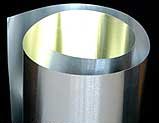
Eduardo CesarFiner and more resistant aluminum sheeting: raw material that has been innovatedEduardo Cesar
Aluminum metal plates that are thinner and more appropriate for sheeting and for the manufacture of automobile bodies, for example, are in the target of a wide ranging study that involves the Brazilian Aluminum Company (CBA), of the Votorantim Group, and the Polytechnic College of the University of São Paulo (Poly-USP). The study is based on the analysis of the microstructure of metal sheets of aluminum obtained through a process called Roll Caster, which carries out cold rolling, contrary to the more costly traditional process in which the sheets are hot rolled.
With the technological advance attained up until now this process has already managed to produce sheets of 2.5 millimeters of thickness, as against 6.0 millimeters in the recent past. “This means a gain in productivity and of competitiveness, because the roll of aluminum completes the process with a thickness that requires fewer stages during the rolling”, explains the metallurgical engineer, Ricardo do Carmo Fernandes, who is in the process of studying for his doctorate degree at the Poly.
“Our strategy is to maximize the technology of the Caster system, developing competence that will lead to the manufacture of products at lower cost and of better performance”, says the engineer Wilke Martins Parra, head of the sheeting department and of technological processes at the CBA.
“Through better knowledge of the process’s characteristics, we can, for example, expand on the range of products, improve their quality and raise their useful life .” Jorge Valezin, the general sales coordinator, adds that over the last two years the CBA has annually invested US$ 87 million in equipment, research and new processes, as well as expanding the production capacity, rising from 240,000 to 340,000 tons per year of primary aluminum.
Ideal texture
Up until now the studies carried out between the Poly and the CBA have already attained, in an unprecedented manner in Brazil, sheeting that can be used in the manufacture of light fittings and accessories for the mounting of aluminum screens. The study’s final objective, according to engineer Fernandes, is to obtain the ideal texture in thin sheeting for press stamping (molding by way of pressing), a process used, for example, in the production of automobile bodies. Engineer Fernandes is being guided by Professor Angelo Fernando Padilha, from the Metallurgical Engineering Department at the Poly-USP. The team is also made up of the student Juliana de Paula Martins, who is studying for her doctorate degree and Márcio Ferreira Hupalo, working on his post-doctorate thesis.
The Caster process that has been studied by the researchers makes use of liquid aluminum that, on passing through two metallic cylinders internally cooled by cold water, results in a sheet free of hot rolling as in the conventional process. This older style technique starts from a semi-finished material, aluminum founded from bauxite, the raw material for producing aluminum, which results in ingots with a thickness that varies between 23 and 60 centimeters (cm). Afterwards, the sheets are formed at a temperature that reaches 500 °C.
The Caster system eliminates this last stage of the production line, leaving the infrastructure much thinner, with less investment of capital. Hot rolling demands an investment of US$ 150 million, while continuous rolling can be mounted for US$ 40 million US$ 10 million for the Caster system and US$ 30 million for the cold laminator. And, to top it all, the Caster system eliminates the need for an installation, some 200 meters in length, to house the hot laminator, without speaking of the work force costs, electrical energy consumption and maintenance.
From the optical operational point of view, the Caster system is more versatile, or that is to say, in the case of the production of various alloys, it facilitates the adjustment of the chemical composition of the metals and produces a diversified line of products, with greater widths.
Width is an important factor for various motives: initially the average width of an aluminum sheet was 85 cm, but today the market demands 1.8 meters. This dimension guarantees greater productivity in applications, explains Ayrton Filleti, the coordinator of the Automobile Industry Market Committee, of the Brazilian Aluminum Association (Abal). In the opinion of Filleti, as it demands 20% less investment in production infrastructure and brings about a reduction of close to 30% in operational costs, the Caster system already represents half of the installed capacity of rolling in the aluminum industry of Latin America, with 35 machines in operation.
Without distortion
“Products that previously suffered from a high degree of distortion during their processing are today obtained in the dimensions close to the final desired thicknesses, with an adequate microstructure.” And it is this characteristic that is going to determine if laminated plates can be submitted to more severe conditions without suffering distortions that will compromise them.
Nevertheless, the Caster process still has significant bottlenecks in relation to hot lamination. One of them is the reduced scale of production annually 10,000 tons per machine, as well as problems in the cooling of the equipment, which leads to low resistance of the material when submitted to deep pressing, as is demanded for example in the automobile industry that is making use of aluminum in greater and greater quantitiesIt is exactly the deficiencies in the Caster process that Fernandes and Professor Padilha’s team are studying in the Poly laboratories.
Today, for example, it is known that factors such as the temperatures involved in the various phases of the process and the velocity of withdrawal (the transport of material to another receiver in the production) have an impact on the texture of the sheet laminated by the Caster process. “With the variation of speed and temperature during withdrawal, we are going to obtain different characteristics in the microstructure of the sheets”, engineer Fernandes explained.
The CBA, which has an income of some US$ 700 million per year 50% going to exports, has been researching the Caster process for more than ten years and by of this technological route has produced fine sheeting with thicknesses below one millimeter, destined to products that do not demand deep pressing, such as the material used in the production of hot food packaging containers.
The intention of the company is to migrate almost all of its production to this process, including laminates for application in heat exchangers (radiators, air conditioners), packaging for the food industry, transport material etc., contributing towards increasing the participation and consumption of aluminum in the domestic market. This is a market that is still small with an annual consumption per capita of aluminum in the order of 4 kilograms per inhabitant as against 29 kilograms in the United States. This is a difference that could be decreased with the adoption of finer sheets of aluminum.
Republish