At Brazilian mining giant Vale’s Brucutu mine in Minas Gerais, southeastern Brazil, a fleet of giant yellow trucks will be seen lazily crawling up and down the mine’s slopes. With a payload of 240 metric tons per trip, the mining mammoths carry iron ore from within the mine pit to a discharge area for processing. All 13 Caterpillar trucks in the fleet are fully driverless vehicles operated from control rooms using special software, GPS systems, radar, and artificial intelligence (IA).
The result of six years of research and testing, the project, which began being implemented in the second half of 2018, has made Brucutu the first mine in Brazil to use driverless vehicles, a technology that has increased operational safety. The trucks are equipped with collision avoidance sensors that will stop the vehicle when they detect objects or people in their path, until the way has been cleared. Having no operators in the cab reduces the number of workers exposed to high-risk areas, such as excavation and loading sites. The new technology also provides cost savings. “We estimate fuel burn and maintenance costs have been reduced by 10%, and equipment life has been lengthened by 15%,” says Hélio Mosquim, who heads the information technology innovation department at Vale.
The company’s driverless trucks, say experts, are just one example of how digital technology can increase safety and productivity in mining operations, which involve hazards such as blasting, rockfalls, vibration, high noise levels, heavy hauling, and the use of toxic materials. Other technologies being explored by mining companies include remote blasting systems, online control of vehicle and pedestrian movement, drones for geophysical surveys, sensors combined with video analytics software for dam monitoring, and AI platforms that analyze ore grades in real time.
Future mines will have no workers in high-risk areas, says Giorgio de Tomi, of USP
“Mining is an inherently hazardous activity, but we need ore to produce many of the products we consume. Many of these hazards can be avoided by automating as much of the operation as possible,” says mining engineer Giorgio de Tomi, head of the Research Center for Responsible Mining at the University of São Paulo (NAP.Mineração-USP). Tomorrow’s mines, says de Tomi, will be fully autonomous, keeping workers a safe distance from high-risk areas. And they will intensively leverage artificial intelligence, machine learning, and data analytics to improve productivity and enable more sustainable and economical ways to access increasingly scarce mineral resources buried deep underground.
One of the largest high-tech mining projects in the world is being developed by mining company Luossavaara-Kiirunavaara Aktiebolag (LKAB) in Sweden, a country known for its cutting-edge mining technology. The company expects that by 2030 it will be able to access iron ore reserves at a depth of almost 2 kilometers (km) at its Kiruna and Malmberget mines. After more than 100 years of mining, the uppermost orebodies in the two reserves are nearing depletion.
To enable mining at such extreme depths, a multinational consortium formed by ABB, Epiroc, Combitech, and Volvo Group is developing carbon-free, fully electric, autonomous technology for drilling, mining, and transporting ore at a depth where connectivity is prevented by interference with communication signals caused by blasting and tremors.
In Brazil, Vale, the country’s largest mining company and one of the leading players globally, signed a R$21-million contract in 2019 with telecom company Vivo to implement a Long-Term Evolution (LTE/4G) network for data transmission at all its operations in Brazil. The Carajás mine in Pará is expected to have connectivity within the first half of 2020. Mosquim says the new system will support deployment of autonomous drilling rigs and vehicles. A total of 37 autonomous trucks are expected to be operating at Carajás by 2024.
Initiated in 2016, Vale’s digital transformation process gained further traction in 2018 when the company launched a program that will invest a total of US$467 million by 2023 in industry 4.0 technology. An Integrated Operation Center has been implemented in Nova Lima, Minas Gerais, to seamlessly connect the end-to-end supply chain and different business functions using digital technologies.
Before, each business unit operated independently, Mosquim explains. Today, algorithms analyze demand and then modulate production and ore shipments to deliver the right ore grades for each steelworks’ production process, increasing the value of the company’s product. The initiative is estimated to generate US$600 million in added revenues.
