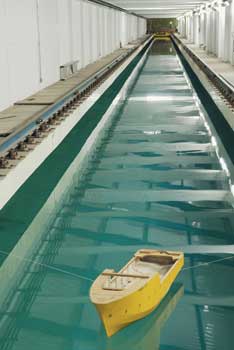
EDUARDO CESAR280-meter long tank produces waves and tests miniaturesEDUARDO CESAR
Prior to being built at the shipyard, the designs of large vessels, such as ships, are put through tests and trials at naval engineering laboratories. One of the main such labs in Brazil is part of IPT (the Technological Research Institute of São Paulo State) and has just undergone a renovation that transformed it into one of the most modern labs of its kind in the world. Inaugurated in 1956, when the country began to build large ships, and expanded in 1980, the IPT lab has a test tank that is 280 meters long, 6.6 meters wide and 4.5 meters deep. Wave-making equipment makes the tank resemble a miniature ocean. Small-scale mock-ups of model ships, up to 5 meters long, are sailed in the tank. A number of devices installed around the tank test and analyze navigation parameters such as speed, wave behavior and water resistance.
The new lab’s project started being outlined in 2005. Three main objectives were established: first, to create a multi-user center with 15 work stations for researchers, designers and IPT clients, so as to support integration among them in joint hydrodynamic R&D projects; second, to improve the technological training of the IPT Cnaval (its Oceanic and Naval Engineering Center), which houses the lab, by purchasing measurement equipment for trials in the testing tank, wind tunnel and cavitation tunnel for studies on propellers; and third, to reduce the time required to build physical models for testing.
R$9.5 million was invested in the renovation, 90% of which was provided by Petrobras, the lab’s biggest client; the balance of 10% was provided by Finep, the Studies and Projects Funding Agency. Of the total amount, roughly R$4 million went toward actual construction work, which included replacing the cover of the testing tank and renovating and expanding the Cnaval technical premises. The remainder was used to purchase equipment, such as a R$1.3 million robotic arm to make the miniature ships. The robotic arm was the main innovation in the renovation and solved one of the lab’s chief bottlenecks: the time it took to build a ship model to scale. “In the past, these models were handcrafted”, explains Carlos Daher Padovezi, Cnaval director. “They were drawn on paper and carpenters then made them from wood. Each model took 45 to 60 days to build. Now, the mock-ups are drawn by computer and the robotic arm sculpts them from polyurethane or Styrofoam blocks. Then their surfaces are coated with fiberglass resin. This entire process takes five to six days. As a result, we can conduct four times as many tests, and went from 20 to 80 tests a year.”
The other equipment purchased for the lab was the fast prototyping machine for the development of propeller and rudder models. It resembles a three-dimensional printer. The models are designed on the computer and then built by the machine, layer by layer, using a special resin. This system results in a level of detail that is hard to achieve with standard machining. Furthermore, production time has been slashed from 45 to 60 days to just 1 or 2 days.
Pressure on the propeller
The water or cavitation tunnel also benefited from a technological upgrade. Its structure underwent major renovation, which included disassembly and internal corrosion protection. Cavitation is the phenomenon whereby a liquid is vaporized as a result of reduced pressure brought about by the propeller’s movement. It can jeopardize the ship’s performance. “Cavitation is cause for great concern among designers because it can generate unwanted effects, such as lowering thrust (loss of propulsion power), blade erosion and increased vibrations induced by the propeller”, says Padovezi.
Besides the tunnel’s structural renovation, modern test equipment was acquired, such as dynamometers to measure propeller performance, cavitation visualization systems and hydrophones to measure underwater noise. The wind tunnel was not renovated, but equipment was purchased for it, the most important of which is the Particle Image Velocimetry (PIV) device, which works with laser beams and one or two cameras, depending on whether the measuring of the flow is two- or three-dimensional. “PIV measures the movement of any particle in the air or in the water using two simultaneous laser pulses, capturing the images with one or two special cameras”, Padovezi explains. “The equipment’s software can specify the local speed of the flow by comparing the particle images obtained with the emission of two pulses”. PIV equipment was also acquired for the testing tank and for the cavitation tunnel.
The renovation has made Cnaval capable of meeting the requirements of this fast-growth industry. “We can fulfill new requests more efficiently”, Padovezi says. “We currently have 10 research projects under way. Our clients include Petrobras, the Federal University of Pará, the São Paulo State Waterways Department, the Hermasa Navegação da Amazônia navigation company and the Brazilian Navy”. Several Brazilian shipyards are beginning to place their requests for tests. New clients are bound to materialize because of the shipbuilding industry’s growth. In 1979, the sector accounted for 45 thousand jobs; it almost came to a standstill in 1999, when most shipyards only repaired ships and employed a mere 2 thousand people. Today, however, the shipbuilding industry is experiencing a boom similar to the one in the late 1970s and it is expected to grow significantly.
Republish