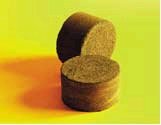
Tablets with 90% iron and 10% aluminum: used by industries to increase the mechanical resistance of aluminum alloyseduardo cesar
A change of position in the production line and the audacity to research and develop a product more adequate to the needs of the market, make up the two principal motives that have led Mextra, a small engineering firm specializing in the processing of metals, to achieve the position of leadership in the manufacture of tablets (pastilles) with metallic products used in the production of aluminum alloys. With its headquarters in the city of Diadema, in Greater Sao Paulo, the company should reach, during 2004, an income of US$ 6 million, practically the double of the previous year, with sixty (60) employees. Part of this income is coming from sales from markets abroad. “Approximately 30% of the production volume, estimated at 200 tons monthly, is sold to around twenty clients abroad. Although we have been active in the market for twenty six years, it has only been during the last six years that we have established the line for manufacturing tablets. We owe to it the company’s formidable growth”, says metallurgyengineer Ivan Calia Barchese, one of the partners at Mextra.
Tablets made from alloy elements – also called hardener tablets – are fundamental for the manufacture of the vast majority of aluminum products, like residential window frames, domestic utilities and even the wings of a plane. This interaction is important because aluminum is a material that is naturally malleable and to increase its mechanical resistance it is necessary to add in such alloying elements.
The most common are iron, copper, chromium, manganese and titanium. “Made by post-pressing or compacting, these tablets are similar to the effervescent vitamin C tablet but in a giant form (they measure 85 millimeters in diameter by 40 millimeters in height and weigh around 1 kilogram) which, when added to aluminum in its liquid state, dissolve and confer to it new mechanical properties”, explains the metallurgy engineer Lucio Salgado, a researcher and collaborator from the Nuclear and Energy Research Institute (Ipen) of the Ministry of Science and Technology (MST).
Innovation in tablets
In order to win market share and establish themselves as leaders in the segment, Mextra’s leap forward was to innovate the process of the manufacture of these tablets composed of two metallic elements. In the place of making a tablet from a mixture of the two distinct powders (for example, iron and aluminum, which is the most common in the market), the company invested in research and in the elaboration of a new process for obtaining a pre-alloy powder, which already has the two elements in its final structure. “From the fusion of scrap iron and aluminum, and using a process called atomization, we produce the tablets in the desired composition and we do not need to use powder bought on the market”, says Ivan Barchese. “We developed a product adequate from the environmental point of view, since we make use of recycled material, and have a production cost inferior to that sold on the market. Also, the tablets have higher quality, because the properties of the powder, as with the size and chemical composition of the grain, can be much better controlled, since its manufacture is done by us.”
The development of the pre-alloy powder with iron and aluminum was only possible with the financial support of FAPESP by way of the Small Business Innovation Research (PIPE) program. The work had the fundamental participation of the Technology Research Institute (IPT) of the State of São Paulo, which masters the technology of the process named atomization of metallic powders. “Atomization is a process similar to pulverization. The metallic alloy founded from iron and aluminum is pulverized and transformed into a powder, already at the desired composition”, stated the researcher Salgado, who was the PIPE project’s coordinator.
“Although the process of atomization has been known and dominated on a commercial scale since the 1940’s, up until today no company in the world has made an iron and aluminum alloy by this method”, related researcher Salgado. As a function of the unprecedented manufacture of the product at the world level, the Mextra tablets, in the proportion of 90% iron and 10% aluminum, and the process of their production resulted in patents deposited at the National Institute of Industrial Property (INPI) and as well in another two countries: the United States and Venezuela, where the principal clients of the company are located. Shortly, Mextra should be depositing patents in other countries.
“The first step in the process of the production of the tablets is the choice of scrap, which must be composed of iron with the minimal levels of carbon”, says researcher Salgado. Impurities of other metals are not desirable either, mainly copper, chromium, nickel and silicon. Once the selection is made, the scrap, whose ton is sold for around R$ 500, is founded in an induction oven (the heating is directly onto the metal and not on the sides of the oven) and heated until a temperature in the order of 1,700°C.
After the metal takes on its liquid form, it is run off into a large casting pan through which a liquid fillet with close to 12 millimeters of diameter is produced. With the use of a device called an atomizing nozzle, this fillet is bombarded with a high pressure water jet, leading to its pulverization and producing the powder. “The shock of the water on the fillet in its liquid state leads to the fragmentation of the metal”, says researcher Salgado. “In order to control the size and the morphology of the particles, the main parameters to be observed are pressure and the rate of flow of the water, the temperature of the liquid metal and the diameter of the fillet”, he adds.
In the opinion of engineer Barchese, the process of the manufacture of the metallic powder by atomization is practically concluded. “For now, the tablet of iron and aluminum is being placed on the market in small quantities. We estimate that already 20 tons of the product have been produced. At the moment we are adapting some stages of the production process to attend to the clients in a wider manner”, says engineer Barchese. Mextra has invested around R$ 2 million in setting up the industrial plant for the manufacture of the atomized powder. In the future, will have the capacity to produce 400 tons per month of tablets from recycled material. “Besides the innovative product, the process also is something new since all of the machinery was developed during the development of the PIPE project, which should be concluded in April of next year”, says engineer Barchese. “We believe that within two years our new pre-alloyed tablet will enter strongly onto the market.”
