El sector del transporte, que ha sido señalado como uno de los principales responsables de la emisión de gases de efecto invernadero, que causan el calentamiento global, está buscando formas de volverse más sostenible y ha venido invirtiendo en productos y procesos con menor impacto ambiental. La industria del automóvil ha echado mano de una alternativa que está consolidándose en todo el mundo: el empleo de fibras naturales de origen vegetal en la fabricación de piezas y accesorios. Más que un simple proveedor de materias primas, Brasil es uno de los centros de investigación y desarrollo de esta tecnología.
En agosto, la Universidade Estadual Paulista (Unesp) suscribió un convenio con Volkswagen de Brasil para el desarrollo de nuevos compuestos que incluyan en su fórmula fibras vegetales. Los compuestos son materiales constituidos por dos o más componentes, como vidrio y metal, con propiedades superiores a los que les han dado origen. El propósito es que estos nuevos materiales se utilicen en la elaboración de piezas del acabado interno de los automóviles que produce el fabricante.
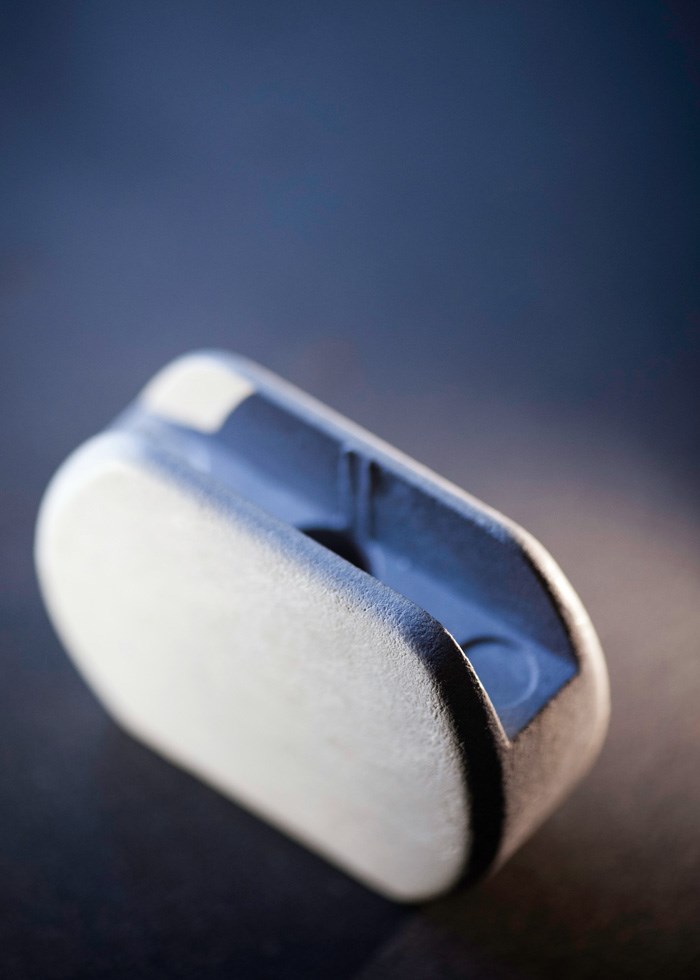
Léo Ramos Chaves / Revista Pesquisa FAPESPUna pieza de automóvil fabricada con un biocompuestoLéo Ramos Chaves / Revista Pesquisa FAPESP
El proyecto es liderado por el ingeniero agrónomo Alcides Lopes Leão y la química Ivana Cesarino, coordinadores del Laboratorio de Bioprocesos y Biotecnología de la Facultad de Ciencias Agrarias de la Unesp, en la localidad de Botucatu (São Paulo), y tiene una duración de 18 meses. Al final del período, la multinacional espera contar con piezas más sostenibles, a raíz de la reducción del uso de plásticos de origen fósil en su composición y, sobre todo, con automóviles más livianos y eficientes desde el punto de vista energético. La ventaja principal de la sustitución de insumos minerales por fibras vegetales –materiales de menor densidad– es la reducción del peso del vehículo y, por ende, del consumo de combustible. Con todo, será necesario aún superar algunas limitaciones, entre ellas la escasa resistencia a la humedad que presentan las fibras naturales, su susceptibilidad al ataque de hongos y su durabilidad.
Lopes Leão estudia el uso de fibras vegetales en materiales compuestos desde la década de 1990. La colaboración actual con Volkswagen es la herencia de un proyecto financiado por la FAPESP en 2000 (lea en Pesquisa FAPESP, edición nº 104). En aquella época, él investigaba el potencial de la fibra de curauá (Ananas erectifolius), una planta originaria de la selva amazónica que había conocido cuando pescaba en los ríos de la región.
