Esenciales para promover la movilidad eléctrica, las baterías de iones de litio logran concentrar gran cantidad de energía en un espacio reducido y pesan mucho menos que los modelos que utilizan otros materiales. Estas dos características – alta densidad energética y levedad – las convierten en las más utilizadas no solo en los vehículos eléctricos, sino también en teléfonos inteligentes y computadoras portátiles. Sin embargo, cuando llegan al final de su vida útil y son desechadas, se transforman en un problema ambiental. Para solucionarlo, grupos de investigación de todo el mundo estudian formas de reciclar y reutilizar los metales que componen estos módulos, entre los que se cuentan el cobalto, el litio, el cobre, el grafito y el aluminio. En Brasil, uno de los trabajos más avanzados se lleva a cabo en el Center for Advanced and Sustainable Technologies (Cast), de la Facultad de Ingeniería de la Universidade Estadual Paulista (Unesp) en la localidad de São João da Boa Vista (São Paulo).
“Nuestras técnicas permiten recuperar y reutilizar materiales potencialmente tóxicos, estimulando la economía circular. Esto hace posible reducir el impacto ambiental que generarían nuevas actividades con minerales”, subraya el ingeniero ambiental José Augusto de Oliveira, coordinador del Cast. Las metodologías en desarrollo utilizan procesos hidrometalúrgicos que implican la lixiviación, es decir, la separación de los metales contenidos en las baterías mediante su disolución continua en un medio acuoso.
Una batería de iones de litio está compuesta por varias pilas pequeñas denominadas celdas o células, que conforman un paquete mayor o pack, en la jerga de los ingenieros (lea en Pesquisa FAPESP, edición nº 261). La primera etapa de cualquier proceso de reciclado o reutilización de las baterías consiste en el desmembramiento del pack. El procedimiento más tradicional conlleva la detección de las celdas que aún son aptas para incluirlas en un nuevo paquete, dando origen a una batería de segunda vida. Las células que han llegado al final de su vida útil se desechan. En ellas se centra el trabajo de los investigadores del Cast.
La secuencia del proceso desarrollado en la Unesp, según describe DeOliveira, implica la separación de todos los componentes de las pilas, como los plásticos contenidos en la carcasa y utilizados como aislante entre la estructura metálica y el material interno. Este último está compuesto por el cátodo (el polo positivo de la batería) – una lámina de aluminio que contiene óxidos de litio y cobalto –, el ánodo (el polo negativo) – una lámina de cobre recubierta de grafito, y por una membrana plástica que separa los dos polos. Al hallarse en contacto con ambos polos, esta membrana puede contener grafito y óxidos metálicos.
La célula se desmantela en forma manual, con la ayuda de máquinas cortadoras. Las láminas metálicas obtenidas se someten a un baño en una solución química acuosa destinada a separar el cobre y el aluminio, que salen del proceso listas para su reutilización. En tanto, el grafito y los óxidos de litio y cobalto con alto grado de pureza se obtienen luego de filtrar las respectivas soluciones. El procesamiento de la membrana también requiere de un filtrado y de una etapa posterior de separación para purificar los óxidos metálicos presentes en ella.
“Los reactivos químicos utilizados proceden de fuentes orgánicas. Fueron seleccionados para minimizar el impacto ambiental y maximizar el beneficio económico y la seguridad laboral”, explica la química Mirian Paula dos Santos, investigadora responsable del proceso de remoción de los óxidos metálicos. “La tecnología se está perfeccionando. Solo al final del proceso podremos calcular su impacto ambiental y su factibilidad económica”, subraya. Por ahora, dice, la técnica ha sido validada a escala de laboratorio.

Campos de extracción de litio en el desierto de Atacama (Chile)LFREEDOM_WANTED / Alamy / Fotoarena
Según De Oliveira, el potencial económico de esta metodología es favorable. “Los estudios iniciales indican que la venta del óxido de litio genera fondos suficientes como para cubrir los gastos del reciclado”, dice. La fase actual de desarrollo de la técnica, para la que se ha depositado una solicitud de patente en el Instituto Nacional de la Propiedad Industrial (INPI) en 2020, proporciona una tasa de recuperación del 90 % del óxido de litio con un 98 % de pureza, mientras que cuando está contaminado con grafito, el índice de pureza es de un 50 %. Los demás componentes de la batería son totalmente recuperables, según un artículo publicado en 2021 en la revista científica Resources, Conservation and Recycling.