In early 2019, Vale created an Artificial Intelligence Center in Vitória, Espírito Santo, to develop new solutions for industry applications. One of its pioneering projects is optimizing the process for producing pellets—small iron ore globules used in steelmaking. Data analytics combined with AI is being used to optimally balance the ratio of coal and natural gas in the pelletizing process, generating savings of 7% on these inputs.
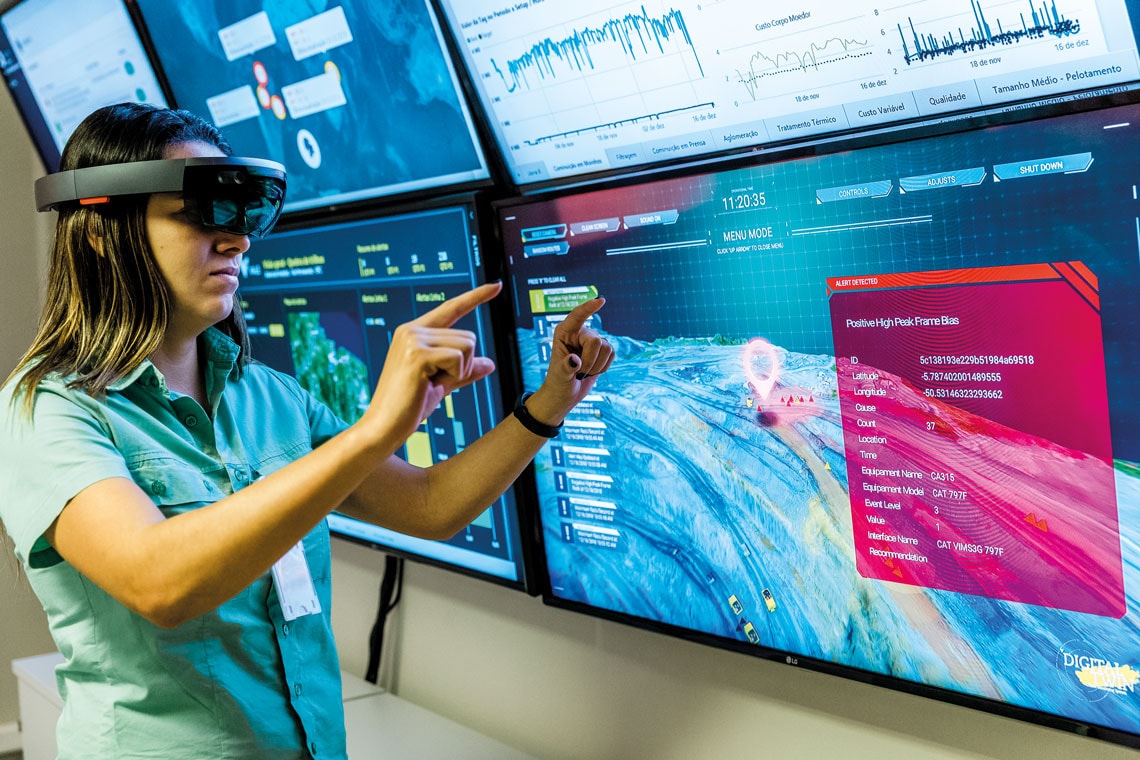
An Artificial Intelligence Center at Vale: new technology is helping to optimize mineral reservesRicardo Teles / Vale
Dam monitoring
The Brumadinho dam failure on January 25, 2019, a tragedy that left 249 dead and a trail of devastation in Brazil’s southeastern state of Minas Gerais, compelled Vale to redesign its approach to dam management. The company created a Geotechnical Monitoring Center in the state to monitor its 111 at-risk dam structures in real time. The center uses a combination of sensors, video analytics software, and algorithms to analyze data, predict problems and alert its full-time monitoring teams.
Vale has also invested in a dry processing technology that eliminates the need for dams to store mine tailings. By 2023, a total of 70% of its beneficiation operations will use dry processing, making Vale the first mining company to use the technology—which was developed by its recent acquisition, NewSteel—at industrial scale. Dry processing will enable tailings to be stored in safer dry-stack facilities.
