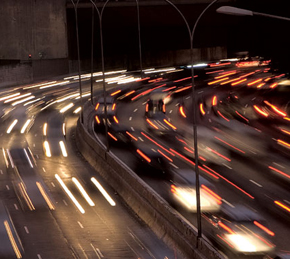
Eduardo CesarProducing electricity under asphalt is made possible by piezoelectric materialsEduardo Cesar
In 1880, brothers Pierre and Jacques Currie, French physicists, discovered the property that some mineral materials have to generate an electric current when deformed by mechanical pressure, a phenomenon that earned the name of piezoelectricity. This discovery gave rise to several commercial applications, from the luminosity on the soles of children’s trainers to applications in ultrasound equipment and lithotripsy, a medical procedure for breaking up kidney or gall bladder stones. However, in times of environmental and energy concerns, usage based on piezoelectricity is gaining ground among researchers: producing electricity, using an inexhaustible source that does not pollute. This is what, for example, two professors from the Paulista State University (UNESP) are doing. Physicist Walter Katsumi Sakamoto, from the Department of Physics and Chemistry at the School of Engineering of Ilha Solteira (Feis), and chemist, Maria Aparecida Zaghete Bertochi, from the Department of Biochemistry and Chemical Technology at the Institute of Chemistry at the Araraquara campus, with financial support from FAPESP, are working on creating a material capable of taking advantage of the mechanical force generated by the traffic on a street, for example, to obtain electricity. This is a film, technically called a composite, which is made from mixing a polymer with nanometric (a measure equivalent to one millionth of a millimeter) ceramic particles, and which can be placed under the asphalt; when it comes under pressure, it becomes deformed and generates an electrical current.
Maria Aparecida is in charge of developing the nanometric ceramics that form part of the film. She makes use of nanotechnology resources on an atomic and molecular scale to make the ceramic powder that goes to make up the film, the ceramic oxide, lead zirconate titanate, better known by its acronym, PZT – the P comes from the Latin name for lead, plumbum. To develop the nanoceramic, Maria Aparecida used a new production method. She explains that the most common way of obtaining PZT is by means of the Pechini process. “In this case, the property that organic acids, such as citric acid, have of forming organic metal-acid type complexes is used,” she says. “This complex, when combined with alcohol, polymerizes forming polyester, a highly viscous polymer, which is decomposed into oxide by combustion, at temperatures around 500 to 800°C. At this temperature, we obtain nanometric ceramics. In the case of PZT we use zirconium, titanium and lead citrates to synthesize the ceramics.”
Pressure and volume
The new process uses the so-called hydrothermal synthesis, whose parameters were optimized in the study by Maria Aparecida, with salts or oxides of zirconium, titanium and lead that are mixed in an aqueous solution, to which is added a mineralizing base (sodium or potassium hydroxide). The mixture is then subjected to heating by microwaves in a closed Teflon container for 30 minutes at 180°C. “The advantage of this process is that by using a low temperature for a short time, ceramic particles are obtained that have an excellent crystalline arrangement, which is important because the piezoelectric property depends on this,” explains the researcher. “Furthermore, it does not release lead by evaporation.” This nanometric ceramic produces energy because it has an asymmetry in its load center, generating a spontaneous polarity within the structure of the material. To be piezoelectric, the material must have a crystalline structure in the form of a slightly deformed cube. “When pressure is applied to the material, like a car driving over it or someone stepping on it, its volume is instantly reduced,” she says. “This increases the load density inside it, causing the release of electrons along wires that are connected to the ceramic material. These electrons can be used to light a lamp, for example.”
Nanometric ceramic on its own is capable of generating energy, but there are some drawbacks. It is fragile, expensive and not very flexible. Overcoming these obstacles is precisely the work of Professor Sakamoto. “We are looking for a more flexible and cheaper material,” he says. “Right now we’re developing a polymer-ceramic compound, which is a material composed of polymers and PZT.” To do so, Sakamoto mixes the ceramic powder with the polymer, also in powder form. This mixture is pressed at the melting temperature of the polymer used to obtain the film. The two researchers have tested compounds with 30%, 40% and 50% ceramic material and the rest polymers. The most commonly used in the research are polyvinylidene fluoride (PVDF), which melts at around 180°C, and polyether ether ketone (PEEK), whose melting temperature is around 360°C. “So, by using a polymer matrix, in which the ceramic material is mixed, there is a gain in resistance to mechanical shock, flexibility and formability (the compound can be molded into any shape),” says Sakamoto. “There’s also an economic advantage. In opting for this compound, less ceramic material is used and it becomes possible to study different matrices in order to improve the piezoelectric activity of the film.”