Estos resultados le han permitido a la Unesp firmar un convenio de desarrollo tecnológico y licencia de una versión de su proceso de reciclado, con nuevos reactivos, con una empresa brasileña de que opera globalmente. El propósito inicial es utilizar la tecnología para reciclar las baterías de los vehículos la compañía produce. Posteriormente, anticipa De Oliveira, la firma, cuyo nombre no puede revelarse por razones contractuales está evaluando una estrategia comercial con la Unesp para posibilitar la oferta de un servicio de reciclado integral a terceros. La cooperación entre la universidad y la multinacional cuenta con el aval de la FAPESP a través del Programa de Investigación en Asociación para la Innovación Tecnológica (Pite).
Otra técnica para el reciclado de las baterías de iones de litio en fase de desarrollo en el Cast sigue una vía no convencional, que utiliza agua en condición supercrítica como solvente para recuperar óxidos metálicos. “Para ello, hay que someter al agua a una temperatura superior a 374 grados Celsius [ºC] y a una presión de 240 atmósferas [atm]. Bajo estas condiciones, ya no existe diferencia entre su estado líquido y gaseoso”, explica el ingeniero químico Lúcio Cardozo Filho, responsable del proyecto de investigación. “El agua supercrítica sometida a una temperatura y presión extremas posee la reactividad adecuada para procesar, tratar y extraer compuestos inorgánicos, como los óxidos metálicos presentes en las baterías de litio”.
Aunque llevar el agua a la condición supercrítica no es trivial, el fluido utilizado, según Cardozo, no necesita ser de buena calidad, puede ser agua reutilizada y el proceso no utiliza ningún reactivo químico adicional para extraer los óxidos metálicos. “El porcentaje de éxito en la separación de metales es superior al 98 %”, informa el ingeniero. El resultado obtenido es una mezcla de óxidos metálicos conocida como black mass, que aún deberá ser sometida a un proceso de separación y purificación comúnmente utilizado en la hidrometalurgia convencional. “Nuestro próximo reto es conseguir fondos adicionales para poder ampliar la escala del proceso”, adelanta Cardozo Filho.
El reciclado de las baterías de iones de litio es un proceso más sostenible y económico que extraer los minerales de la naturaleza. En el caso del litio, se necesitan 100 kilogramos (kg) del mineral en bruto para producir 1,6 kg de litio. En cambio, en un proceso de reciclado pueden recuperarse 7 kg de óxido de litio por cada 100 kg de baterías. La extracción del mineral tiene un alto impacto ambiental por su uso intensivo de agua, sin contar que el proceso de refinado es electrointensivo, en el cual los materiales rocosos deben calentarse a temperaturas superiores a 1.000 ºC, lo que consume mucha energía.
Según un estudio de la consultora McKinsey, se prevé que la demanda mundial de almacenamiento en baterías de litio crezca de 700 gigavatios hora (GWh) en 2022 a 4.700 GWh en 2030. El aumento de la demanda, dicen los expertos, hace que prevalezca la recuperación y reutilización de los materiales metálicos que componen estas baterías.
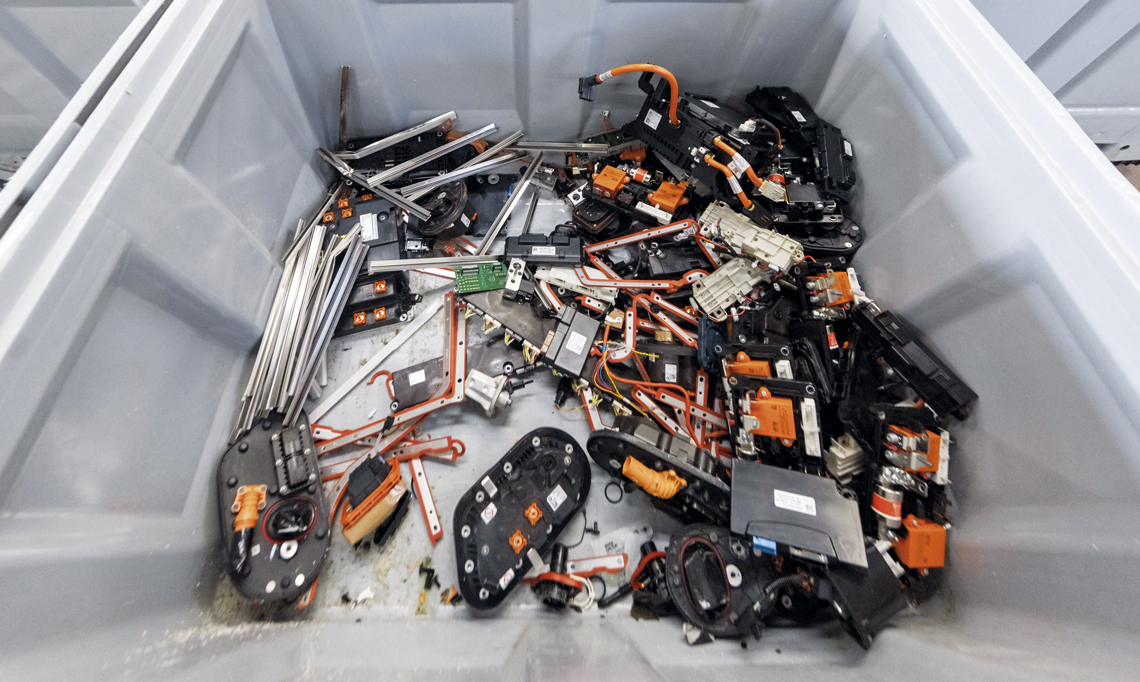
Baterías de litio al final de su vida útil, desguazadas y listas para su reciclado en una empresa de Hamburgo (Alemania)Markus Scholz / Picture Alliance via Getty Images
El sector automotor es el destino principal de las baterías de litio, ya que alrededor de un 80 % de la producción se destina a los fabricantes de automóviles. Una batería típica para vehículos eléctricos pesa más de 200 kg y tiene una vida útil de entre 8 y 10 años. La Agencia Internacional de la Energía (AIE) estima que la producción de litio deberá multiplicarse casi por diez de aquí a 2050 para poder satisfacer el aumento de la demanda mundial del producto.