El proyecto despertó el interés de Volkswagen, que llegó a producir algunas partes de automóviles con esas fibras, y el investigador fue invitado a impartir conferencias sobre el tema a los ingenieros de la empresa en Brasil y Alemania. Pero la ensambladora no pudo hallar un proveedor regular de curauá y archivó el proyecto. Dos décadas después, Lopes Leão quedó sorprendido ante una nueva invitación. “Ya no tenía contacto con nadie de la empresa. Ellos decidieron invertir en la producción de piezas elaboradas con fibras vegetales y me localizaron este año buscándome en internet”, relata el investigador.
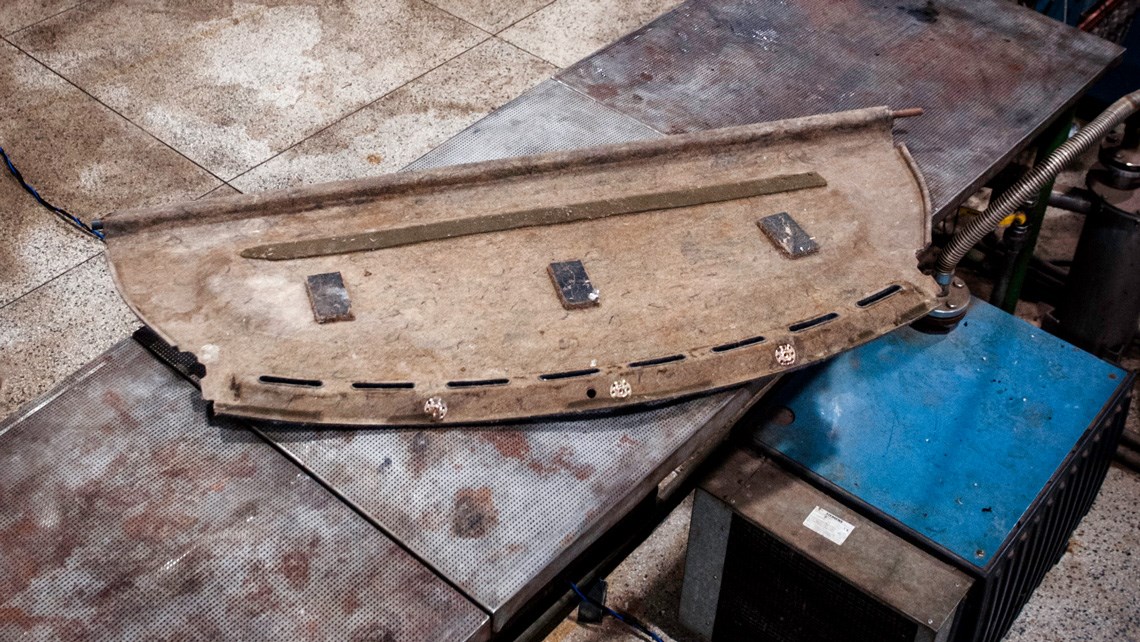
Léo Ramos Chaves / Revista Pesquisa FAPESPCuerpos de prueba para ensayos elaborados con bambúLéo Ramos Chaves / Revista Pesquisa FAPESP
Ahora, para definir cuál es la mejor fibra para incorporarla al plástico, se están probando cuatro opciones: coco, yute, sisal y bambú. La cuestión del suministro va a pesar en la decisión, que el investigador considera lo más acertado. “Como el proyecto actual tiene un alcance mundial, Alemania puede contar con proveedores de fibras de diversos países”, considera. En una primera etapa, las fibras se incorporarán al polímero a escala nanométrica en seis piezas que forman parte del maletero del modelo Polo de la compañía. Más adelante, la idea es trabajar a escala nanométrica. “La incorporación de nanocelulosa duplica la resistencia del compuesto”, explica Lopes Leão.
Según el investigador, algunos fabricantes de automóviles ya utilizan las fibras naturales a escala reducida en diversos tipos de compuestos. “La mayor consumidora es la empresa alemana Mercedes-Benz, que emplea alrededor de 30 kilos de fibras por vehículo. En Volkswagen empezaremos con 8 kilos por vehículo, aproximadamente. Si se piensa que la empresa produce 6 millones de autos por año, el volumen puede llegar a ser considerable”, dice. En estos materiales compuestos, el polímero funciona como la matriz responsable de su estructura, y la fibra es el elemento de refuerzo. Si las piezas de los automóviles se confeccionaran únicamente con fibra, esta no podría aportarle la resistencia que el material necesita.