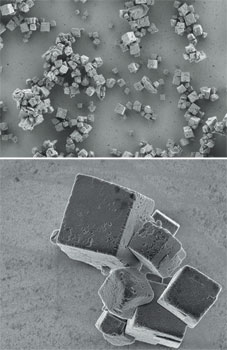
Eduardo CesarProducing electricity under asphalt is made possible by piezoelectric materialsEduardo Cesar
The first film developed by Sakamoto and Maria Aparecida was small, measuring 2 cm. by 1 cm., and its capacity for generating energy was proved in the laboratory. Sakamoto placed the new compound, connected to an LED (light emitting diode) between two acrylic plates. When they were pressed the LED lit up. However, depending on the size of the film, the energy generated can be much higher. “It’s known from scientific literature that a person weighing 60 kilograms produces an average of 0.1 watt with every step they take,” says Sakamoto. Other data come from Israel, which has invested heavily in this line of research. There, experiments were carried out showing that one kilometer of a heavily used highway containing piezoelectric material can generate 200 kilowatts (kW), enough electricity to power a house for a month. Maria Aparecida and Sakamoto are now testing films that are slightly larger, 7 cm. x 7 cm., to find out what voltage can be obtained. “We want to know if it’s possible, using this material, to charge an AAA battery, known as stick batteries and used in devices like remote controls, and if we need to put some films in series or in parallel to get more voltage or more current,” says Sakamoto. “Depending on the result, its use commercially is a mere consequence.”
In some countries the use of this technology is already more advanced. In 2008, two nightclubs, the Surya in London and the Watt in Rotterdam, in the Netherlands, installed piezoelectric dance floors. When customers dance they generate enough power to light the dance floors. In Japan, the company Soundpower, installed piezoelectric systems in the floor of two train stations in Tokyo, which are used by some 2.4 million people each week.
In Israel, between 2008 and 2009, a pilot project was developed on highways and airports. In Brazil, Maria Aparecida and Sakamoto imagine various applications for the piezoelectric film they are developing. “This technology will be able to generate power in busy areas, and not just from passing cars but also from people walking,” says Sakamoto. “Shopping malls, for example, could use special floors that transform customers’ footsteps into energy for lighting the corridors. Or the film could be applied to the soles of shoes, which would make them capable of generating electricity, while their wearers are walking, to supplying small electronic devices, like cell phones or music players.” The compound would also serve to generate power within a car. “We could install piezoelectric materials in moving parts, such as shock absorbers and tires,” says Sakamoto. “This alternative source would substitute the car’s engine for powering up its electrical system.”
Power generation is only one of the applications of these piezoelectric materials. In the medical area, they could be used, for example, as sensors for detecting X-ray leaks in clinics and hospitals, or for the production of implants capable of stimulating guided bone growth, which would be very useful in orthopedic treatment and dental implants. “Piezoelectric technology can be used for the structural inspection of materials, such as those used in aircraft fuselages,” adds Sakamoto. “In tests we found that the compound is efficient in detecting micro-cracks in the carbon fiber plates that are used in aircraft.”
Challenge of storage
Despite the optimism, the researchers caution that to use this technology on a large scale it is still necessary to overcome one obstacle: energy storage. Using it as it is generated is no problem. The problem comes with storing such energy for future use. Currently, storage is only possible with large capacitors (equipment for storing energy), which are still expensive and occupy too much space. For Sakamoto, the solution may be found once more in nanotechnology. “The ideal thing would be to develop another nanomaterial, whose main property is to accumulate large quantities of energy in a small size,” he says.
Sakamoto and Maria Aparecida, who form part of the National Institute of Science and Technology of Materials in Nanotechnology (INCTMN), based in Araraquara and funded by FAPESP and the National Council for Scientific and Technological Development (CNPq), are satisfied with the results they have obtained so far. “We’ve submitted two articles to scientific journals and a book chapter that should be published in the United States next month, by Novapublishers,” reveals Sakamoto. Maria Aparecida emphasizes another positive aspect of their work. “We’re using Brazilian material, adapting a system which takes advantage of energy that is completely wasted, and at a very little cost to the environment,” she says.
The project
Intelligent piezoelectric and pyroelectric sensors (nº 01/13187-4); Type
Regular Research Awards; Coordinator Walter Katsumi Sakamoto – Unesp; Investment R$ 52,862.13 (FAPESP)
Scientific article
MALMONGE, J.A. et al. Piezo and dielectric properties of PHB-PZT composite. Polymer Composites. v. 30, n. 9, p. 1.333-37. 2008.