
Zaramella, from ACS, and Novais, from Itaipu: a technology partnershipAlexandre Marchetti / Itaipu Binacional
Brazil’s first manned electric aircraft is scheduled to take off in March from the runway at São José dos Campos Professor Urbano Ernesto Stumpf Airport, in the interior of the state of São Paulo. Planned flight time is 10 to 15 minutes. The two-seater has one electric engine and was named Sora-e. The testing program will continue over the next few days until the aircraft flies for an hour and 30 minutes at a cruising speed of 190 kilometers per hour (km/h), its maximum range. After that, in April, the airplane will head to Iguaçu Falls, in the state of Paraná, where it will be put through a second and final series of tests, performed with ACS-Aviation, the company that developed the airplane, and its crew from the Center for Research, Development and Assembly of Vehicles Powered by Electricity (CPDM-VE) of Itaipu Binacional, a partner in assembling the aircraft. And then the Sora-e project (a concept aircraft) will be complete. The next challenge will be to develop a commercial version of the electric aircraft.
Engineer Alexandre Zaramella, managing partner of ACS and creator of Sora-e, says that it will take two years of work to develop this new version. The goal is to build two new versions: a sports version and another for training. The first one will be a motor glider. The aircraft will use the electric engine to take off (eliminating the air towing requirement that gliders have) and for landing maneuvers. With the electric power plant, the aircraft can glide for more than three hours. The second version will be used to sell electric aircraft to train pilots.
Manufacturer: |
ACS Aviation – São José dos Campos |
Technology partnership: |
Center for Research, Development and Assembly of Vehicles Powered by Electricity (CPDM-VE) of Itaipu Binacional |
Power plant: |
Two electric engines powered by lithium batteries |
Seating: |
1 pilot and 1 passenger |
Uses: |
As a glider that requires no air towing or pilot training |
Thinking in the long term, Zaramella sees much greater potential for his firm and his electric aircraft project. Commercial aviation, through the International Civil Aviation Organization (ICAO), has made a commitment to improve the energy efficiency of airplanes and, over time, to slash carbon emissions in half by 2050, based on 2005 figures. “To comply with this rule, the industry will have to use unconventional power plant systems, such as electricity,” Zaramella says. “Today there are only about a dozen companies in the world that build electric airplanes. When Sora-e takes off, we will be one of the few companies with an aircraft that has undergone in-flight testing. All the others will be keeping an eye on the solutions we develop, and this opens up new business opportunities,” he says.
Airbus is one of the few large companies working on developing electric airplanes. In April 2014, in Bordeaux, France, this European firm conducted the inaugural flight of the e-Fan 2.0 prototype, a two-engine two-seater with total power of 60 kilowatts (kW) that runs on a lithium-polymer battery. The range is one hour, with a 15-minute reserve. The aircraft is being developed to train pilots. In addition, Solar Impulse 2 flew for the first time last year at an air base in Switzerland. The airplane has four electric engines powered by 17,200 solar cells placed in a set of wings larger than the wings of a Boeing 747. It is an experimental airplane, and two of its developers, Andre Borschberg and Bertrand Piccard, plan to fly it around the world in 2015.
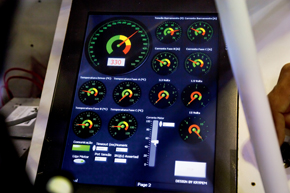
An instrument that analyzes aircraft enginesALEXANDRE MARCHETTI / ITAIPU BINACIONAL
Electric engines in the aeronautics industry are replete with potential for two reasons, according to Zaramella. The first reason is environmental, since these engines do not emit polluting gases into the air and they generate little noise. The second is economic, a consequence of the greater efficiency of electric engines compared to combustion engines that use gasoline, ethanol, diesel fuel and kerosene, in which 73% of the energy is wasted. In an electric vehicle, total wastage is 10%: 8% in the battery and 2% in the engine. If we add the energy that is wasted before the fuel reaches the vehicle, the difference is even greater. In a refinery, 12% of refined oil is wasted, while the energy wasted in the electricity generation and distribution process is 5%. “Today, to move the fleet of automobiles in Brazil, we burn energy equivalent to what 9.3 Itaipus hydroelectric dams generate in a year. If the fleet were electric, 1.5 Itaipus would meet the demand,” says engineer Celso Novais, the Brazilian coordinator of the Itaipu Binacional Electric Vehicle Project.
