
MIGUEL BOYAYANSoldaduras con láser: la luz pasa por la lente y alcanza el conector encerrado en su protecciónMIGUEL BOYAYAN
En octubre del año pasado, la industria Tupy Fundições, del estado de Santa Catarina, una de las mayores del segmento en Brasil, enfrentaba un gran desafío. Para ejecutar un contrato millonario de provisión de autopartes para la ensambladora General Motors, en Estados Unidos, la empresa brasileña necesitaba probar que era capaz de realizar fracturas inducidas por láser en estructuras de motores de automóviles como las tapas de cojinetes. En el interior de esas estructuras va montado el cigüeñal, eje que recibe la fuerza térmica de la explosión enviada por los pistones y transmite esa energía en forma de fuerza mecánica para las demás piezas del motor.
Como no dominaba el proceso del láser, la empresa, radicada en la localidad de Joinville, procuró a los ingenieros del Instituto de Estudios Avanzados (IEAv) del Comando General de Tecnología Aeroespacial (CTA), ubicado en la ciudad de São José dos Campos, en el interior paulista. Poco después de un mes, los especialistas demostraron la viabilidad de realizar micro-ranuras láser guiadas mediante fibra óptica en el bloque de hierro que puede ser fracturado, con seguridad y precisión, por medio de una fuerte presión ejercida por una cuña hidráulica en el montaje de los motores.
“El proceso láser separó, en un cuerpo de prueba, la tapa de cojinete del bloque del motor en una única operación, reduciendo el número de operaciones de remociones de material y los costos de fabricación”, afirma José Cláudio Macedo, director de operaciones de la Tupy. Con ello, la empresa probó la viabilidad del contrato y comenzará a proveer, a partir del 2009, 60 mil bloques por año para la montadora americana. El éxito de la operación fue posible porque, además del alto conocimiento de los investigadores del IEAv acerca de la tecnología láser y sus aplicaciones industriales, el instituto adquirió en 2006 una nueva estación de procesamiento de materiales mediante láser de fibra óptica de alta potencia. “Se trata de un equipamiento con propiedades superiores que las de los láser empleados tradicionalmente en los procesos industriales, como los de dióxido de carbono (CO2) y de neodimio-YAG (Nd:YAG) (ver cuadro en la página 77). Aquellos resultaron muy útiles en ese proyecto y cuentan con una amplia aplicación en operaciones de corte, soldadura y tratamientos térmicos de materiales”, dice el físico Rudimar Riva, jefe del Laboratorio Multiusuario para Desarrollo de Aplicaciones de Láser y Óptica (Dedalo) del IEAv. “La instalación del equipamiento, único en América Latina, contribuye para el desarrollo de nuevos procesos de fabricación, aumentando el valor agregado de los productos nacionales y permitiendo la calificación de recursos humanos en el área de procesamiento de láser”, dice Riva.
Para la Tupy, el equipamiento surgió en el momento exacto. “Si no hubiésemos conseguido desarrollar este proceso, deberíamos adquirirlo a las empresas alemanas, las únicas que dominan esta tecnología. Decidimos desarrollarlo en Brasil, en colaboración con el IEAv, y ahora realizaremos un estudio de viabilidad económica para implantarlo en nuestra fábrica”, dice Macedo. Todo el equipamiento montado, de los láseres producidos y guiados mediante fibra óptica tiene un costo cercano a los 500 mil dólares.
La primera diferencia en el equipamiento es la calidad del haz emitido, que posibilita un diámetro focal (área iluminada por el haz) menor, elevando la intensidad de la luz. “El aumento de la intensidad permite cortar o soldar materiales más gruesos con mayor rapidez y calidad. Como el diámetro focal es menor, se registra menor pérdida de material durante el corte”, explica Riva. Otra característica importante de esos láseres es la mayor conversión de energía eléctrica en energía lumínica. Por cada kilowatt de potencia consumido por la estación, es posible extraer 250 watts de potencia lumínica, mientras que los láseres de Nd:YAG convierten apenas 50 watts y los de CO2, como máximo, 200 vatios. La mejor eficiencia energética muestra su reflejo positivo en la reducción del costo operacional.
