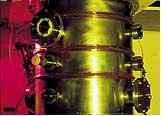
eduardo cesarVacuum chamber where metal prostheses and parts are treated by immersion in plasmaeduardo cesar
If everything runs smoothly, within three years, Baumer, a company from the São Paulo city of Mogi-Mirim and the largest manufacturer of orthopedic implants in Latin America, will be putting on to the market knee and femur prosthesis that are much more resistant and durable than the ones currently produced. This advance will be possible because of the use of an innovative method for treating metallic surfaces, baptized as ionic implantation by immersion in plasma (a sort of gas that is regarded as one of the states of matter, with a molecular and atomic structure and with different particles from the traditional solids, liquids and gases). This treatment has increased the hardness of the steel alloys that make up the prostheses by up to 250% and has reduced wear by around 160 times.
“The method has revealed itself to be biocompatible, and the results went beyond our expectations. Laboratory tests have shown a considerable increase in the endurance of the prostheses, which is usually from 12 to 15 years”, says chemist Roberto Parpaioli, the manager of Bauer’s Research and Development Division. “Our intention is now to organize one or two clinical groups to carry out examinations in vivo on the prostheses submitted to ionic implantation by plasma. We believe that within one or two years we will have concluded the clinical trials.”
For these examinations, the company is going to choose two teams of orthopedists linked to a university. Each clinical group will have, on average, five professionals and from ten to 30 patients. Baumer will provide all the prostheses and bear the costs of the tests. Improving the hardness and, as a consequence, the useful life of orthopedic implants is one of the many applications of this technique of surface treatment, developed in a pioneering venture, in Brazil, by Metrolab, a company from São José dos Campos specialized in calibrating, adjusting and maintaining mechanical and electronic industrial equipment.
The technique was developed in collaboration with the Associated Plasma Laboratory (LAP) of the National Institute for Space Research (Inpe). The method of ionic implantation by immersion in plasma (IIIP or 3IP) can be employed for improving tribological (characteristics that involve hardness, resistance to corrosion and to wear and reduction of attrition and friction), optical and electronic properties of a varied range of materials, such as aluminum, titanium, stainless steel, metal alloys, polymers, plastics, Teflon, nylon and, in the case of semiconductors, making possible the creation of smaller and smaller devices. Accordingly, besides the orthopedic prostheses, there may also be benefits for tools and industrial tools from the automobile, medical, dentistry and aerospace areas, such as cutting knives, molds for aluminum, engine pistons, ball bearings, steel bits, dental implants, and poly polymer bottles, better known as PET, polyethylene terephthalate), used for packaging soft drinks and mineral water.
Discovered at the end of the 1980’s by researchers from the University of Wisconsin, in the United States, the 3IP technique is still little exploited commercially in the world. The main research groups are located in the United States, in Germany, in Australia, in Japan, in China and in Korea. “In Brazil, we have been working with this technology in the area of materials treatment since 1995”, says physicist Mário Ueda, a researcher from the LAP at The National Institute for Space Research (Inpe), who coordinated the end of the project at Metrolab.
At the start, the coordination was also handled by a researcher from Inpe, Raul Murete de Castro. “We use several kinds of plasma at the institute, like, for example, for application in ionic propulsion for controlling satellites in space and in the treatment of polymers in aerospace systems”, Ueda says. “From the start, we knew already knew that the use of 3IP would have an ample commercial application, because this technique has proved to be highly efficient for extending the average life of many tools and components used in industry.”
The passing on of technology and the carrying out of supplementary researches on the part of Metrolab were only possible with the funding from FAPESP received by the company, under the Small Business Innovation Research Program (PIPE). The funds, in the order of over R$ 400,000, were used to acquire the equipment necessary for the construction of a 3IP processing station. The heart of the system is a stainless steel vacuum chamber, in which the plasma is generated and the treatment is implemented in the part. Together with this chamber, which has a volume of about 100 liters, a vacuum system has been installed and a source of direct current voltage, responsible for generating the plasma. Completing the system, there is gas injection equipment, a high voltage pulsator, and a power supply for controlling the parameters of the plasma.
The first step in the treatment process is placing the part in the vacuum chamber and creating the plasma, an ionized gas produced at high temperatures. It is different from the solid, liquid and gaseous states, because the ionization (loss or gain of electrons) of its particles, molecules and atoms is significant. Nitrogen gas has mainly been used for producing the plasma – depending on the application, gases like helium, argon and hydrogen may also be used.
