrini, Sertãozinho’s Secretary for Industry and Commerce, based on the figures from the Brazilian Institute of Geography and Statistics (IBGE). To reach this level, the companies differentiated themselves by betting on innovations in products and productive processes. And the examples are not a few.
A process for dehydrating ethanol known as extractive distillation, which currently accounts for about 35% of all the anhydrous alcohol produced in Brazil, only arrived on the market because two businessmen from Sertãozinho, designer Valter Felipe Sicchieri and chemical engineer Paulo Barci, glimpsed that they were looking at an innovative methodology when thumbing through a magazine during a visit to a customer. What attracted their attention was a article on extractive distillation with ethylene-glycol, an organic product from the family of alcohols, that showed the possibility of producing anhydrous alcohol (used as an additive in gasoline) with the same quality and a lower consumption of electricity, by Professor Antonio José Almeida Meirelles, from the School of Food Engineering (FEA) of the State University of Campinas (Unicamp).
The paper, published in 1991, an abstract of Meirelles’s doctoral thesis, had received the 1989 Young Scientist award from the National Council for Scientific and Technological Development (CNPq). Interested in new technologies, the businessmen contacted the researcher at Unicamp. “In that conversation, we entered into a verbal commitment”, says Sicchieri. On return to Sertãozinho, the businessman called on Santa Elisa Mill to negotiate the use of a pilot plant that had been taken out of service at the time. Having made some adaptations to the plant, the technology began to be tested in the 1998 crop, with the distilling of 50 thousand liters of anhydrous alcohol a day. Between harvests, the results were evaluated. “In this stage, we began to use our knowledge of engineering and processes to make some modifications in the basic technology”, Sicchieri says.
Pilot plant
In the following year’s crop, with small changes incorporated into the process, the final tests were carried out at the pilot plant. Some customers were invited to get to know the new process in operation at the mill. Seven industrial plants (sets of equipment) were sold, amongst new ones and ones adapted to the production processes at the mills. The great advantage of the ethylene-glycol process in comparison with the hexane cycle process, using a saturated hydrocarbonate, a volatile and highly inflammable product that is used nowadays, is that is with the same total consumption of steam (the source of energy used) twice the amount of anhydrous alcohol can be produced. Furthermore, the process consumes less water than the traditional processes.
The two partners have two companies: B&S, in charge of designing the equipment, and JW, responsible for its construction. Today, there are 34 mills in Brazil that have adopted the extractive distillation process for alcohol, and one in El Salvador, in Central America, which belongs to the Cargill group, with a capacity for dehydrating 700 thousand liters of anhydrous alcohol. Unlike the Brazilian ones, the industrial plant in El Salvador was assembled merely to dehydrate imported alcohol, which, once ready, is sent to the United States. By the beginning of September, another four units, forecast to come into operation by 2008, had been sold to Brazilian mills. The evolution of the extractive distillation process is, without a doubt, a success story. For this to have happened, the interest of one engineering and equipment company was decisive. “They managed to transform academic knowledge into a real and functional piece of equipment, in accordance with the requirements that the mill establishes, while maintaining the quality of the alcohol”, Meirelles says.
Industrial automation
It was this same spirit of blazing innovative trails that led a group of engineers, in 1978, to transform Smar Equipamentos Industriais, of Sertãozinho, a company created in 1974, into the largest manufacturer of instruments for controlling industrial processes electronically in Brazil. Before, it used to provide maintenance services for steam turbines in the sugar industry. Nowadays, it above all develops and produces sensors and transmitters for automation processes. It is equipment that is packed with technology, essential for almost all the industrial processes. To start with, there were ten partners and three employees. Today, there are almost a thousand employees, of which 150, who came from the main Brazilian universities, make up the company’s research and development team.
Last year, the company grossed US$ 80 million, and sales to the export market, made up of over 60 countries, accounted for 50% of this amount. The investment in research and development (R&D) works out to around 10% to 12% of sales and shows heartening figures. In the United States, the company has 20 patents granted and over 30 being processed. “Smar is the Brazilian private-sector company with most patents in the United States”, says César Cassiolato, an electronic engineer and the company’s marketing director.
Smar’s first development was the automation of a sugarcane conveyor belt for the crusher of a mill in the municipality of Pontal, in the interior of São Paulo. The system, which controlled the quantity of sugarcane that should be used to feed the shredders and the crushers, resulted in a 20% increase in production and opened the way for other innovations. In the 1980s, Smar developed the pressure transmitter with a capacitor cell, a piece of equipment designed to measure and control the pressure, level and flow of the boilers of the sugar and alcohol mills.
