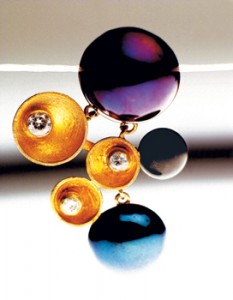
MIGUEL BOYAYANMulticolored jewelry made by Jackie-O MIGUEL BOYAYAN
At first glance, the pieces of colored gold resemble stones in unusual colors, whose hues change according to the light that shines on them. The various shades of blue, purple and other colors are obtained thanks to an innovative process that uses a high-frequency grinding technique, instead of the traditional goldsmithing processes, in order to produce powders used to make colored jewelry. To achieve yellow or red, the gold is mixed with silver or copper, alloys that are traditional. To obtain different colors, such as purple, the gold is mixed with aluminum. When iron is added, the gold becomes blue; with chrome, it turns into olive green and with cobalt, it goes black. “The choice of the metal depends on the desired color,” explains metallurgical engineer Edval Gonçalves de Araújo, of the Jackie-O jewelry company, who has been researching the technique for obtaining colored gold since 2003. Initially, this research was conducted in partnership with metallurgical engineer Ricardo Mendes Leal Neto and physicist Eneida da Graça Guilherme. “Changing some processing conditions also allows us to obtain a deep shade of green when we mix gold with cobalt,” explains Leal Neto, a researcher at the Ipen Nuclear Research Institute and a shareholder in the Alluvium company.
One has to mix gold with other metals because pure 24-karat gold is extremely flexible. “It is such a flexible metal that stretching 30 grams of gold would result in a 100-kilometer long, ultra-fine wire,” says Araújo. The 18-karat gold used in jewelry consists of an alloy that is 75% gold and 25% other metals. The same ratio is used in the new technique, which does away with melting the gold in the production of gold alloys. “The metals that comprise the remaining 25%, such as copper, silver, palladium and platinum – used in traditional goldsmithing – were replaced by chromium, iron and cobalt, among others,” says Araújo.
The first step of the process is to produce the alloy by means of high-energy grinding. The vibrating mill has small steel spheres that collide and provide energy for the powder mixture to form a solid-state alloy. After a few hours, each powder particle throughout the batch has the same chemical composition. The powder from the mill then goes into a press where it is compacted at a pressure of 2 to 7 tons per square centimeter, shaping the jewelry parts into their final form or into 20 x 25 millimeter, 1.3-millimeter thick sheets. The parts are then heated in a furnace at a temperature below melting point, a step called firing. In the case of sheets, they can be rolled after firing down to a thickness of 0.1 millimeter. These sheets can then be worked on using conventional jewelry techniques.
The parts are white when they come out of the furnace. The color of the alloy only appears after thermal treatment at temperatures ranging from 100 to 700 degrees Celsius (ºC), when surface oxides are formed in different colors. The same piece can have a homogeneous color or can come in several hues of the same color. The process can change the color of the jewel according to the client’s taste. A white engagement ring, for example, can be turned into a gold-colored one for the wedding, or into a purple, light blue, dark blue, gray or black ring. A special resin that acts as a sealant has been developed to coat the pieces to protect them from the natural wear-and-tear of metal oxides.
One of the advantages of using the high-energy grinding process to make jewelry is to obtain alloys that, under traditional techniques, would have completely different melting points. If metals such as iron, cobalt and nickel were used in the conventional goldsmithing process, the alloy’s melting point would be higher than 1,200 ºC, but for the alloy powder resulting from grinding, the firing temperature is around 1,000 ºC.
By using the high-speed grinding technique, also known as mechanical alloying, one can produce several metal alloys. This technique is part of a field called powder metallurgy and is used, for example, in car part manufacturing. To this end, steel, iron and bronze powders are compacted inside a high-tonnage hydraulic press to shape the part, which is then sent to a controlled atmosphere furnace for firing. The finishing is the next step and then the part is ready. “This is not a new process, but it had not yet been used to make colored gold alloys,” says Leal Neto.