“Esas tres características juntas – calidad superior del haz, mejor eficiencia energética y reducción del costo de mantenimiento – tornan a los láser de fibra de alta potencia, extremadamente atractivos para aplicaciones en fábricas”, dice el físico Milton Sérgio Fernandes de Lima, investigador de Dedalo, responsable por varios proyectos que atañen al equipamiento. “Los industriales han percibido esa ventajas y los láser de fibra están sustituyendo a los aparatos tradicionales, principalmente a los Nd:YAG”.
Soldadura en Embraer
La instalación de la estación de tratamiento en Dedalo costó alrededor de 500 mil dólares, y la mayor parte de esa erogación (400 mil), fue provista por la Financiadora de Estudios y Proyectos (Finep), del Ministerio de Ciencia y Tecnología (MCT), y del Fondo sectorial Aeronáutico. El resto provino de las cajas del IEAv y del Instituto Fábrica del Milenio (IFM), red virtual de investigación enfocada en la industria de la manufactura de la cual el instituto forma parte (lea acerca del IFM en la edición nº 133 de Pesquisa FAPESP). La financiación fue utilizada para la adquisición del equipo de láser a fibra óptica y demás componentes del sistema, además de la implantación de una cabina metálica a prueba de derrames con 4 metros de longitud por 4 de ancho y 3 de altura, que permite el ingreso de piezas de hasta 2 metros de ancho. El fabricante nacional de aviones Embraer también colabora con el proyecto, en la provisión de material y recursos humanos, y está siendo uno de los grandes beneficiados con las investigaciones realizadas con el equipamiento.
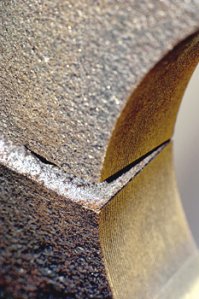
MIGUEL BOYAYANPotencia del láser: la estructura de un motor fracturada y micro poros en una pieza automotriz.MIGUEL BOYAYAN
El interés de la Embraer en el laboratorio se explica fácilmente. “Hoy en día, la tecnología de soldadura láser se emplea cada vez más en la fabricación de aeronaves, principalmente en la parte estructural, en sustitución del proceso de remachado”, dice Lima. Ese proceso utiliza los remaches, que son pequeñas piezas cilíndricas metálicas semejantes a tornillos, para unir dos placas metálicas. Un jet comercial de gran porte, como un Boeing 777, con capacidad para más de 300 pasajeros, posee alrededor de 1,5 millones de remaches que aumentan en el 15% el peso de su estructura, sumado a que el proceso de remachado consume el 15% del tiempo de fabricación de la aeronave. Además de eso, para realizar el remachado es preciso perforar el fuselaje, generando una especie de vulnerabilidad en el jet. “Como el avión opera bajo temperaturas extremas, de -50 ºC a 50 ºC, el fuselaje puede sufrir corrosión en función del acumulamiento de hielo y agua en esas cavidades”, explica Lima. “Boeing, Airbus y Bombardier poseen acuerdos de cooperación con centros de investigación en láser y las dos primeras ya emplean esa tecnología en la fabricación de sus aviones”.
El IEAv posee dos proyectos en etapa de desarrollo con la Embraer. El principal de ellos es la soldadura de uniones de aluminio de alta resistencia, que son utilizadas en la estructura de las aeronaves. “Ensayamos un centenar de cuerpos de prueba de aluminio soldados con láser a fibra, que ahora están testeándose en la Embraer. Los resultados preliminares demuestran que el equipamiento produce soldaduras con excelente calidad metalúrgica y muy pocos detalles”, afirma Riva. El proyecto utiliza el láser Nd:YAG y posee como objetivo la soldadura sin utilización de plomo en los contactos eléctricos de fijación utilizado en los aviones. Ese proyecto es vital para Embraer porque varios países prohibieron en junio del año pasado, el ingreso de componentes eléctricos y electrónicos que contengan plomo y otras sustancias tóxicas o difíciles de reciclar. “Para solucionarlo momentáneamente, desarrollamos una tecnología que utiliza el láser de Nd:YAG como fuente de calor para soldadura sin plomo”, explica el investigador. “Los resultados muestran hasta ahora que los contactos soldados en apenas algunos segundos presentan altísima resistencia a la fractura, nada comparables con los contactos crimpados (conectores para terminales de cables), realizados por medio de un alicate especial”.
