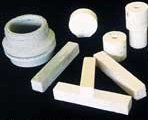
eduardo cesarRefractarios: cuerpos de prueba construidos en el laboratorio de la UFSCareduardo cesar
Una asociación entre la Universidad Federal de São Carlos (UFSCar) y Alcoa Alumínio resultó en la creación de un instrumento inédito: el reómetro para cementos. Dicho equipo se destina al registro del grado de calidad y de las reacciones entre las materias primas utilizadas en las fórmulas de cementos refractarios, aplicados en el revestimiento de hornos y en equipos de producción de hierro y acero. Estos concretos son formulados con un bajo tenor de cemento y un alto tenor de alúmina, un subproduto de la industria del aluminio, muy resistente a las altas temperaturas.
Este reómetro fue desarrollado en el marco de un proyecto temático sobre concretos refractarios avanzados financiado por la FAPESP y coordinado por Victor Carlos Pandolfelli, del Departamento de Ingeniería de Materiales (Dema) de la UFSCar. Dicho proyecto abrió una línea de estudios que ya ha producido diez disertaciones de maestría y siete tesis doctorales, además de un libro que pasó a ser fuente de consultas en cursos sobre materiales. Y también posibilitó el registro de tres patentes. Una es la del propio reómetro, otra del software Particule Size Designer, que define y analiza los materiales en partículas utilizados en los cementos.
Lanzado el 23 de octubre por Alcoa, el software cuesta 800 reales, y los ingresos generados por las ventas irán a parar íntegramente a la UFScar. Dicho software también contribuyó para que se registrara la tercera patente: una generación de cementos refractarios con bajo tenor de agua en la preparación y una mayor resistencia mecánica a las altas temperaturas. El reómetro y otros equipamientos y procesos desarrollados surgen en un momento oportuno. En 2000, la producción mundial de acero fue de 847 millones de toneladas. La demanda actual de la siderurgia requiere cementos refractarios cada vez más resistentes y durables. Por lo tanto, la diferencia competitiva surgirá del desempeño y del valor agregado del material, y no solamente de la productividad. Pero una previsión es unánime: las siderúrgicas menos eficientes deberán cerrar su puertas, y este fenómeno ya empieza a verse en EE.UU.
El desafío de la industria del acero es reducir los costos y elevar los rendimientos. Para ello, son decisivos los refractarios, así como también las tecnologías que surgieron en los últimos años para elevar la eficiencia. “Los refractarios utilizados hoy”, dice Pandolfelli, “son una sofisticada clase de materiales, cuya concepción y proyecto de microestructura va mucho más allá de la clásica combinación de materias primas para obtener un mejor componente”. Las industrias están obrando correctamente al cambiar los viejos hornos de ladrillos refractarios por revestimientos de cemento refractario: “Con los ladrillos se gasta más tiempo y mano de obra, ya que son colocados uno por uno. El cemento refractario utiliza maquinarias rápidas, no necesita diferentes formatos de ladrillos para componer el horno y no deja juntas, por donde pueden desencadenarse procesos de corrosión.”
Se estima que, en el año 2007, la totalidad de los altos hornos y otras instalaciones de las acerías brasileñas estarán utilizando cementos refractarios. Actualmente, éstos corresponden al 60% del material refractario empleado en el sector, que mueve 350 millones dólares anuales. La calidad del refractario se revela en su resistencia a las temperaturas de la transformación de mineral en hierro y acero, que llegan a 1.600º C. Tres décadas atrás, el consumo de refractarios por parte de la siderurgia brasileña era de 30 kilogramos (kg.) por tonelada de acero producida. Actualmente, esta relación es de 9 kg., cercana a aquélla considerada excelente: 7 kg. Cuanto más eficiente y bajo control se encuentre el proceso siderúrgico, menor es el consumo de refractarios.
Con ello, la siderurgia brasileña se ha vuelto más competitiva. Pero, para mantener este nivel, e incluso superarlo, se ha estrechado el margen para estudios y experimentaciones: es necesario dominar y aplicar rápidamente formas de conocimiento cada vez más específicas. En este contexto, según Pandolfelli, el reómetro marcará la diferencia. Este instrumento constituye una parte fundamental en la producción de cementos refractarios bombeables, producidos en mezcladores en el propio local de la obra y transportados por mangueras a presión hacia el revestimiento de los altos hornos.
Nuevos tiempos
El reómetro mide el torque (esfuerzo de torsión) necesario para mezclar el cemento en diferentes condiciones, simulando el bombeo industrial. También indica el pH (índice de acidez) y la temperatura, según como van produciéndose las reacciones. De esta manera, dicho instrumento permite simular las solicitaciones a las que los cementos serán sometidos, desde el momento en que sus componentes son mezclados hasta su aplicación.