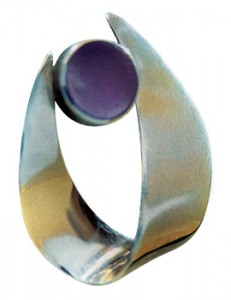
Eduardo CesarMulticolored jewelry made by AlluvionEduardo Cesar
High energy
Araújo applied the high-energy grinding process during his master’s degree program at Ipen, in the early 90’s. He chose this technique to produce an expanding agent for mortar made from aluminum scrap, for use in construction, a project funded by FAPESP. This project began in 2001 and ended in 2002 (see Pesquisa FAPESP nº 81). Leal Neto worked with intermetal compounds, a category that includes some colored gold alloys, during his doctoral studies, beginning in 1993, at Ipen’s Materials Research and Technology Center.
The two researchers combined their knowledge in this field and, in partnership with Eneida Guilherme, created the Regulus Ars company with the objective of obtaining colored gold alloys. This project was funded by FAPESP through its PIPE – Innovative Research in Small Companies program, initiated in November 2003. In the first phase, the researchers managed to obtain powders and small solid samples in blue, red and purple. During the project’s second phase, the company moved to Cietec, the Innovation, Entrepreneurship and Technology Center at Ipen, at the University of São Paulo campus, in São Paulo City. Concurrently, another PIPE project for the manufacturing of colored gold artifacts, coordinated by Araújo, was approved in 2004.
The Regulus partnership ended in 2006, leading to the spin-off of two firms. Leal Neto and other partners established Alluvium, which remained at the Cietec facility until July of this year, and they continued to work on the first Pipe project, which was concluded in April 2008. “We manufactured some pieces of jewelry to show the feasibility of the technique,” says Leal Neto. Araújo established the Jackie-O company, located at Intes, the Technological Incubator of Companies in the town of Sorocaba, State of São Paulo. The new company enabled him to continue working on the Pipe project that he had coordinated. The project was concluded this year in July.
Both companies use the same process to make the colored gold powders. However, Alluvium and Jackie-O started to develop their own alloys and techniques to obtain the colored gold products. At present, the Alluvium partners are looking for partners to develop applications for this material. “One of our future partnerships will probably be established with jeweler Silvia Furmanovich,” says Leal Neto. “As she likes to work with new materials, she is very keen on the possibilities of using colored gold powders to produce unique jewelry.” In addition to making material for jewelery, the company’s strategy is also to develop the product’s application in other fields, such as ceramics. In this case, the pigments would be used to color high-end ceramic tiles. Leal Neto believes that extensive marketing work must be conducted to acquaint consumers with colored gold, as the colored shades mixed with yellow gold can be mistaken for resins or other lower-end materials.
Araújo is also hoping publicity will help him place his colored gold pieces on the market. In partnership with goldsmith Rodolfo Penteado and materials engineer Oswaldo Vilela da Silva Junior, he has designed a collection of earrings, charms, necklaces and wedding rings. Jackie-O itself will manufacture and distribute the colored jewelry. “We expect to place our product on the market by the end of this year,” says Araújo. To this end, he hired the junior company from the School of Arts and Communication from the University of São Paulo to do the communication planning for the product, while the consulting service of Getulio Vargas Foundation is to analyze the market.
The projects
1. Obtainment of colored gold alloys through high-energy grinding (nº 03/02133-6); Type Pipe – Innovative Research in Small Companies; Coordinator Eneida da Graça Guilherme – Alluvium; Investment R$ 325,664.02 (FAPESP)
2. Process for the manufacturing of colored gold artifacts (nº 04/14290-1); Type Pipe – Innovative Research in Small Companies; Coordinator Edval Gonçalves de Araújo – Jackie-O; Investment R$ 497,965.02 (FAPESP)