Clients abroad
Currently Mextra has in its portfolio clients from the main producers of aluminum in the country, such as the industrial companies Alcoa, Alcan, Companhia Brasileira de Alumínio (CBA), BHP Billiton and Valesul, a subsidiary of the Companhia Vale do Rio Doce. “For example, Alcoa only buys iron tablets produced by us. Among the various applications of the pressed powder that we sell to them is the production of fine aluminum sheeting for food containers, known as tetrapak. This is a very sophisticated material and the tablet employed must be of good quality, if not the aluminum lamina could have impurities and could split apart during the processing”, explains engineer Barchese. Abroad, Mextra sells its products to factories in the United States, Canada, Mexico, Spain, France, Colombia Venezuela, Argentina, Taiwan and countries in the Middle East. One contract recently signed with Alcan aiming exportation to Europe, forecast the delivery of metallic powders produced by atomization.
The partnership with the IPT for the development of atomized powders was the second signed between Mextra and the São Paulo research center. Before, in 2000, the company had already been involved with the Technology Support Program for Exporting (Progex), promoted jointly with the IPT, the Brazilian Service of Support to Micro and Small Businesses (Sebrae) of Sao Paulo and the Financier of Studies and Projects (Finep), of the Ministry of Science and Technology (MST). “On that occasion we had the intention to fight for the international market and we knew that we needed to have a product with quality and at a competitive price.
We got in touch with the IPT to help us perfect our tablets, which at that time were already being exported to a Venezuelan company. The partnership included the realization of studies on compacting the tablets without loss of efficiency. This meant that they could not be too hard, otherwise they would take a long time to dissolve in the liquid aluminum, nor could they be very fragile, as they would run the risk of crumbling during transportation”, explains engineer Barchese. The good results of this joint work served to kick off the research that targeted the development of the pre-alloyed tablets of iron and aluminum.
Mextra was founded in 1978 by the engineer Eduardo Barchese, Ivan’s father, who decided to put into practice his doctoral thesis, defended at the Polytechnic School of the University of Sao Paulo (Poli-USP) concerning the transformation of minerals into metal by way of a technique called “thermoaluminum” (obtaining high temperatures by way of the heat generated in chemical reactions between aluminum powder and metallic oxides). He mounted a small company focusing on the manufacture of metals and alloys directed to the foundry and steel making markets. Eduardo Barchese was also a professor at the Poli-USP and at the Faculty of Industrial engineering (FEI).
Special steels
Today the company is structured into three different sectors. The Chromium Division manufactures green chromium oxide, a product used as a raw material in the manufacture of special refractory bricks and as a green pigment in the ceramics industry. This same division is responsible for the manufacture of chromium metal, a metal that Mextra was a pioneer in manufacturing in Brazil, and chromium carbide, both used in the production of electrodes and special steels that demand higher metallurgical properties, such as resistance to mechanical abrasion and to corrosion. Another sector of the company is the Special Services Division that offers the services of milling, classification of metals and the development of metallic alloys in accordance with the client’s needs. This same sector deals with iron alloys, manganese in scales or powder form and aluminum alloys.
The third division is the tablets of alloying elements for aluminum. This product line, the leading light of the company, was baptized as Mextral. As well as the tablets of atomized iron powder and aluminum, the company offers to the market other four tablets, produced from mixtures of different metallic powders (chromium, manganese, copper and titanium). All of them, except the iron, have in their composition from 10% to 25% of aluminum powder and each one confers a different property to the aluminum. For example, the iron tablets increase the mechanical resistance of the material at high temperatures, whilst the chromium reduced corrosion under tension. The manganese and copper tablets raise the hardness of the aluminum, and it so happens that titanium improves the mechanical properties in general.
Mextra’s good commercial result, which possesses a quality system based on the ISO 9001:2000 certification, led to an expansion of the company, which should by the beginning of next year inaugurate a new factor in the town of Taubaté, in the region of the Paraíba Valley in the State of Sao Paulo. The building of the factory, budgeted at R$ 3 million, can count upon resources from the National Economic and Social Development Bank (BNDES). When it begins to operate, the Diadema installation will remain directed towards the manufacturing of pre-alloyed tablets of iron and aluminum. “We are optimistic about the company’s future. We manufacture a global product and we are certain that, with the investments that we have made over the last few years, we are more and more going to occupy a highlighted place in the international market”, said engineer Barchese.
The Project
Production of post-metals, pre-alloys by atomization for applications in the manufacture of tablets for addition of alloying elements in metallic aluminum baths (nº 01/03209-0); Modality Small Business Innovation Research (PIPE) Program; Coordinator Lucio Salgado – Ipen-Mextra; Investment R$ 373,600.00 (FAPESP)