The failure of Brumadinho and Fundão—a dam operated by Samarco in Mariana, Minas Gerais, which was breached in 2015, causing 19 deaths and contamination in the Rio Doce—also created the need for systematic monitoring of the volume and properties of tailings remaining at the dam sites and the material discharged downstream into affected rivers. The monitoring programs at Brumadinho, Mariana, and along affected rivers are intended to prevent further damage and provide inputs into environmental remediation plans. Monitoring is done by field technicians using drones built by São Paulo–based startup XMobots (see Pesquisa FAPESP issue no. 211).
With support from FAPESP’s Research for Innovation in Small Businesses program (RISB, or PIPE in the Portuguese acronym), XMobots developed the only Brazilian-built drone to be certified by the civil aviation authority, ANAC, to fly at altitudes exceeding 120 meters, beyond visual line of sight (BVLOS), over distances of up to 30 km. Giovani Amianti, a founding partner at XMobots, explains that the company’s drones can operate autonomously over great distances using GPS systems and sensors, unlike conventional drones operated from the ground using a remote control, which have a limited range.
Xmobots drones have a high accuracy (HA) system with a margin of error of just 3 centimeters (cm), compared to 8 cm with conventional GPS systems. “Another advantage over GPS is that HA technology does not require ground markers to collect coordinates, which can be a difficult task on unstable terrain, such as mud,” says Amianti.
Nexa Resources, a Votorantim Group mining company producing copper, zinc, lead, silver, and gold, also uses autonomous drones equipped with electromagnetic sensors developed jointly with Peruvian startup Deep Sounding. The drones are used for geophysical surveys of the company’s open-pit mines in Peru. Rodrigo Alberto Moreira Gomes, head of innovation and energy at Nexa, says the drones are programmed to fly at an altitude of 30 m above the ground, tracing the terrain and scanning the subsoil for regions likely to contain minerals, a task previously performed by helicopters or airplanes. “Drones are not only more economical, but because they fly closer to the ground, the data they collect is more precise.”
Ventilation and bauxite
Nexa has been developing digital mining solutions since 2011, spending an average of US$9 million annually, the equivalent of 0.36% of its net revenue in 2018. Among the projects successfully completed by the company’s research and development department is an on-demand ventilation system installed in an underground zinc and lead mine in Vazante, Minas Gerais. Conventional ventilation systems operate continuously, whereas the new technology modulates the system depending on the number of people and machinery in the mine at a given time, reducing energy costs.
“The system is currently pre-programmed, but we are working to create sensors to throttle the ventilation,” says Gomes. Another of the company’s innovations is a software-based blasting system that eliminates the need for blasters to light fuses and run to safety. The system is being tested at a mine in Morro Agudo, Minas Gerais.
Both of the newly developed systems will be used at Aripuanã, an underground mine project in Mato Grosso that will produce an estimated 66,700 metric tons of zinc, 23,000 metric tons of lead, and 3,700 metric tons of copper per year from 2021. Marco Henrique Carrete, head of automation at Nexa, says that mine operations and equipment routing at Aripuanã will be managed by a digital dispatch system, using telemetry data to identify, track, and optimally route the mine equipment to save fuel. A tracking system will be used to prevent rollovers and collisions.
New solutions have also been introduced in bauxite mines. In Miraí, Minas Gerais, Companhia Brasileira de Alumínio (CBA) uses an automation system powered by artificial intelligence to manage a water treatment system at its beneficiation plant. Plant manager Christian Fonseca de Andrade explains that the system treats water coming from the tailings dam before it is discharged into the environment, ensuring that water quality parameters are better than required by environmental regulations. The automation system, designed by Bauminas Ambiental, in Campinas, São Paulo, measures flow rate, power of hydrogen (pH), and turbidity in real time as the water flows in and out of the treatment plant, and dispenses chemical reagents as required for treatment, a task that would otherwise require four people. “Automation has not only improved water quality, but it has also reduced chemical usage by 80%,” says Andrade.