The purpose of the treatment is to implant in the part positive hydrogen ions present in the plasma – it is these ions that give the material better characteristics. For this to occur, the part undergoes a bombardment of high voltage negative pulses, which vary from 10,000 to 100,000 volts. When it receives these pulses, the part attracts the positive hydrogen ions. The ions penetrate up to a dozen thousands of ångströms in depth – 1 ångström is equivalent to 10-7 millimeters, or 1 millimeter divided 10 million times. The temperature of the part, the pressure inside the chamber, and the processing time vary according to the material. “In the case of polymers, the treatment takes about 15 minutes, while materials made of steel need a longer implantation, about one hour”, Ueda claims.
After the parts are modified, they undergo tests and measurements to verify the efficiency of the process. As it is almost impossible to do these tests on the parts themselves, without damaging them, each treatment is accompanied by samples that are assessed later. “The most important test is the atomic concentration profile, which reveals whether the nitrogen ions have penetrated properly. Besides this one, we analyze the structure of the material and measure its hardness and its resistance to wear”, says physicist Luiz Angelo Berni, from LAP, who also took part in the project.
Excellent results
While the PIPE project was being carried out, Metrolab teamed up with into partnerships with several companies besides Baumer, to carry out the surface treatment on different materials and components. All the parts were provided free of charge to Metrolab. “The most surprising results were achieved with the tools from Refal, a manufacturer of rivets and riveters, based in São Paulo”, advises electronic engineer Antônio Claret Pereira Fernandes, Metrolab’s owner. In one of the parts treated, in this case a steel hammer, an improvement of over 25 times in its average life was verified, compared with a part that was not modified by 3IP.
In another, a steel follower, the prolongation of the average life was higher than four times. The principal result, though, happened to a punch for high temperature works in the production of rivets, which saw 70-fold improvement in durability. For Refal, these results represent great savings, not only for the greater durability, but also for the reduction in time on changing, which is reflected directly in the factory’s productivity. The success of the treatment has borne good fruit for Metrolab. “We are pleased because Refal has now formalized an order for processing a batch of tools used in the production of rivets and riveters”, explains Fernandes, adding that, with its current structure, Metrolab has the capacity to treat a hundred parts a week, including rivets, hammers and prostheses.
Another partner of Metrolab was AS Technology, a company specialized in the manufacture of dental implants from São José dos Campos. According to Luiz Roberto Castro de Souza Aguiar, the company’s project manager, the process of three-dimensional ionic implantation has shown highly promising results, when applied to cutting tools used in machining dental implants. In some cases, the increase in the useful life of the part was from 40% to 100%, and, in others, the quality was improved, but the useful life reduced.
“The 3IP process considerably improves the quality of machining in our application, such as, for example, not producing a superficial film, as in the case of nitriding (enrichment with nitrogen) by chemical products. The plasma inserts the ions into the tool, improving its cutting angle”, Aguiar explains, making a reservation: “Without a doubt, there is a phenomenon of improvement, but we have not yet mastered all the variables of the process”. That is why the company is continuing to do tests on the parts submitted to the 3IP treatment, to discover the ideal condition for processing.
Metrolab has also experimented with the application of the 3IP technique on PET bottles, with the collaboration of beer manufacturer Primo Schincariol. In this case, the objective of the research was not to make them more resistant, but to reduce the rate of transmission of oxygen through the walls of the polymer bottle, so as to prevent the rapid degradation, which occurs after a week or two in the case of untreated PET. At the end of the process, preliminary tests revealed that there was a small increase in the barrier against the penetration of oxygen, which brought about a slight improvement in the conservation of the product. The process, though, still needs to be perfected for the beer to be conserved for at least six months.
Clean and economical
One of the main characteristics of the 3IP method is the fact that it can be applied to parts of a large size and complex formats, because the treatment has three-dimensional reach. Besides this, the parts do not suffer any alterations in their dimensions, and implantation can be done individually or in batch, with several parts at the same time. For Ueda, the method shows advantages over the processes normally employed in the treatment of surfaces, like nitriding, which consists of putting nitrogen atoms into steel parts by means of salt baths or immersion in ammonia gas under high pressure.
“These methods are toxic and handling is dangerous, since they are carried out at high temperatures, of up to 600ºC. Not to mention that they are problematical from the environmental point of view, because they generate highly hazardous waste, as in the cyanide bath.” In comparison with the traditional methods, the 3IP treatment is similar in the economic ambit. “It also brings the advantage of treating the parts in a homogeneous manner, with the ions reaching the part in all directions and perpendicularly to the surface, besides not being aggressive to the environment”, Ueda guarantees.
The Project
Improvement of the surface properties of components for industrial use by three-dimensional ionic implantation (nº 99/06961-3); Modality Small Business Innovation Research Program (PIPE); Coordinator Mário Ueda – Inpe-Metrolab; Investment R$ 93,240.00 and US$ 121,314.75 (FAPESP)