El desarrollo de materiales de alto rendimiento para la industria automotriz a partir de materias primas regionales también es el propósito de un equipo de las universidades federales de Paraíba (UFPB) y de Campina Grande (UFCG) y del Instituto Fraunhofer para Tecnología de Manufactura y Materiales Avanzados, con sede en Bremen (Alemania). El proyecto está financiado por la Fundación de Apoyo a la Investigación Científica del Estado de Paraíba (Fapesq) y por el Ministerio de Educación e Investigación de Alemania. En Brasil, su coordinación está a cargo de la ingeniera de materiales Renate Wellen, del Departamento de Ingeniería de Materiales de la UFPB.
Las autopartes hechas con fibras vegetales son más livianas y redundan en un menor consumo de combustible
Los investigadores iniciaron el proyecto trabajando con fibras de sisal, en Brasil, y de lino, en Alemania. “Las mejores propiedades se obtuvieron con el lino, que se moldea mejor como tejido para incorporarlo al compuesto por compresión. El objetivo es utilizar el material en la parte interna de la puerta, elegida por la alta demanda de la industria y porque es una estructura de menor complejidad”, revela Wellen.
Al igual que en el proyecto de la Unesp con Volkswagen, la alianza entre brasileños y alemanes nació de búsquedas realizadas en internet. En este caso, la iniciativa partió del lado brasileño. En 2015, empeñada en el desarrollo de proyectos en el área de las fibras vegetales y conocedora del interés creciente de Alemania por la tecnología verde, la investigadora de la UFPB se contactó con diversas universidades e institutos de investigación germanos.
De esos contactos surgió la posibilidad de realizar un posdoctorado en el Instituto Fraunhofer de Tecnología de Manufactura y Materiales Avanzados de Bremen que derivó en el proyecto actual. Para Wellen, coordinadora general de investigaciones de la UFPB, el intercambio de experiencias entre los equipos es uno de los aspectos más importantes del convenio. “Ello generó mejoras en la capacitación de los alumnos. Dos integrantes del equipo están realizando sus doctorados en Alemania”.
El nuevo polímero reforzado con fibras naturales está a punto de ultimarse y el prototipo de una autoparte fabricada con este material fue presentado en octubre en la Feria K 2022, el mayor evento internacional de la industria del plástico y el caucho, realizada en Düsseldorf (Alemania). Ya hay perspectivas de desarrollo de un nuevo material compuesto, cuya fórmula posiblemente incluya fibra de coco, una materia prima abundante en Brasil. “Los alemanes están interesados en continuar con la colaboración”, dice Wellen.
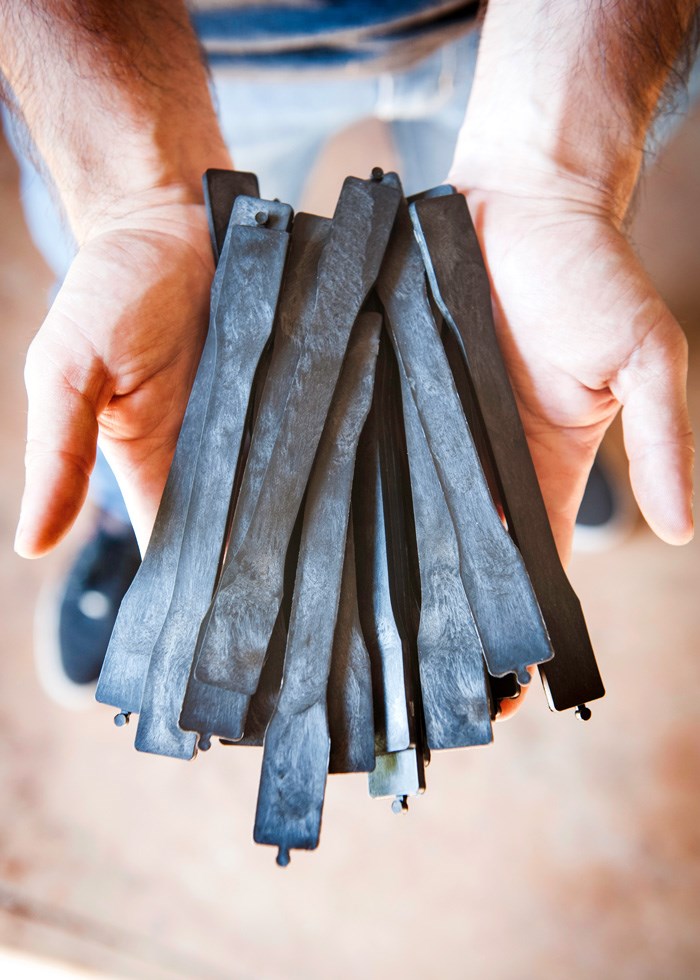
Léo Ramos Chaves / Revista Pesquisa FAPESPCompuesto elaborado con fibras naturales sometido a un test de resistenciaLéo Ramos Chaves / Revista Pesquisa FAPESP
Del automóvil de soja al fibrocemento
El intento de utilizar fibras naturales en el sector automotor es de larga data. En 1930, Henry Ford, pionero de la producción de automóviles en serie, creó un material bautizado como bioplástico. Su composición exacta es incierta, porque no se conservaron registros de su fórmula, pero un prototipo fabricado con ese material en 1941 pasó a la historia con el nombre de Soybean Auto, que significa automóvil de soja. Empero, el nuevo coche nunca fue incorporado a la línea de producción de la fábrica.
