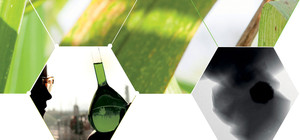
Shown above is a microscope image of a catalytic alternative to reagents consisting of clay and magnetite microspheres, in an experiment at UFSCARLÉO RAMOS CHAVES | ARLENE CORRÊA / UFSCAR
With environmental stewardship growing in importance as a global concern, the chemical industry has been faced with the challenge of finding new alternatives to petroleum-based products. According to data from British oil major BP, global oil reserves in 2016 were sufficient for another 50.6 years of production. But the use of oil products has been increasingly constrained by both economic factors, such as price volatility, and environmental concerns including global warming, ozone depletion and pollution. Novel pathways to developing alternatives to petrochemical compounds, or new substances for industrial use, have been collectively termed as “green chemistry”.
The concept of green chemistry—which includes efforts to reduce dependence on oil—first emerged in the US in the 1990s, and more prominently in 1998 when John Warner and Paul Anastas enumerated 12 principles to guide the development of this new field in their groundbreaking book Green Chemistry: Theory and Practice. “Early environmental initiatives date as far back as the 1960s in Europe and especially Germany. In the 1990s, industry was the first to stir in response to the issue of chemical contamination, in a bid to improve production processes and consumer reputation. Government regulators and then academia soon followed suit,” says Vânia Gomes Zuin, a professor at the Federal University of São Carlos (UFSCAR) and visiting professor at the Green Chemistry Center of Excellence at the University of York in England.
Progress in green chemistry, however, has been constrained by the wide variety of cheaply priced petrochemical products and a lack of sustainable substances and processes to replace them. The 2000s, however, saw the development of a number of novel solutions, with vegetable oils such as soybean and corn oils emerging as promising candidates to replace oil products. One solution involving the use of biomass, which could help to change the face of the chemical industry, was developed by US-based Elevance in 2007. The solution uses a process that breaks down vegetable oil molecules to produce feedstocks for detergents, waxes, solvents and oils for cosmetics. Elevance uses a catalysis technology (to accelerate chemical reactions) called olefin metathesis, which can replace some petroleum-based products, uses less energy, produces less waste and reduces harmful greenhouse emissions.
The seminal research that led to the development of this innovative process was recognized by a Nobel Prize in Chemistry awarded in 2005 to French chemist Yves Chauvin and Americans Robert Grubbs and Richard Schrock for their development of metathesis. Metathesis is a reaction of two organic molecules with chains containing double bonds that have similar groups and are exchanged to allow the synthesis of new chemical compounds at lower temperatures and pressures using metal catalysts. Founded as a spinout of Cargill and Materia, Elevance was selected as the 2012 winner of the US EPA’s Presidential Green Chemistry Challenge Award for its use of the metathesis process. The company operates two plants in the US and one in Indonesia using palm oil. Palm oil has the advantage that it is cheaper than oil from soybeans and corn, two crops that are high in demand as ingredients in food and animal feed.
The 2016 edition of the EPA awards spotlighted another company for its development of a solution using microorganisms to replace petroleum-based materials. US-based Verdezyne developed a Candida sp. yeast fermentation platform to produce dodecanedioic acid (DDDA) for use in the manufacture of a type of nylon fiber used in engineered plastics with high chemical resistance, as well as adhesives, coatings and lubricants. The company was founded in 2008 and in 2014 began small-scale production of the new product from a variety of vegetable oils. Verdezyne is currently developing a plant in Malaysia where commercial production from palm oil is due to commence in 2018.
Developments in Brazil
A notable example of renewable chemistry originated in Brazil. Braskem, the world’s fifth largest petrochemical company, created an innovative, world-class green plastic solution that has been produced from sugarcane ethanol at its Triunfo plant in Brazil since 2010. Braskem’s resin is used to produce more than 150 products worldwide, including food packaging, personal care and cleaning products, cosmetics, dairy beverages, and plastic bags. The biopolymer was developed through a research effort involving engineers, chemists, and technicians and an investment of US$290 million. Braskem currently has the capacity to produce 200,000 metric tons of renewable resins. While the company does not openly disclose whether there is currently a significant price gap between cane- and petroleum-based resins, when the product was first unveiled at a fair in Germany in 2007, commercially produced green plastics were estimated to cost 15% to 20% more than petroleum-based counterparts. With inflation-adjusted oil prices now about 56% lower than in 2007, competitive pricing remains among the economic hurdles to the development of green chemistry.
Green polyethylene is currently exported to the US, Europe, and Asia. “Braskem is a prime example of Brazilian innovation in green chemistry,” says Zuin of UFSCAR. The next projects in the pipeline are under development at a biotechnology laboratory in Campinas. “These projects carry a high risk as they involve, for example, genetically engineered microorganisms and biomass,” says Mateus Schreiner, Braskem’s global manager for Renewables Innovation.