“La producción de insumos corre el riesgo de no seguir el ritmo de la creciente demanda mundial. El resultado es que podríamos tener escasez de baterías en 2030”, advierte el físico Hudson Zanin, de la Facultad de Ingeniería Eléctrica y Computación de la Universidad de Campinas (Feec-Unicamp), coordinador de una investigación que apunta al desarrollo de una batería a base de sodio (lea en Pesquisa FAPESP, edición nº 329). “El reciclado y la integración progresiva de los materiales recuperados en las nuevas baterías proporciona ventajas tanto desde el punto de vista ambiental como económico, garantizando el suministro de insumos”, sostiene.
Zanin explica que los principales procesos de reciclado utilizados en todo el mundo son pirometalúrgicos e hidrometalúrgicos, y, según el investigador, alcanzan una eficiencia superior al 80 %. En la pirometalurgia, la incineración del material puede liberar gases tóxicos, algo indeseable.
En tanto, los procesos hidrometalúrgicos, si bien consumen agua, contaminan menos y requieren menos energía. “El consumo de agua es mucho menor que el de la minería del litio. En los procesos hidrometalúrgicos de reciclado se utilizan unos 5 litros [l] de agua para obtener 100 gramos [g] de sales de litio. En la minería, el consumo de agua puede variar de 50 a 90 l para obtener 100 g de carbonato de litio”, informa De Oliveira.
La reelaboración de baterías en nuevos packs que aprovechan las células que han perdido rendimiento pero aún no han llegado al final de su vida útil es objeto de un proyecto en desarrollo en el centro de innovación CPqD de Campinas (São Paulo) en colaboración con las empresas CPFL Energia y la china BYD, fabricante de baterías y vehículos eléctricos.
Tal como lo explica el ingeniero Aristides Ferreira, gerente de soluciones de sistemas de energía de CPqD, las baterías utilizadas en los vehículos eléctricos son de tracción, es decir, se emplean para impulsar al vehículo y, para tal fin, están sometidas a intensas condiciones de funcionamiento. Tras un período que puede variar entre 8 y 10 años, dependiendo del uso, pierden su capacidad de almacenar energía y generar la tracción necesaria como para mover un vehículo. Pero todavía pueden ser útiles en aplicaciones de menor exigencia, tales como baterías estacionarias, sistemas de respaldo y módulos de almacenamiento de energía de fuentes de generación solar y eólica, que son intermitentes. Permiten, por ejemplo, acumular la energía generada durante el día por un panel solar fotovoltaico para utilizarla por la noche o la energía de una fuente eólica cuando no hay viento.
El proyecto de CPqD implicó la creación de algoritmos capaces de comprobar la calidad de las celdas extraídas de una batería vehicular de iones de litio y determinar su longevidad, sin necesidad de largos ensayos de laboratorio, lo que facilitó la selección de las mejores células para una segunda vida en baterías estacionarias. CPqD ha desarrollado un prototipo de batería de segunda vida que se encuentra en fase de prueba en un laboratorio que cuenta con una planta generadora de energía fotovoltaica en la Unicamp.
Proyecto
Una tecnología para el reciclado de baterías de iones de litio: aplicaciones de ingeniería del ciclo de vida a la luz de la economía circular (nº 20/11874-5); Modalidad Asociación para la Innovación Tecnológica (Pite); Investigador responsable José Augusto de Oliveira (Unesp); Inversión R$ 198.854,94.
Artículo científico
SANTOS, M. P. et al. A technology for recycling lithium-ion batteries promoting the circular economy: The RecycLib. Resources Conservation and Recycling. dic. 2021.