Según la información disponible en el Benson Ford Research Center, el instituto de investigación dependiente del Museo Henry Ford, el estallido de la Segunda Guerra Mundial (1939-1945) suspendió la totalidad de la producción de automóviles en Estados Unidos. A raíz de ello, el experimento del auto de soja no prosperó. Posteriormente, los esfuerzos de la empresa se centraron en la recuperación de las pérdidas ocasionadas por la guerra y el automóvil de bioplástico cayó en el olvido.
Para el ingeniero químico Sandro Amico, coordinador del Grupo de Materiales Compuestos y Nanocompuestos de la Universidad Federal de Rio Grande do Sul (UFRGS), otro factor que contribuyó al desinterés de la industria fue la aparición de las fibras de vidrio y de carbono en las décadas de 1930 y 1950, respectivamente. Él explica que las fibras sintéticas ofrecían ventajas tales como su alta rigidez y una mayor resistencia mecánica a los ataques químicos y ambientales, mientras que las naturales eran susceptibles a la humedad, por ejemplo. Hoy en día, este problema puede subsanarse con el tratamiento de las fibras, o bien mediante el uso de aditivos en la fórmula del compuesto, y la preocupación por el medio ambiente ha traído nuevamente a escena a las fibras naturales en el ámbito industrial.
Desde hace más de dos décadas, Amico trabaja con diferentes tipos de fibras. “Actualmente hay varios ejemplos de aplicaciones que hasta hace cinco años no existían y otras cuya escala se ha incrementado”, afirma el profesor. Cita como ejemplo a la madera plástica, conocida como WPC (wood-polymer composite), que surgió en la década de 1960 y está compuesta por aserrín de madera y una resina polimérica termoplástica, como PVC o polietileno. “Este material ha tenido un gran éxito comercial en América del Norte”, dice.
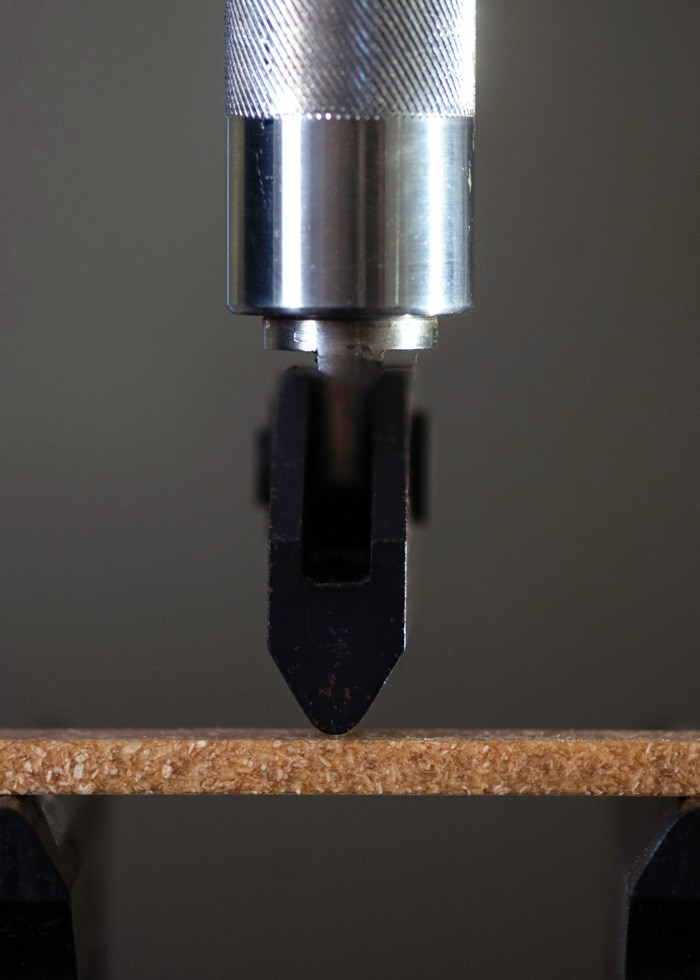
Léo Ramos Chaves / Revista Pesquisa FAPESPSoporte para vidrios fabricado con fibra de maderaLéo Ramos Chaves / Revista Pesquisa FAPESP
En la Universidad Tecnológica Federal de Paraná (UTFPR), los alumnos del ingeniero forestal Ugo Leandro Belini, del Departamento de Diseño Industrial y de Posgrado en Sostenibilidad Ambiental Urbana, estudian cómo elaborar productos más sostenibles, como lámparas y gafas. Uno de ellos ha despertado el interés de una empresa local. “En un trabajo de investigación de finalización de carrera, crearon un marco de anteojos a partir de un compuesto de partículas de bagazo de caña de azúcar teñido con un colorante natural, la cúrcuma, y aglutinadas con resina de poliuretano de ricino”, comenta Belini.