Created two years ago, Brazil’s Mining Hub is developing innovative solutions for the mining industry
In 2018 a group of 25 mining companies and other industry players, with backing from the Brazilian Mining Institute (IBRAM), launched Mining Hub, a virtual collaboration network now in its third round of startup challenges. In each round, startups are invited to develop solutions in areas such as renewable energy, water and waste management, operational excellence, safety, and social development. A total of 20 projects are currently in testing, says Rodrigo Gomes, a coordinator at the hub and energy innovation manager at Nexa.
One project, developed by startup LLK for Vale, is creating technology to collect and process imaging information across the electromagnetic spectrum. This allows sensors to determine ore grades as the material passes by on conveyor belts, without requiring laboratory analysis. “As a result, the products we sell are better optimized,” says Hélio Mosquim, head of information technology innovation at Vale. The new system is currently undergoing testing.
Collaborations with mining companies have also helped to boost innovation at universities. A partnership between Vale, the Federal University of Espírito Santo, and the Espírito Santo Research Foundation has provided an opportunity for 30 students to participate in an immersive program at the company. Two student-led projects are being developed at the Artificial Intelligence Center in Vitória, one for predicting and preventing locomotive engine failure and the other for detecting bottlenecks along the Vitória-Minas Railroad. In São Paulo, a project at the Research Center for Responsible Mining at the University of São Paulo (NAP.Mineração-USP), dubbed the “Future of Mining,” is creating digital transformation applications such as decision support for mine operations, in a collaboration between Vale and FAPESP.
Giorgio de Tomi, a director at NAP.Mineração, says there have now been several offshoots from the project, including an MBA Program in data science for engineers at the Polytechnical School at USP, which will accept its first class this year, and a startup, Dual Mining, founded by mining engineers Ranyere Sousa Silva and Erbertt Barros Bezerra. The duo created an artificial intelligence and machine-learning system for online analysis of equipment and fleet productivity in mining operations.
Another spinoff is a FAPESP-supported project developing digital transformation and simulation solutions for small businesses. “Brazil’s mining majors are at the same stage of technological maturity as their global peers. But small and medium-sized companies are far behind and will be unable to achieve transformations without support,” says Giorgio de Tomi. According to data from IBRAM, there are currently 9,400 active mines in Brazil, operated by 7,638 companies. Of these, 87% are classified as micro businesses and 11% as small or medium-sized businesses.
Projects
1. AMAS6: Multispectral imaging system for unmanned aerial vehicles (UAVs) (no. 16/01011-4); Grant Mechanism Research for Innovation in Small Businesses (RISB); Principal Investigator Michelle Matos Horta Tenca (XMobots); Investment R$142,136.15.
2. Dynamic simulation of the mineral value chain (no. 16/00647-2); Grant Mechanism Regular Research Grant; Principal Investigator Giorgio Francesco Cesare de Tomi (USP); Investment R$49,980.78.
3. Certifiable avionics system for civilian unmanned aerial vehicles (UAVs) (no. 13/50946-8); Grant Mechanism Research for Innovation in Small Businesses (RISB); Cooperation ArrangementFINEP; Principal Investigator Giovani Amianti (XMobots); Investment R$876,283.32.
4. Certifiable avionics system for civilian unmanned aerial vehicles (UAVs) (no. 07/55661-0); Grant Mechanism Research for Innovation in Small Businesses (RISB); Principal InvestigatorMichelle Matos Horta Tenca (XMobots); Investment R$ 991,761.06.
5. Asset optimization applied to open-pit mining (no. 10/51287-0); Grant Mechanism Research Partnership for Technological Innovation Program (PITE); Principal InvestigatorGiorgio Francesco Cesare de Tomi (USP); Investment R$80,487.76.