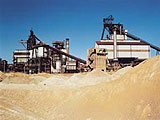
cstSlag stocked at Companhia Siderúrgica de Tubarão to be transformed into cementcst
Brazilian productive sectors have turned, with greater frequency, to more efficient and cleaner processes and systems, with the goal of improving the use of raw materials, diminishing waste, and seeking the recycling of industrial products and leftovers. The result of this series of new procedures is a substantial reduction in costs and the possibility of winning new foreign markets, increasingly more demanding with regard to production processes that cause less aggression of the environment. “The adoption of clean technologies leads the companies to save a lot of money and to increase their sales”, says Professor Luis Nunes de Oliveira, the assistant coordinator of the areas of exact sciences of FAPESP’s scientific board. “In addition, the company ceases to be fined in cases, for example, where it used to throw waste into rivers.”
Within this strategic policy for the country, seven projects financed by FAPESP expand and launch new prospects for the use and development of clean technologies. These projects encompass everything from civil engineering and building to the recycling of metals and reuse of packaging. “Civil engineering and building is the industry that causes most aggression to Nature, due to the great quantity of natural resources that it demands”, recognizes Vahan Agopyan, a civil engineer and a professor at the Polytechnic School of the University of São Paulo (USP).
Agopyan’s studies are centered on projects that have the objective of re-using what is thrown away as trash. Among the most important is the one that transforms slag residue from the production of steel, worthless, into an important component in making an innovative cement: two times more resistant and 40% cheaper than common cement. In the new cement, which has resulted in the registration of a patent, the slag performs a fundamental role. Combined with activators, which are substances made up of compounds of silicates of sodium, sulfates, and calcium hydroxides, the cement acquires low alkalinity, which makes it possible to add fibers to the mixture. Glass fibers make slag cement a material that is resistant and easy to mold.
“Slag used to have a ridiculous value. Our research has added value to this waste, transforming it into an excellent material from the industrial point of view”, says Agopyan, who coordinated the project Slag Cement Panels Reinforced with E Glass Fiber, developed under the auspices of FAPESP’s Partnership for Technological Innovation Program (PITE).
Two years ago, when this project was concluded, the steel mills had no alternative but to pay to dump this waste in industrial landfills. Due to the high costs, a large part of the slag was abandoned in the environment, contaminating the ground and the water. “With time, slag hardens and forms rocks made up of heavy metals that contaminate the water table “, says Agopyan. Each year, Brazilian steel mills obtain some 6 million tons of slag from the blast furnaces as a sub-product of making steel. Today, not only do they save what they used to spend to give it a final destination, but they also make money from the slag.
Sale of slag
Companhia Siderúrgica de Tubarão (CST), in Vitória, Espírito Santo, supported the project and presently sells US$ 9 million worth of slag to four cement companies. Previously, all its production of 1.7 million tons a year had as its destination just two companies that used to stock the product on their land. “Our customers didn’t know what to do with so much slag”, says Paulo Lana, CST’s special sales manager. Agopyan is the first Brazilian to be a member of the board of directors of the International Council for Research and Innovation in Building and Construction (CIB), an institution that has been in existence for over 50 years, as its vice-president.
“This concern with the environment is no craze”, he says. Both the CIB, which changes the theme for its congresses every three years, went back to the same subject it had addressed in 1998: sustainable construction. Another of Agopyan’s contributions to this theme – along with other researchers from USP – was to assist with the text of a resolution of the National Council of the Environment (Conama in the Portuguese acronym) on “Waste from Civil Engineering and Building”, which will give more responsibilities to the municipalities to supervise contractors and transportation companies in the creation and transport of rubble from civil engineering and building.
Based on this resolution, there will be more rules to be complied with by the contractors and owners of rubbish skips, who will also be responsible for depositing waste. At the moment, the text of the resolution is being analyzed by Conama’s technical chamber for environmental control. Civil engineering and building still has a serious problem to solve. It is the presence of asbestos in the composition of roofing tiles. The use of this mineral is prohibited in 21 countries, due to the problems of health that it causes.
From January 2005, the decision will be valid for all the member countries of the European Union. But in Brazil, the mineral fiber is still being used by the manufacturers of water tanks, roofing tiles and brake pads. The project for a federal law that would banish asbestos for once and for all from Brazilian industry, with the argument that this material is carcinogenic and causes lung diseases, was not approved, but replaced by another, that establishes control over its use.