Another Brazilian player, Nexoleum, uses soybean oil as the main ingredient in a plasticizer for polyvinyl chloride (PVC). “Customers use soybean oil in replacement of dioctyl phthalate (DOP), a petrochemical product used to make PVC [better known for its use in rigid pipes and fittings] malleable for use in the manufacture of wire and cable, artificial leather, food packaging films, and toys,” explains Nexoleum CEO Jacyr Quadros Júnior. Founded in Cotia, São Paulo, in 2007, the company markets the ingredient to companies producing end products. “Customers pay 5% to 10% less than for an equivalent petroleum-based product,” says Quadros. The technology was originally licensed from Battelle, but Nexoleum has since developed its own proprietary technology for the same production process. In 2016, the company entered into a joint venture with Elekeiroz, an Itaú Group chemical company that had operations in the plasticizer business and was looking to make a foray into green chemistry. “With the support of Elekeiroz we can now launch into global markets,” explains Quadros.
Reducing waste in chemical processes is one of the reasons researchers are working to replace current feedstocks and processes with green solutions. “In conventional processes, reagents are used in the same amount as raw materials in chemical reactions. As a general rule of thumb, every 1 pound of raw material requires around 1 pound of reagent. Processes using catalysis require only 10% of other compounds (catalysts) instead of reagents, which minimizes waste,” says chemist Arlene Gonçalves Corrêa, a professor in the Department of Chemistry at the Federal University of São Carlos (UFSCAR) and coordinator of the Center of Excellence for Research in Sustainable Chemistry (CERSusChem), a collaboration with GlaxoSmithKline (GSK). Corrêa and her group of 18 researchers have been developing new catalysts to replace conventional reagents since the program was first launched in 2016. One of the challenges for industry uptake of green chemistry is the need for production costs to be competitive with petroleum-based products. A case in point is anise seed oil, or anisole, which can be used in replacement of toluene (used in paints) and benzene (a known carcinogen), but is prohibitively priced.
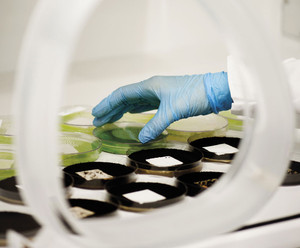
…and synthesis using microorganisms are two pathways to developing alternatives to petroleum-based productsLÉO RAMOS CHAVES
Even though prices are largely less than competitive, the market for renewable chemicals—including cane ethanol, which is used both as fuel and in the chemical industry—is expected to grow at an annual rate of 10.6% over the period 2015–2020. According to a study released in 2016 by US market research firm BCC Research, the market size of the green chemistry industry is expected to grow from US$51.7 billion in 2015 to US$85.6 billion in 2020. The study also found that regulations on the manufacture and disposal of conventional chemicals in the US and Europe are helping to boost renewable chemicals consumption and production. Navigant Research forecasts revenues in the sector to reach US$98 billion by 2020, equivalent to 1.85% of the US$5.3 trillion in total revenues projected for the broader chemical industry that year.
Challenges and education
While only just beginning to make its way into industry, green chemistry in Brazil has benefited from strategies to develop the sector that include greater involvement of research and education. Examples of this include initiatives implemented in recent years by the Brazilian Chemical Industry Association (ABIQUIM). “Since 2010 we have been helping to create Rede Brasileira de Química Verde [RBQV], a non-profit organization to promote science and innovation among local companies, as well as providing support to the Brazilian School of Green Chemistry at the Federal University of Rio de Janeiro [EBQV-UFRJ],” says Fernando Tibau, manager of Innovation and Regulatory Affairs at ABIQUIM.
EBQV is a virtual school with no research facilities of its own. Current research programs are largely focused on sugarcane bagasse studies involving researchers from UFRJ, the National Laboratory of Ethanol Science and Technology (CTBE) in Campinas, and the National Technology Institute (INT) in Rio de Janeiro. “Our primary interests are in researching ways to convert biomass waste into higher value-added raw materials,” explains EBQV coordinator Peter Seidl. Seidl believes a full-blown shift to green chemistry would not yet be practicable. “Processes still need to be developed, and technological constraints in industry need to be addressed.” He also believes a larger offering of graduate programs in green chemistry is needed in Brazil. A graduate program incorporating the subject is offered at UFRJ and there are plans to introduce the subject into undergraduate programs as well. Green chemistry has already been integrated into the undergraduate curriculum at UFSCAR and from 2018 will also be available in graduate programs.
Project
Green chemistry: Sustainable synthetic methods employing benign solvents, safer reagents, and bio-renewable feedstock (FAPESP-GSK) (No. 14/50249-8); Grant Mechanism Innovation Partnership Program; Principal Investigator Arlene Corrêa (UFSCAR); Investment R$3,948,414.14 (FAPESP) and R$2,849,094.73 + US$601,093.17 (GSK).
Scientific article
ERLEN Y. C. JORGE, E. Y. C. et al. Metal-exchanged magnetic β-zeolites: Valorization of lignocellulosic biomass-derived compounds to platform chemicals. Green Chemistry. v 19, p. 3856-68. jul 2017.