However, Novais says that the challenges to be overcome to make electric vehicles popular are still significant. Costs must be reduced and the shelf life of batteries must be longer. The range of the vehicles must be increased as well, recharging time must be shortened and infrastructure must be built for recharging vehicles. At the same time, investments must be made in new models of spare and other parts to make them lighter and suitable for electric power plants. “The CPDM-VE at Itaipu has dedicated its work to developing solutions for each of these problems, and that is our task at hand,” Novais says. The Binacional electric vehicle program was established in 2006 (see Pesquisa FAPESP Issue No. 173). Through partnerships, more than 100 electric Palio Weekends have been produced with the FIAT team at the Itaipu facilities, and 32 Renault Twizy compact vehicles will be assembled as well. The Twizys arrived in Brazil in 2014 in the SKD (semiknow-how) configuration–in other words, partially assembled. “The CPDM-VE has already produced electric versions of trucks, cars, jeeps and buses, and it is working on producing a hybrid bus that runs on ethanol as well as light vehicles on tracks (LVT) for use in urban transportation. All of these projects are in the field of electric mobility technology and focus on supporting the industry for domestic production,” Novais explains.
In aircraft that use electric power plants, the challenges are even greater, Novais says, due to the fledgling chain of suppliers of spare and other parts, with many parts being developed almost from scratch, as was the case for the Sora-e. Alexandre Zaramella notes that they had to resort to homemade solutions in some cases, such as for producing the battery and control software programs. Moreover, suppliers had to be found that developed special materials and special orders had to be placed for customized parts. “We do more than just assemble planes; we are developers because there are no off-the-shelf parts to build an electric airplane,” he says.
The Sora-e has two electric engines, 35 kW each. They are the Enrax model supplied by Enstroj of Slovenia. The power comes from six polymer lithium ion battery packs for a total of 400 volts. The batteries were assembled by ACS itself using cells made by Kokam of South Korea. The airplane uses a fixed pitch propeller made of wood and carbon. It was developed by ACS and Craig Catto of California. Catto is one of the most acclaimed makers of propellers for experimental airplanes in the world. With this configuration, the ACS electric airplane climbs at the rate of 1,500 feet per minute and reaches a maximum speed of 340 km/h with a range of 1 hour and 30 minutes, traveling at 190 km/h.
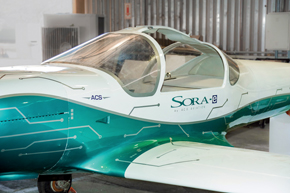
At Iguaçu Falls, details of the Sora-e cockpitALEXANDRE MARCHETTI / ITAIPU BINACIONAL
The road to development
The Sora-e project began in 2010 when ACS was awarded a R$500,000 grant from the Brazilian Innovation Agency (FINEP) to develop an electric system for airplanes. The project ended in September 2014, when Sora-e was certified with bench tests and simulators made by the CPDM-VE through Itaipu. ACS-Aviation was founded in 2005 in São José dos Campos by Zaramella and two partners who are no longer with the firm. All are mechanical engineers who graduated from the Federal University of Minas Gerais (UFMG) and worked for Embraer at one point. The company’s first product was Sora, an aircraft that runs on fuel. It is light and sporty and is used for acrobatics. The Sora-e is the electric version of this airplane. ACS also develops UAVs: unmanned aerial vehicles, both electric and combustion, for military and civilian use. In addition, the company provides engineering services for the national defense industry.
According to Zaramella, the main challenge for the new stage of the ACS electric airplane project is to increase the aircraft’s range. To do so, there are developments on two separate fronts. ACS is not involved in one of them: developments in the international lithium battery industry. Zaramella says, however, that the prospects according to international publications and forums are excellent. “We believe that in 2018 we will have batteries capable of keeping flights aloft for four and five hours at a cruising speed of 250 km/h in a two-seater electric airplane,” he says.
Composite solutions
Longer flight ranges can also be achieved at ACS by making the airplane lighter. The lighter the airplane, the less energy it requires to keep it aloft. The company is focusing on this issue, Zaramella says. The Sora-e has a wingspan of eight meters (from one tip of the wing to the other) and weighs 650 kg, 100 kg of which is just the battery, and the engine weighs 26 kg. The structure is made of a carbon fiber-based composite, which does make the airplane lighter. The structural components it uses are made in Brazil, developed from studies of composites. For a new model of an electric airplane, Zaramella says, ACS is now studying the application of innovations in carbon composites. They are being developed through two projects that are part of FAPESP’s Innovative Research in Small Businesses Program (PIPE), run by Multivácuo Aeroespacial and led by Professor Jossano Marcuzzo of the São José dos Campos State Technological Colleges (Fatec-SJC).
Celso Novais, from Itaipu Binacional, says that the CPDM-VE is closely monitoring solutions using materials found by ACS. “ACS has been very effective in finding alternatives using materials that reduce the aircraft’s weight without causing a loss of mechanical resistance. We are analyzing the viability of these solutions in other vehicles,” Novais says. At this time the Itaipu electric vehicle project team is working on developing a hybrid electric bus that will run on ethanol and sodium batteries for use in the 2016 Olympic Games in Rio de Janeiro. “Today the great majority of bus chassis are made with iron so that they withstand mechanical forces, which makes them heavy. But if we prove that the composite that was used for the Sora-e can work for producing chassis, we will have a lighter bus that will run on less fuel,” Novais says.
Republish