El ingeniero Carlos Pagliosa, actualmente empleado de Magnesita, el mayor fabricante brasileño de refractarios, fue uno de los primeros en trabajar con Pandolfelli, como alumno de posgrado, en el desarrollo de concretos bombeables. Para Pagliosa, los nuevos tiempos imponen el uso de productos multifuncionales y adecuados a un proceso de instalación más rápido, como lo es el sistema de bombeo. “Fue necesario tratar a los cementos refractarios como productos de alta tecnología. En ese contexto, los nuevos productos ya no pudieron ser generados mediante concepciones empíricas, por eso se emprendió el rumbo hacia el modelado computacional y el desarrollo de equipos específicos”, afirma Pagliosa.
La asociación de la UFSCar con Alcoa -que genera el 25% de la producción de aluminio en Brasil- nació hace diez años, período en el cual la empresa ha invertido 650 mil dólares en varios proyectos conjuntos. “Con elreómetro, la empresa espera diferenciarse al brindarle al mercado un instrumento de evaluación de la calidad de sus propias materias primas”, dice el químico Jorge Gallo, que comanda la investigación en la empresa y realiza la vinculación con la UFSCar, desarrollando su doctorado dentro del proyecto temático.
Menos esfuerzo
Los recursos invertidos por Alcoa en la UFSCar apoyan necesidades que el financiamiento de la FAPESP no puede atender, como la ampliación de los espacios físicos de la universidad. De esta manera, con recursos de la empresa, fue construida una unidad de 900 metros cuadrados en donde se encuentran los equipos y en donde trabaja el grupo implicado en este proyecto. Un ejemplo de los beneficios de Alcoa en la asociación se produjo durante el primer semestre, cuando ésta reformó uno de sus hornos de calcinación (quema) de alúmina. “Foi una operación de rutina, que se realiza una vez cada dos años. Pero esta vez fue diferente”, explica Jorge Gallo.
“Formamos un grupo con integrantes de la empresa, del Dema-UFSCar y del proveedor del refractario: Magnesita. Juntos, bajo la orientación del profesor Pandolfelli, pudimos organizar los trabajos de una manera mucho más fundamentada. Estimamos que esto nos permitirá agrandar el intervalo de tiempo entre las paradas de los equipos para su mantenimiento, cosa que, si se confirma, implicará una reducción considerable en los costos.”El proyecto también contribuyó para que Cerâmica Saffran, de Betim (Minas Gerais), se convirtiera en pionera en el uso de tecnología nacional para desarrollar concretos refractarios bombeables, incluso para reparar equipamientos siderúrgicos.
Con el equipo de la UFScar, la empresa logró mejorar el desempeño de los canales en los que el metal fundido se desliza hacia los altos hornos. El uso del reómetro redundó en el desarrollo del cementó refractario utilizado en estos canales. La empresa también economizó tiempo de desarrollo y gastos con tests industriales, que son caros, pues involucran una cantidad mínima de dos toneladas de material. De esta manera, la experiencia de Saffran, fundada en 1954, fue importante para comprobar la eficiencia del reómetro. Mientras el mercado brasileño de cementos refractarios apostaba firme a las maquinarias y tecnologías importadas, Saffran encontró un camino propio junto a la UFSCar.
Marcelo Guerra, ingeniero de investigación de la empresa, lo explica: “Nuestro nuevo cemento es bombeado con una mayor eficiencia, permitiendo así que el producto aplicado tenga una mejor calidad y desempeño. Como no necesitamos aplicar ninguna vibración -operación necesaria en el antiguo sistema de bombeo, para que el concreto fluyera con mayor facilidad-, redujimos en dos tercios el tiempo de operación. Un horno de 200 toneladas, por ejemplo, demandaba 72 horas de aplicación con vibración. Para el mismo volumen, ahora realizamos toda la operación en 20 horas”.
Concepción casera
Pagliosa, cuya tesis doctoral se focaliza en los cementos bombeables, agrega: “El desarrollo de la tecnología de cementos bombeables de Saffran fue efectuado dentro de la propia empresa, con el apoyo del equipo del proyecto temático de la FAPESP. No fue algo desarrollado dentro de la empresa y que migró hacia la universidad. La concepción del producto fue plasmada de forma conjunta por la empresa y la UFSCar; los tests de evaluación del producto por el reómetro y las discusiones técnicas fueron fundamentales para el éxito del desarrollo”.
Entre otros resultados delproyecto temático, Pandolfelli destaca otros cinco equipamientos que fueron construidos a lo largo de estos últimos cuatro años -algunos de ellos en fase prueba actualmente, para posibles pedidos de patentes. El equipo participante recibió nueve premios y publicó 71 artículos en revistas especializadas en Brasil y en el exterior. “Son resultados que muestran a las claras la generación de ciencia y sus aplicaciones”, completa Pandolfelli.
EL PROYECTO
Estudio Sistemático para el Desarrollo de Cementos Refractarios Avanzados
MODALIDAD
Proyecto Temático
COORDINADOR
Victor Carlos Pandolfelli – UFSCar
INVERSIÓN
R$ 525.877,47 y US$ 456.438,54