Vegetable fibers
But the replacement of asbestos in Brazilian roofing tiles is under way, with a PITE project – the Development of Technology for Making Fibrocement Roofing Tiles without Asbestos -, developed in partnership with the companies Infibra-Permatex, from São Paulo, and Imbralit, from Santa Catarina. The main function of the project is to eliminate asbestos and to introduce vegetable and plastic fibers in the manufacture of the tiles. The growing use of these materials is a world tendency in civil engineering and building. When mixed with vegetable fibers, cement becomes more suitable for the production of slim equipment that is more resistant to dynamic forces.
“Brazilian industry has the big challenge of developing technologies for the use of fibers that are clean and economically viable at the same time”, says the coordinator of the project, Professor Holmer Savastano Júnior, from the School of Zootechny and Food Engineering of the University of São Paulo (USP). The project provides for the manufacturing of tiles reinforced with plastic and cellulose fibers. A renewable raw material, cellulose fibers are internationally accepted. The intention is to use fibers of eucalyptus and pine, to strengthen the tiles, and plastic fibers, which give them long term resistance. In the current stage, the researchers are testing these raw materials on a laboratory scale.
Rice husk
Another vegetable fiber that can be useful as a raw material in supplies for the construction business is rice husks. Not in its natural state, but with the extraction of the silica that exists in this fiber to be used in concrete structures. Rice husks are today a big environmental problem in Brazil. Every year, 10 million tons of rice husks are discarded – and 400,000 tons of silica -, and are burnt or left on the ground. To make use of the potential of this residue, at USP in São Carlos a project is being developed on High Performance Concrete with Rice Silica, coordinated by Professor Jefferson Libório, of the Laboratory of Civil Engineering of the Department of Architecture and Urbanism of the School of Engineering. The researchers have developed a method for extracting silica from rice husks and have confirmed its application in concrete structures.
Libório developed the technology along with Professor Milton de Souza, from the Institute of Physics and Materials Science at USP. The joint work now has a patent request and is about to be put onto the market. “Several companies are interested, but we have to keep the names secret while they are doing the tests”, says Libório. Another focus for the development of clean technologies lies in the recycling of discarded products. Although sending beer and soft drinks cans for recycling is popular, only 229,000 tons of aluminum out of the 1.5 million tons produced in Brazil recovered from scrap in the course of 2000, according to a survey made by the Brazilian Aluminum Association (Abal).
In the assessment of Professor Antonio Carlos da Cruz, of the Institute of Technological Research of the State of São Paulo (IPT), this percentage should increase gradually. Among the many advantages, recycling consumes much less electricity than is needed to produce aluminum from bauxite, 5% at the most. But for the recycling processes to become really clean, the new technologies have to be perfected. Cruz coordinates research that is regarded as innovative, for the fact that it does away with the use of salts in recycling aluminum.
Used to protect the aluminum itself against oxidation, these salts create residues that contaminate the environment. The project Recycling of Aluminum: Development of Innovative Technologies provides for the control of the atmosphere of the furnace, preventing to the maximum the presence of oxygen, and it replaces combustion, which calls for the use of this gas, by the use of thermal plasma to heat the furnace. This product is obtained by passing an electric current into a gas, forming the plasma, a substance that is capable of reaching a temperature of up to 20,000 degrees Celsius.
Industrial scale
The funds invested in the project by FAPESP and by six companies represented byAbal made possible both the technology and the rotating furnace, with the capacity to process 300 kilos of material – a sufficient volume to show performance on an industrial scale. The only thing missing is an inspection of the conditions of safety, for the furnace to start to operate, recycling aluminum swarf, cans, pans, engine blocks and frames used in windows and doors. The advantage of plasma for recycling aluminum lies in the fact that this process does not produce waste, nor any toxic and dangerous effluents. One of the companies that are candidates for availing themselves of this new technology is Latasa, which manufactures 6 million cans, half of them from recycled aluminum.
Today, the process used for recycling 40,000 tons of the company’s aluminum uses salts that have to be disposed of, generating an addition cost for them to be eliminated safely. The manager of Latasa’s Recycling Center in Pindamonhangaba, in the Paraíba valley, Antonio Paulo Galdeano Damiance, does not reveal the quantity of salts used in the recycling, nor the cost with final disposal, but he does assure that Latasa has cut down the salt over the last three years, and, as a consequence, the residues, by 45%. According to this manager, this is due to the application of American technology to the process. With the help of researchers from USP, the company has a chance of reducing this level to zero.
Less energy
The advances in the area of recycling of aluminum do not stop there. A new kind of electrolytic refining of aluminum, one of the processes for recycling this metal, has become economically feasible, due to a technology developed at the Institute of Energy and Nuclear Research (Ipen), through the project Development of a Process of Electrolytic Refining (recycling) of Aluminum Scrap in Baths of Cast Chlorides. Until a short while ago, this process demanded as much electricity as it is consumed in the production of primary aluminum.