Flagship of the company to this date, the transmitter has won other markets. “This same sensor is used by the oil and gas industries, and even in the aircraft carriers of the American Navy”, says Cassiolato. A new model of the product with high performance and precision was launched at the end of September at the 2006 Fenasucro & Agrocana (see article on page 63), an international business and technology fair that has been held for 14 years in Sertãozinho. Another product from Smar presented at the fair that has gained improvements is an industrial process maintenance and diagnostic system called asset management. From anywhere in the world, at any time, it is possible to check out how the situation of the production is.
The company that at the end of the 1970s had only three employees boasts today ten subsidiaries and over 80 representatives spread over various countries to attend to the world market. To reach this level of excellence, the differential was the partners’ bet on having a company driven by technology, even when this idea was distant from the reality and the Brazilian industrial vocation. The term ‘technological innovation’ has been incorporated into the vocabulary of the local industry. Even when the company does not have a research and development team of its own, it resorts to exclusive partnerships for the development of the projects. This is the case of Sermatec, a manufacturer of equipment for sugar and alcohol mills. The company’s flagships are diffusers, used in the extraction of the sugarcane juice, and boilers, two types of equipment developed, respectively, with Uni-Systems and HPB Engenharia, both companies from Sertãozinho.
The diffusers are an alternative to the use of the crusher, which reigned absolute until the mid-1980s. From then until now, various innovations have guaranteed greater efficiency for the diffusion process, making it become an excellent option for the production of alcohol. “In the crusher, the extraction of the juice reaches 96.5% at the most, with the diffuser we get 98.5%, which at the end of a harvest means a few million dollars of sucrose”, says Daniel Moraes Filho, Sermatec’s commercial manager. “Another advantage of the diffuser lies in the lower consumption of steam, which makes it possible to increase the cogenerated power (to produce electricity and for sale to the concessionaires).” The main difference between the two processes lies in the manner of extracting the sucrose. The crusher crushes the sugarcane, while the diffuser takes the juice out with hot water.
Energy from the bagasse
The high pressure boilers manufactured by Sermatec and designed by HPB Engenharia have amongst their main markets the sugar and alcohol, pulp and paper and mining and other industries. Essential for the operation of sugar and alcohol mills, the boilers driven by the heat originating from burning the bagasse generate the steam that produces the energy necessary for the industrial plant to work. The excess, called cogeneration, can be sold to the concessionaires of the electricity grid at the auctions held by the Brazilian Electricity Regulatory Agency (Aneel). For this reason, innovations are always welcome for improving the energy efficiency of the mills and offer more alternatives for the Brazilian energy matrix. “The high pressure boiler favors cogeneration”, Moraes Filho says.
Sermatec, which has 700 employees, estimates for this year sales in the order of R$ 400 to R$ 500 million. “The company is enjoying a very good moment for the sector, with great demand”, the commercial manager says. Various projects under way have foreign investors as partners. New units for producing sugar and alcohol are being constructed in Mato Grosso do Sul, in the south of Goiás, in the north of the state of São Paulo, and in the Minas Triangle. The figures for the sales of diffusers illustrate well the sector’s trend for expansion. In 20 years, Sermatec marketed four diffusers. And this year alone, nine have already been sold, with the prospect of another five being sold by the end of the year.
The growth of the sector, with some 90 projects for expanding and enlarging mills in Brazil, has stimulated the diversification of the business of Sertãozinho’s companies. Caldema, a manufacturer of high pressure boilers for electricity cogeneration, is going to invest, in a partnership with the Balbo Group, also from Sertãozinho and a sugar and alcohol producer, R$ 120 million in a sugar and alcohol mill in Uberaba, Minas Gerais. Founded in the 1970s, the company’s main focus is the sugar and alcohol sector, but it also attends to other sectors, like pulp and paper, mining, chemicals and petrochemicals. The technological development of Caldema’s boilers is done in partnership with Brazilian and international companies. In Brazil, the company’s main partner is Thermocal Engenharia, from Piracicaba. The most recent development is a new conception of a boiler with a single big drum, a large steel cylinder in which the water in the steam boiler circulates.
Boilers with this technology, called MonoDrum, are already operating in Brazil in the pulp and paper and petrochemical industries and in thermal power stations. The company’s new model, baptized as AMD – Aquatubular MonoDrum, was specially developed to meet the sugar and alcohol sector’s need for cogeneration. “The new model arose because the mills, with the greater efficiency of the turbines, began to have greater capacity for producing steam by hour and an increase in pressure, and, as a consequence, there was a need for developing a more powerful boiler”, says Alexandre Martinelli, the company’s marketing director. The quest for more efficient boilers from the energy point of view reflects a change in the sugar and alcohol sector driven by the crisis of the Brazilian energy sector in 2001, better known as the “crisis of the blackout”. Today, the producer thinks not only about producing sugar and alcohol, but electricity using sugarcane bagasse.