Según un estudio de mercado publicado en 2020 por la empresa de consultoría estadounidense Grand View Research, el mercado de los compuestos fabricados con fibras naturales está creciendo en todo el mundo. La empresa estima que el sector alcanzará en 2024 una valuación de 10.900 millones de dólares. El área que más emplea estos materiales es la de la construcción civil, que representa más de la mitad de la demanda. En el exterior, el material más consumido es la madera plástica WPC, que se utiliza en baldosas y entarimados, marcos de puertas y ventanas y revestimientos. Las fibras también se emplean como compuesto en elementos estructurales de hormigón.
En Brasil, las tejas de fibrocemento hechas con una mezcla de cemento y amianto, una fibra mineral reconocidamente cancerígena, se prohibieron en 2017, lo que ha dado lugar a nuevos compuestos de origen vegetal. Responsable del desarrollo de una teja de fibrocemento fabricada con pulpa de celulosa patentada en 2012, el ingeniero civil Holmer Savastano Junior, de la Facultad de Zootecnia e Ingeniería de Alimentos de la Universidad de São Paulo (FZEA-USP), dirige un proyecto para la producción de placas cementicias reforzadas con una estructura tridimensional (3D) de yute y malva.
Según el investigador, quien desde la década 1990 estudia el uso de fibras vegetales en la producción de tejas (lea en Pesquisa FAPESP, edición nº 98), las tejas de tejido de yute y malva yuxtapuestas y conectadas entre sí perpendicularmente forman una estructura que proporciona liviandad y una mayor resistencia mecánica y química que el producto patentado hace una década. El proyecto cuenta con el apoyo de la FAPESP y de la Fundación de Apoyo a la Investigación Científica del Estado de Amazonas (Fapeam), en el marco de un acuerdo de cooperación científica con participación de investigadores de la USP y de la Universidad Federal de Amazonas (Ufam).
“El equipo de Amazonas posee experiencia en matrices poliméricas y nosotros en capas de fibrocemento. Nos complementamos e intercambiamos experiencias enriquecedoras”, dice Savastano. Tras la prohibición del uso del amianto, él vislumbra buenas perspectivas de comercialización de las nuevas placas. “Como ya no existe el riesgo de toxicidad, este tipo de fibrocemento también ha sido considerado para usos internos, en tabiques divisorios de ambientes, cielorrasos y baldosas, lo que puede elevar la demanda del nuevo producto en el segmento de la construcción”.
Proyectos
1. Producción de compuestos a base de fibras naturales (nº 06/06464-1); Modalidad Programa de Investigación en Asociación para la Innovación Tecnológica (Pite); Investigador responsable Alcides Lopes Leão (Unesp); Inversión R$ 242.035,63.
2. Desarrollo de paneles sándwich sostenibles con placas cementicias reforzadas con tejido 3D de yute y malva y alma polimérica (nº 20/08975-4); Modalidad Ayuda de Investigación – Regular; Convenio Fapeam; Investigador responsable Holmer Savastano Junior (USP); Inversión R$ 152.568,94.
Artículo científico
JÚNIOR, I. B. et al. Fibras vegetais e compósitos na indústria automotiva. Mix Sustentável, v. 6, n. 4. ago. 2020.