Centro de tecnología de avanzada
Instalado al borde de la carretera de los Tamoios, que une el Valle de Paraíba con el litoral norte paulista, el laboratorio del IEAv, creado hace sólo tres años, también preparando otros dos modelos de láser, ambos proyectados y construidos en el instituto: un láser de CO2 pulsado de alta potencia y uno de vapor de cobre, además de otros cinco láser de uso más común, tres de Nd:YAG y dos de CO2 continuos. Los equipamientos sirven para varios proyectos en el área de manufacturas. Ese es el caso de un nuevo tratamiento láser para herramientas de fabricación, que se originó en una necesidad industrial prevista dentro de la red del IFM y devino en el depósito de una patente al IEAv. “Se trata de un proceso innovador de texturización láser que aumenta el tiempo de vida útil de las brocas, fresas y otras herramientas de fabricación”, destaca el ingeniero João Fernando Gomes de Oliveira, coordinador general del IFM.
Durante el proceso, un haz de luz láser de pulsos cortos y alta energía promueve la formación de nanocráteres en la superficie de la herramienta. Como ellas normalmente son recubiertas con un revestimiento en base a nitratos y carbonatos, el proceso permite una mayor adherencia de los revestimientos que quedan adheridos en los surcos. Una capa más adherente confiere mayor durabilidad a las herramientas – en algunos casos, la vida útil fue aumentada en diez veces. El proyecto utiliza el láser de vapor de cobre y fue desarrollado por el Dedalo en colaboración con la Universidad Federal de Uberlândia y la Universidad Estadual de Campinas. Abarca también un pool de empresas interesadas en la tecnología, formado por la Tupy Fundiciones, Sandvik (especializada en la fabricación de herramientas), Brasimet y Balzers (focalizadas en revestimientos y tratamientos de superficies).
Otro proyecto relevante en el área de la metalurgia implica a la compañía Thyssen Krupp Metalúrgica Campo Limpo, brazo paulista de un grupo multinacional que detenta el liderazgo mundial en la fabricación de cigüeñales, ejes metálicos de los motores automotrices. El objetivo del proyecto es realizar la microtexturización láser en esos componentes para reducir la fricción entre las piezas con el consiguiente desgaste. “Pueden utilizarse diversos métodos para realizar la microtexturización, tales como abrasión controlada, cañón de electrones o corrosión química. La texturización con láser es una técnica reciente que ha presentado buenos resultados”, dice Lima.
Fibras y cristales
Para entender como funciona un láser, y las diferencias entre ellos, es preciso conocer que la generación de un haz de luz se da, normalmente, por la excitación de los átomos o moléculas de un determinado medio activo, compuesto por una o varias sustancias responsables por la emisión de radiación láser, por una fuente luminosa o una descarga eléctrica. Los láseres de dióxido de carbono (CO2), por ejemplo, son excitados por descargas eléctricas y poseen como medio activo una mezcla de gases: nitrógeno, helio y el CO2, responsable de la emisión del láser. En los láseres de Nd:YAG, el medio activo es una barra de cristal de YAG, un cristal sintético constituido por óxido de ítrio y de aluminio, dopado (inserción de pequeñas cantidades de elementos químicos en una sustancia) con neodimio y excitado por una fuente luminosa de una lámpara o de diodos emisores de láser, dispositivos similares y más potentes que los utilizados en reproductores de CD y DVDs.
El láser de fibra óptica posee como medio activo una fibra de sílica dopada con iterbio, un elemento del grupo de los metales raros. Más de un centenar de diodos emisores de láser son utilizados como fuente de excitación de la fibra.
Republicar