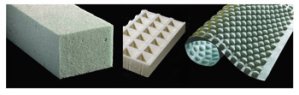
Bio-material in various compositions: biodegradable foam, trays for seeds, absorbent oil carpetEDUARDO CESAR
Resins obtained from plants such as corn, rice, sugarcane, soybeans and the castor bean serve as the basis of biodegradable products destined to substitute expanded polystyrene (EPS), a product difficult to recycle derived from petroleum, mainly used for the packaging industry. Bioespuma, the commercial and patented name of the material developed by the company Kehl, in the city of São Carlos, in the state of São Paulo has been applied in various products such as trays for the commercialization of fruit and vegetables, packaging for electro-electronic products, supports for the planting of offshoots and seeds with associated nutrients and carpets absorbent to chemical products.
“The formation and the arrangement of the molecules allows for obtaining different products”, says Eduardo Murgel Kehl, a chemist and economist who started the company in 1972 as a test laboratory and manufacturer of rubber and silicon articles. Some product lines are already on the market, others will be launched during the first semester of this year by the company Synbeeosis, also from São Carlos, which has become Kehl’s commercial partner. The research that resulted in the biodegradable material began back in 1992 in the Kehl laboratories and continues at the State University of Campinas (Unicamp), where the first study of the biodegradable material was carried out. Other tests were made at the Federal University of Sao Carlos (UFSCar) and at the University of São Paulo (USP) in the same town.
The major advantage of the bio-material is its degradation time in nature. In the presence of oxygen and in the soil, it degrades within two years – without oxygen it can take up to three years. “In environments such as rubbish tips, appropriate to the development of microorganisms, the process is much quicker and can be completed in up to six months”, says the chemist Ricardo Vicino, one of the company’s partners, who coordinated the research at the university. The Kehl company has a signed agreement with Unicamp that allows for the carrying out of tests on the developing product. Bioespuma is produced by the combination of the biomass of vegetal resins and petroleum derivatives, which constitute up to 50% of the composition. The mixture is treated by conventional chemical processes and transformed into a raw material that gives rise to the biodegradable material.
The tests to evaluate the product’s biodegradable level were done at the UNICAMP laboratory of the Pluridisciplinary Research Center in Chemistry, Biology and Agriculture (CPQBA in the Portuguese acronym), according to the norms of the American Society for Testing and Materials, accepted worldwide. Bioespuma could substitute Styrofoam, which is not biodegradable and constitutes a serious environmental problem when discarded in rubbish dumps. Furthermore, it produces toxic gases on being incinerated. Recycling of Styrofoam is possible, but the material’s low density constitutes an obstacle to its reuse. In order to be economically viable, a very large quantity of the material would need to be collected. At the moment the initiatives to contain the ESP discarding in the rubbish tips or even in nature are timid.
Initially the Bioespuma was produced from the castor bean, but today the soybean and corn are two of the main raw materials for obtaining better technical results and at a lower cost. One of the products derived from this vegetable polymer that has conquered consumers is a special paint based on corn used in civil construction work as an impermeable coating for concrete slabs, as well as industrial, commercial and residential flooring. “As well as having no smell during its application, the product is highly resistant”, explains Kehl. The paint, produced in various colors, is even indicated for road signs and naval construction, as a waterproof coving for ships’ hulls.
The vegetable polymer, also called polyurethane, is used in the manufacture of hammer ends, which have an appearance similar to that of rubber, indicated for impact applications, but without causing damage and marks on the impacted parts, as in the car manufacturing line. “Two BMW repair garages are making use of our hammers”, says Kehl. When the ends get worn down, they can be substituted since they screw into position on an aluminum support.
Resistant packaging
The polymer’s versatility has led various entrepreneurial groups to propose partnerships with researcher Kehl and has attracted clients from diverse areas. The company Rytpak, from São Paulo, for example, is purchasing an unfinished product in order to produce packaging for various segments of the industry. As it is biodegradable, it is interesting multinational companies that are looking to substitute their EPS packaging, rejected by various European countries because of the waste.
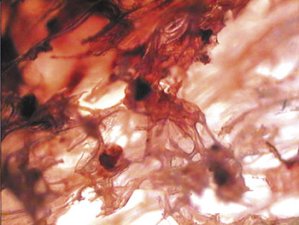
Microscope shows the micro-organism action during various phases in the decomposition of Bioespumakehl
Caterpillar, the manufacturer of machines such as bulldozers, conveyor belt tractors and generators, are using carpets made from Bioespuma to absorb the lubricating oil in their dealers’ maintenance workshops. The product even functions as a barrier for oil spills in rivers and seas. The oil is absorbed by the foam, which does not sink even when highly soaked. In order to remove the oil, it is sufficient to pass the foam through a machine similar a compressor and it immediately returns to its original shape and can be used again.
Some companies are seeking out Kehl in search of specific solutions. One of these clients, a Japanese group in the food sector, which because of the confidentiality clause in the agreement cannot be identified, want a natural foam that can be placed in the effluent treatment system inside tanks with a capacity to process 10,000 m3. “We’re developing a natural and renewable foam, but not biodegradable, if that were the case it would be consumed by the micro-organisms during the effluent treatment, which is being tested on a pilot scale”, says Vicino. With this device, the effluent treatment capacity of the company will practically double without the need to build a new tank or to invest in works to increase the industrial plant.
Rose gardens
A flower producer from the town of Holambra, in the interior of the state of São Paulo, for example, has placed an order for Bioespuma pots for his rose gardens. As the substrate is biodegradable the offshoots can be directly transplanted to the flower beds. The small pots for the plants’ offshoots have in their chemical composition nitrogen, phosphate and potassium (NPK), the basic formula of manure, as well as micronutrients. As the foam degrades into the soil, it liberates the nutrients to the plants. The product is now ready, but the order, of 5,000 small pots, can only be delivered when the company Synbeeosis has its industrial greenhouse ready.
Another Holambra producer wants 80,000 vases per month to substitute those of plastic. In this case the Bioespuma is gaining another configuration by having a useful lifespan of around ten years. The Kehl company has already produced prototypes to be used in hydroponic cultivation and in flower arrangements, substituting synthetic foam, which will also be manufactured by the partner company. The decision to pass on the production of bio-material to another company was taken because Kehl is already manufacturing various products.
In the area of industrial rubbers it is producing shock absorbers, coatings, flooring and wheels, as well as cannulas for veterinary use, made from non-toxic rubber, and a product line made with silicon. “After years investing in research into new products, we decided to center our efforts on putting them on the market”, says researcher Kehl.
The company Synbeeosis is ready to meet the demand. Initially it is going to produce blankets for oil absorption in mechanic workshops and in industries, as well as the pots for agriculture. For the civil construction industry, Nutrispuma boarding is ready, another name of the bio-material for specific applications, substituting the plastics used as molds for concrete, for example.
The company is also preparing to compete in a new niche, the market of pet animal products. Carpets for absorbing the urine of cats and dogs, which degrade rapidly when thrown in the rubbish, and biodegradable plastic sacks for collecting feces are the first launches programmed in this area.
Republish