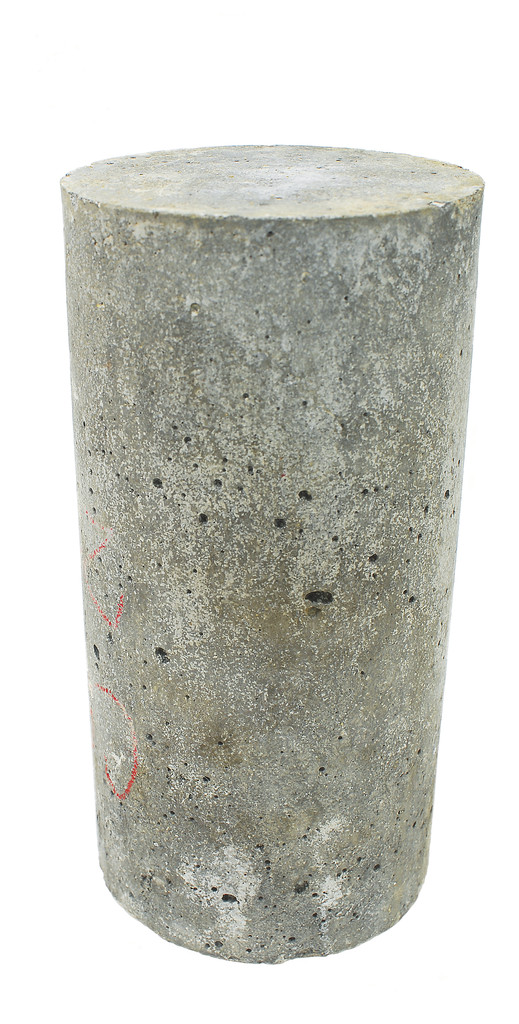
LÉO RAMOS
Concrete trial sample…LÉO RAMOSThe ashes from sugarcane bagasse and rice husks and the waste from the ceramics industry are candidates in the preparation of concrete to reduce the amount of cement used in concrete. Reduction in their use and the resulting limits in the process of industrialization are important factors for the environment, because in addition to taking advantage of these materials, which are often difficult to discard and reuse, this helps to cut carbon dioxide (CO2) emissions into the atmosphere. The cement industry accounts for 7% of CO2 emissions worldwide. According to data from the Intergovernmental Panel on Climate Change (IPCC), for every ton of cement produced, one ton of CO2 is released into the atmosphere.
“In Brazil this corresponds to 0.67 t, because part of the raw material used in the country for producing cement comes from the slag (clay separated from the ferrous material) from blast furnaces of steel mills, and the energy or electricity used in the process is renewable, as it comes from hydroelectric power stations,” explains professor Romildo Toledo Filho, from the Coordinating Office of Post-graduate Engineering Programs (Coppe) at the Federal University of Rio de Janeiro (UFRJ), coordinator of the team that has developed studies for adding waste to cement. In 2007, some 44 million tons of cement were produced in Brazil, yielding 29.4 million tons of CO2. Toledo calculates that with the inclusion of waste one could reduce Brazilian emissions by almost 6 million tons, by substituting 20% of the cement production.
The information gathered by the group from Coppe indicates that there are some 10 million tons of waste available for use by the cement industry. Around 1.5 to 2 million tons are ashes from burning sugarcane bagasse, produced by the boilers and generators used to generate electricity for the refineries themselves. “Bagasse ashes are rich in amorphous silica, which is unlike the crystalline form found, for example, in sand. In the amorphous form, it can react at room temperature with calcium hydroxide, one of the by-products at hydrating cement.” This same structure is found in the calcined husks of rice. For every ton of rice harvested there are 200 kg of husks. In Brazil, rice production reached 11 million tons in the 2006-2007 harvest, therefore yielding 2.2 million tons of husks. “To be integrated into concrete, both sugarcane bagasse and rice husk ashes must undergo a micronization process, when the material is turned into much smaller particles.”

LÉO RAMOS
…uses rice husks …LÉO RAMOSThe Brazilian ceramics industry produces some 5 to 6 million tons of waste from its production of tiles, bricks and flooring. This material, once it is calcined and milled, can replace as much as 20% of the total volume of cement. A specific study on the use of waste from this industry was carried out by the group from Coppe and presented in the September 2007 edition of the journal Cement and Concrete Research. Another non-usable product that is an alternative, but that can only replace cement to a smaller degree (from 5% to 10%), are the ashes from burning the clay at urban solid waste treatment stations.
Sustainable development of concrete is the result of concerns voiced both in the IPCC and in the clean development mechanisms presented at the Kyoto Protocol and it is appearing at a point in time when global cement consumption is rising, particularly in China, which uses 43% of all the cement produced in the world. “Calculations by researchers from the area, based on the growth of large emerging countries, indicate that if current cement consumption is 2.5 billion tons a year, it will jump to 6.5 billion tons in 50 years time, because it is, and will continue to be, the material that is used the most around the world for infrastructure,” says Toledo.
A binding element
The cement industry’s main problem is its emission of CO2 during the burning of calcium carbonate (CaCO3) to transform it into calcium oxide, which accounts for 65% of the composition of cement. Ferrous oxide, aluminum and plaster are also used as ingredients. Cement functions as an element that binds together the components of concrete, such as water, sand and gravel.
The inclusion of waste still has no prospect of being taken up by the cement industry. “Our work is academic and looking for solutions. It is up to the industry to implement them.” The southeast is the biggest cement consuming center and also the biggest waste producer. “At this time we are conducting a study to identify the areas that produce bagasse and rice husk ashes, the ceramics industry and where cement producers are located. In the end we will have a map that will help with the logistics for using the waste.”
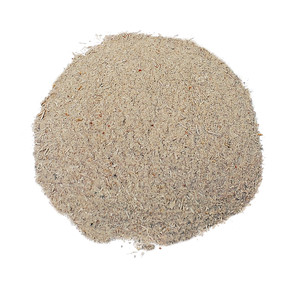
LÉO RAMOS
…in the form of silicaLÉO RAMOSThe importance of the Coppe studies can be measured by news published recently in the French newspaper Le Monde (March 13). Various cement producers in the world are developing solutions for reducing the production of cement and the consequent emission of CO2 into the atmosphere. The French group Lafarge, which produced 135 million tons of cement in 2007, has already managed to reduce its emissions of carbon dioxide by 16% out of a planned total of 20% between 1990 and 2010. In addition to top performance, ultramodern plants, even in China, Lafarge, like other cement companies, is reducing the use of fossil fuels for heating the enormous furnaces in which cement is produced. To do so, companies are turning to various used oils, solvents, tires, plastics, nut-shells from Malaysian palm trees , rice husks from the Philippines, coffee husks from Uganda and animal meal. In manufacturing its cement and in substituting part of the calcium carbonate used, the French company has also introduced ashes from thermo-electric power stations and the steel mills’ slag.
Republish