By replacing the fluoride salts (compounds of fluorine) by chlorides (based on chlorine), and, using this, restructuring the process, Professor Marcelo Linardi, from Ipen, reduced the consumption of electricity by two thirds, from 15 kilowatts (kW) to around 4 kW per kilo of recycled aluminum produced. With these innovations and other modifications in the process, he built an electrolytic refining cell and is obtaining aluminum with a purity of 99.8% from scrap.
Life cycle
If the destination of aluminum cans was recycling for 78% of the units produced in Brazil in 2000, other kinds of packaging are still not meeting the same success. Although technology for recycling exists, paper and plastic, for example, have not yet achieved high levels of re-use. The main reason is that a kilo of these materials costs far less than aluminum. But their lower value has not affected studies into packaging of paper and cardboard, glass, wood, plastic, steel and long-life milk. In the field of academic research, these kinds of packaging deserve the same attention.
Brazil now has a vast database with the results of the assessments of these materials, with figures and tables of consumption of fuel, electricity, water and all the other input needed for their manufacturing and for the life cycle of these kinds of packaging. This database was built up in the course of the project Analysis of the Life Cycle of Packaging for the Brazilian Market, under the PITE, which was concluded in 1999 and developed by researchers from the Center for Packaging Technology (Cetep), of the Institute of Food Technology (Ital), in Campinas.
According to Anna Lúcia Mourad, a chemist who is a member of the research group, the database, the first version of which was concluded in 1998, is frequently updated. “We made a complete, detailed, survey of everything that is consumed to make a cardboard box”, explained Anna Lúcia, who is responsible for the area of cellulosic materials in the research.
Corrugated paper
This is not the only one of Cetea’s project that is in tune with the proposal for cleaner production. Another one, developed under the auspices of PITE and entitled Development of Corrugated Paper Packaging Systems for Fruit and Vegetables, also has a strong environmental character. In partnership with the Brazilian Corrugated Paper Association (ABPO in the Portuguese acronym), Cetea developed three kinds of boxes of corrugated paper, for the storage and transport of tomatoes, oranges, grapes, eggplants, cucumbers, peaches and carrots. Since 1999, when the project was concluded, the paper boxes have been available for the fruit and vegetables market chain, which previously had no option but the wooden boxes.
Technical standards
Corrugated paper has at least two advantages over the wooden box. The first for being disposable and recyclable, which increases the degree of cleanliness of the fruit and vegetables marketed. The other is related to the greater compatibility of paper with the fragility of the products. In wooden boxes, losses of market garden products come to 30%. According the food engineer Eloísa Garcia, a researcher at Cetea, “the loss of products through shortcomings in packaging brings negative consequences for the environment, very often greater than the environmental cost of making and eventually disposing of a suitable packaging product”.
From cement to packaging, all sectors are seeking excellence in less toxic products and systems and which spend less electricity. Initiatives for a world more focused on the concepts of clean technology are encouraged, including by the United Nations (UN). Since 1995, the capital of the state of Rio Grande do Sul, Porto Alegre, has been the Brazilian headquarters of the National Center for Clean Technologies (CNTL in the Portuguese Acronym), founded with the support of the United Nations Industrial Development Organization and the United Nations Environment Program. In recent years, these institutions have helped to set up clean technology centers in 22 developing countries. The center receives support from the National Service of Industrial Apprenticeship (Senai) and is installed in its premises.
“The final destination of the residues ends up being costly to the companies. When they cut down these residues at the origin of the process, it makes them more competitive”, says Hugo Springer, a CNTL director. With the support of this center, companies linked to Senai have made their production cleaner in various sectors of industry: shoes, furniture, metal/metalworking, foodstuffs and pulp. The engagement in this common effort also includes the Brazilian Association of Technical Standards (ABNT). A point of reference for the business world, the ABNT gave its most recent contribution last November, with the launching of ISO 14040, which comes as an addition to the ISO 14000 standards aimed at environmental protection.
According to Hubmaier Lucas de Andrade, the coordinator of the life cycle subcommittee of the ABNT, the new standard steers companies in a revision of the whole productive chain, through the analysis of the life cycle of the process. “ISO 14040 is a voluntary tool that is not certifiable, but it helps companies to take decisions to perfect the process”, says Andrade. In the assessment of the coordinator, the application of the standard facilitates the definition of priorities in the development of clean technologies.
“In Brazil, we have to build an institutional arrangement that allow companies to gather information on their life cycle data, from the use of raw material to post-consumption”, Andrade reckons. For all these reasons, the new century is pointing towards a prospect of clean technologies. A condition for the planet to continue to live through other centuries.
Republish