One of the first to sell the excess energy to the São Paulo Power and Light Company (CPFL), which serves the interior of São Paulo, was the Santa Elisa Energy Company, the former Santa Elisa Mill, also from Sertãozinho, which has been generating electricity for its own consumption ever since 1940. “We have an installed capacity of 58 megawatts (MW) per hour, of which 30 MW is sold to CPFL”, says Henrique Gomes, the company’s administration director. The total electricity produced is sufficient to supply a city of 500 thousand on a daily basis. One of the largest companies of the sugar and alcohol sector, Santa Elisa bills R$ 650 million a year, accounts for about 50 thousand direct jobs, produces 40 million liters of alcohol a year and 10 million 50-kilo bags of sugar.
Even between crops, the mill does not stop producing energy. “With the high pressure boiler that we are using, we have a surplus of bagasse during the harvest”, says Gomes. The sale of excess energy, coming from a renewable source, to the electricity system, enables the company to sell its carbon credits in the international market, the so-called Clean Development Mechanism (CDM) resulting from the Kyoto Protocol. “Up until 2012, we have already sold 50% of our carbon credits to a Swedish agency”, Gomes says.
Increase in demand – The movement to expand the mills was also reflected in the demand for high pressure, high temperature, turbines designed to cater to the processes for cogenerating energy, manufactured by TGM, a company from Sertãozinho. “Over the whole of last year, we sold 60 turbines. This year, we have already sold 75, but we should reach 80”, says mechanical engineer Waldemar Manfrin Júnior, a director of the company. By virtue of the large volume of orders, the delivery time, which used to be six months, went up to 15 months. The company, which was founded only 15 years ago, has today 800 employees and exports to 26 countries. TGM’s trajectory is similar to that of many other companies that form Sertãozinho’s high technology industrial complex. To start with, the company used to provide maintenance services for turbines, all of them imported.
The change of route occurred when the company began to absorb employees from a Brazilian company that used to manufacture turbines with German technology, which moved from Sertãozinho to Osasco after being incorporated by a multinational. Many qualified employees did not want to change cities. With this, from seven employees, the company went to 50. And the natural way was to pass from a provider of services to a manufacturer of turbines with a technology of its own. The first was developed in 1995. “All the turbines that we sell are developed by our team of engineers, from the small 20 kilowatt one to the biggest, with 70 megawatts”, Manfrin says. There are 42 engineers working on turbine design, because each mill requires a different project.
After the crisis of the blackout, business took off, with the orders from the mills. The hirings too. From 140 employees, the company reached 280. After sales of R$ 200 last year, the company estimates billing of R$ 300 million this year. The three partners also have 50% of TGM Cannes, a company based in Germany. The four German partners, who control the remaining 50%, used to work before in the German company, Siemens. Today, the turbines manufactured in Sertãozinho, the only ones with Brazilian technology, are purchased by TGM Cannes, which is in charge of assembling them.
Trade fairs
Two events connected with the sugar and alcohol sector, held simultaneously in Sertãozinho, between September 19 and 22, brought together about 55 thousand people, 10% more than originally forecast. In an area removed from the center of the city, about 40 thousand square meters were set aside for 550 Brazilian and foreign exhibitors who took part in the XIV International Sugar and Alcohol Industrial Fair (Fenasucro) and the IV Sugarcane Farming Business and Technology Trade Show (Agrocana), at the Zanini Events Center. Equipment, products and services needed for all the planting and harvesting of sugarcane, as well as the production of sugar and alcohol, could be seen and negotiated The expectation is that the volume of business generated by the fair and in the three subsequent months reaches about R$ 1,5 billion.
The International Business Round, which takes place on the 20th and 21st should result in a turnover of R$ 7.5 million. There were two days of negotiations between ten buyers, of which three from abroad – Ecuador, Mexico and Tanzania – and 60 salesmen. The amount to be negotiated as a result of the round is calculated on the basis of the evaluation made buy the buyers at the end of each meeting with the salesman.
Various events took place simultaneously with the holding of the fair, like the International Alcohol and Ethanol Forum, which attracted the presence of several leaders from the sector, besides talks and the seminar “The path to success in the reduction of steam in the sugar factory”.
Republish