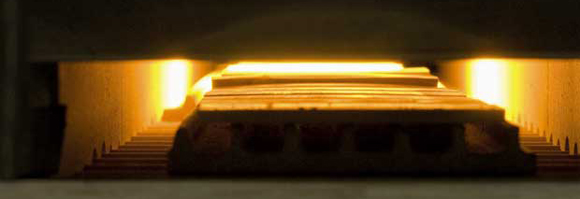
EDUARDO CESAROven for the trials conducted by the laboratory at the Center of Ceramics of BrazilEDUARDO CESAR
Brazil is now the world’s second largest manufacturer of surfacing ceramics, a segment that encompasses flooring and wall tiles, its production having reached 713 million square meters in 2008, ahead of traditional manufacturers such as Italy and Spain and trailing only behind China. Of this total, 485 million square meters were produced in São Paulo state, of which 400 million (56% of the country’s production) came out of the ovens of companies at the Ceramic Center in Santa Gertrudes, which encompasses, besides the town of Santa Gertrudes, the towns of Cordeirópolis, Araras, Iracemápolis and Ipeúna, also extending to the cities of Rio Claro, Limeira and Piracicaba. “The great advantage of the region, which has 47 enterprises in the ceramic sector, lies in the excellent quality of the raw material, a red clay that is plastic and therefore easy to mold, while also being refractory”, says engineer José Octavio Armani Paschoal, an expert in special ceramics and president of CCB, the Center of Ceramics of Brazil, a quality certified organization established by Anfacer, the National Association of Manufacturers of Ceramic Tiles for Surfacing.
The fact that the region has top grade clay is an indisputable advantage, but for it to achieve its outstanding position at the domestic stage it was necessary to undertake systematic R&D work, conducted by São Paulo researchers with FAPESP support of the Consitec (Sector Consortiums for Technological Innovations) type. The project involved everything from selecting the most suitable raw materials to the creation of new paints and special very hard, wear-resistant glazes.
When the project began, back in late 2001, the region’s tiles were of low technical quality. “At present, at least 98% of each lot fits into class A, meaning that the tiles have no defects whatsoever”, says Paschoal, a researcher who recently retired from Ipen, the Institute of Nuclear and Energy Research (Ipen). In 1997, only some 50% at most of the production of the São Paulo ceramic tiles industry rated as class A. The rest rated as class B (tiles with small surface defects) or class C (tiles with more serious defects). At that time, Brazil produced 200 million square meters of ceramics a year. The state of Santa Catarina accounted for 70% of the total produced and the state of São Paulo for 30%. “As the price of the ceramic tiles was good, companies were able to keep going despite their losses”. The situation is quite different today, when all the industries manufacture world-class products. “Currently, the profit margin is small and there is a lot of competition in the sector, so the company runs the risk of closing down if more than 2% of its tiles are defective”, says Paschoal.
The production of porcelain tiles (special ceramic products ranging from mini-tiles to very large pieces with high added value used in flooring and in the surfacing of buildings) among the São Paulo industries was one of the achievements attained at the end of the project in 2009. “When the project started, only three companies made porcelain mini-tiles, which are small pieces for surfacing and decoration”, says researcher Ana Paula Margarido Menegazzo, CCB superintendent and coordinator of two of the project’s research lines. “By the time it ended, 13 companies were making porcelain tiles”. These tiles can belong to two categories: extremely high quality technical tiles that compete with natural stone, the surface of which is not glazed, and the glazed kind.
Of the seven research lines conducted as part of the project, three centered on porcelain tiles and focused on the development of raw materials for making them, on the study of the technology of their manufacturing process, and on the formulation of special glazes. The other two lines of research ranged from innovations in the field of trials to the evaluation of products, such as the development of methodology for checking the thickness of tiles, which reduced differences in results among the laboratories, research into the technology of laying surface tiles, and even a study about the draining of the paints used to decorate tiles, a field of mechanics known as rheology. “This study is necessary because, as decoration application techniques evolve constantly, one must adapt the materials used in this task”, says Eduardo Quinteiro, CCB project manager and coordinator of the four lines of research on the Consitec project.

EDUARDO CESARAutomated production process for ceramic tiles: stamping and glazing stagesEDUARDO CESAR
When it comes to the decorative enamels used to make designs on floor or wall tiles, for instance, they must be placed exactly at the right spot and they should not run. “The São Paulo ceramic companies work with a decorative technique that uses few layers of paint to form the designs with the best possible resolution”, says Quinteiro. The project also included mapping the differences in shades observed by the human eye, which formed the frame of reference for the development of a method to improve the use of ceramic paints used by the sector’s industries.
Ceramic certification
Certain trials were conducted at the laboratories of the Ceramic Center of Brazil (CCB) and others at the Interdisciplinary Laboratory of Electrochemistry and Ceramics (Liec) of the Federal University of São Carlos (UFSCar), at the laboratories of the Polytechnic School of the University of São Paulo and at Ipen, all of which partnered the project. Although it was established in 1993 as a certifying organization, only with the help of the Consitec project and other Finep and CNPq projects was CCB able to perform this function fully, when its single laboratory was transformed into a ceramic technology innovation center. “We worked on surveying the quality and adaptation of the companies to help them meet the standards and get certification”, says Paschoal, who became the president of CCB president in 1997 thanks to his experience at Ipen. “Back then, the influence of the state of Santa Catarina was very great.”
Proof of this is that even with the entirely different clay in Santa Catarina, which is easy to mold lacks mechanical resistance, the ceramic products of the Santa Gertrudes region used a similar process for a while. This process was based on the Italian method. “In Santa Catarina, one must add structuring products during production, such as quartz and feldspar; this calls for a wet grinding process followed by the removal of the water through drying”, explains Paschoal. The red clay found near the surface of the Santa Gertrudes area, however, already had the mechanical resistance of the end product. “This totally changes the characteristics of the process, that resort to dry grinding”, says Paschoal. Just one stage suffices, rather than several. This means an industrial cost some 50% lower than that of the ceramic tiles made in the South of Brazil.
Besides dealing with manufacturing technology, the Consitec project also conducted a survey of the products made throughout Brazil. “Based on these data we prepared, in conjunction with the industry, the technical standard NBR 15 463 that is specific for porcelain ceramics and that was published in 2007”, says Ana Paula. This standard specifies the product’s features in terms of resistance to wear and to chemical products, as well as low water absorption requirements. “This standard, which was a pioneering effort worldwide, has already been presented to the ISO 189 International Committee, which works with global ceramic surfacing standards.”
The project
Sector consortium of the surfacing ceramics industry in the state of São Paulo: technological innovation and competitiveness (nº 01/10783-5); Type Consitec – Sector Consortiums for Technological Innovation Program; Coordinator José Octavio Armani Paschoal – Ipen/CCB; Investment R$ 586,715.13 (FAPESP)